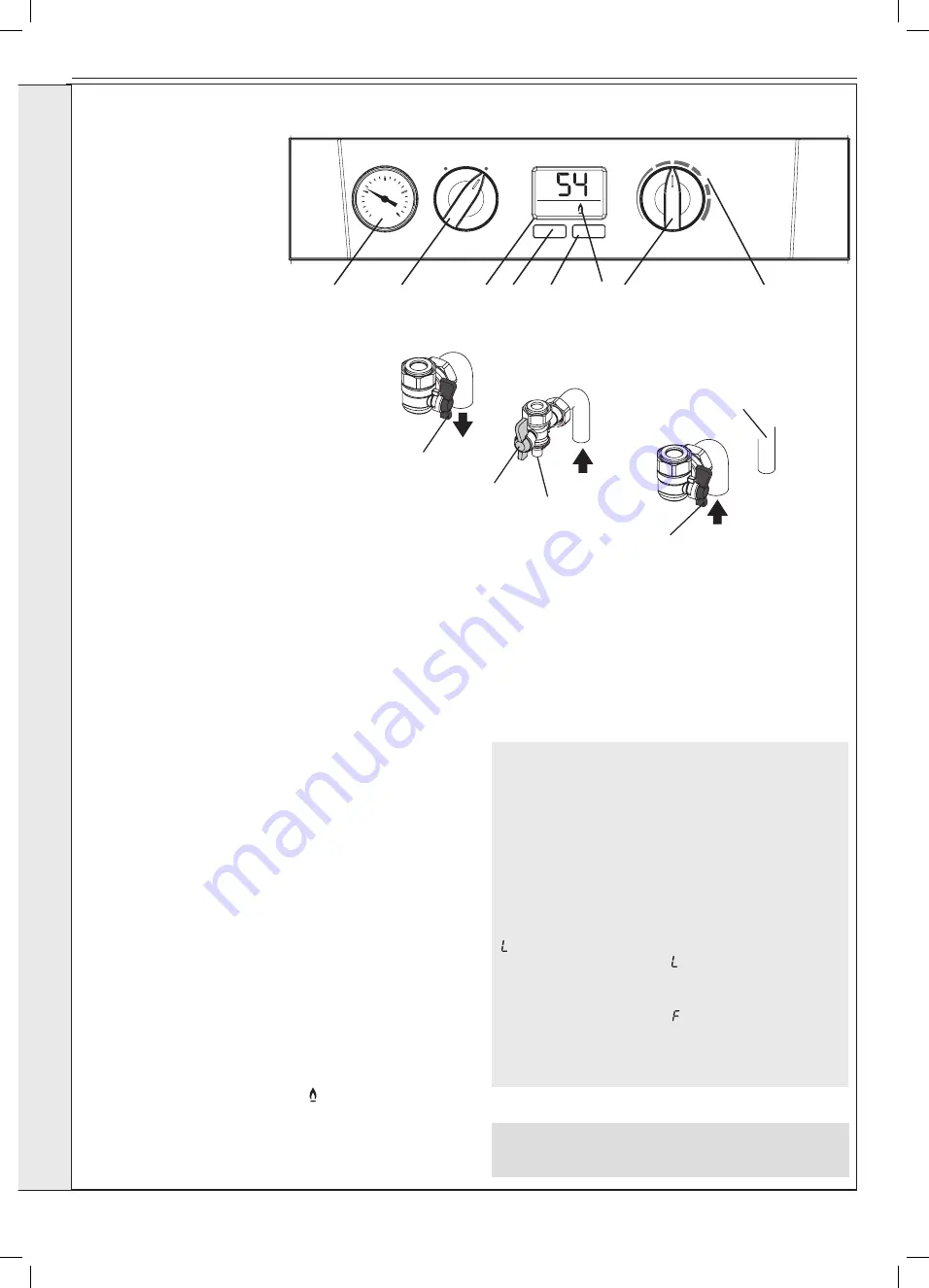
36
Installation and Servicing
SECTION 2 - INSTALLATION
2.23 INITIAL LIGHTING
THE DISPLAY
The user control has one display to inform the user about
the status of the boiler. The LCD Display shows the status
of the flame. If no flame is detected the flame symbol
will not be visible. When the flame is detected the flame
symbol will be visible permanently.
Below is a list with display function in normal operation.
0 0
Standby, no demand for heat present.
ON
There is a demand for heat.
F P
Boiler is active for boiler frost protection.
Boiler is in lockout for a specific error. Display will
show a number after the “ ” to indicate which error is
detected.
F
Boiler has a fault for a specific error. Display will
show a number after the “ ” to indicate which error is
detected.
Note:
Boiler frost protection - boiler operates if the
ambient temperature is below 5ºC until it reaches 19ºC.
Legend
A. Central Heating Temperature Knob
B. Mode Knob
C. Boiler Status
D. Burner ‘on’ indicator
E. Central Heating Economy Setting
F. CH Flow Isolating Valve
G. System Pressure Gauge
H. Gas Inlet Pressure Test Point
J. Gas Service Cock
K. CH Return Isolating Valve
L. Drain Valve
M. Function Button
N. Restart Button
1.
Check that the system has been filled and that the boiler is not
airlocked. Ensure the automatic air vent cap is open. Refer to
Section 2.16.
Note.
It is important the burner is not operated before the system is fully
vented of air. If it is necessary to operate the appliance pump to
assist venting of the air this must be done with the gas service cock
turned off.
2.
Refit the boiler front panel. Refer to Section 3.2.
3.
Check that the drain valve (L) is closed and that the CH isolating
valve (F and K) are OPEN.
4.
Check that the electrical supply is OFF.
5.
Check that the boiler mode control knob (B) is OFF.
6.
Check that the gas service cock (J) is OPEN.
7.
Slacken the screw in the inlet pressure test point (H) and connect
a gas pressure gauge via a flexible tube.
8.
Switch the electricity supply ON and check all external controls
are calling for heat.
CENTRAL HEATING
9.
Set the CH temp control (A) to “
MAX
” and turn the mode knob
(B) to “
BOILER ON
”. The boiler control should now go through
its ignition sequence until the burner is established.
10.
If the boiler does not light after 5 attempts the boiler will lock out
and display fault code
L 2
.
Restart the boiler (Refer to Section 2.25). The boiler will repeat
its ignition sequence. If restart occurs 5 times within 15 minutes
then
LC
will be shown.
If power is removed this will be reset.
When the burner is established the ‘ ’ will be shown on the display
with the ‘ON’ indicating central heating operation and the current
flow temperature shown in the 2 digit display.
11.
Ensure that with the boiler operating the dynamic gas pressure
is able to obtain maximum output. Refer to Table 2.
IMPORTANT
The gas input to the burner is regulated by the gas
valve according to the air flow produced by the fan.
It is NOT
user-adjustable. Any interference to sealed
settings on the gas valve will adversely affect operation
and render our warranty void.
For additional gas supply information refer to “Gas Supply”
on page 12.
Note. The boiler incorporates a fan overrun cycle which
MUST NOT be prematurely interrupted by isolation of the
mains electricity supply.
ºC
ON
A
B
E
C
D
MIN
e
RESTART
MAX
BOILER
OFF
BOILER
ON
CH Flow
Gas Supply
CH Return
Safety
Drain
Valve
F
J
L
H
K
Note. Valves shown are in the open position.
G
B
C M
N
A
D
E
INST
ALLA
TION
Summary of Contents for LOGIC SYSTEM S15IE
Page 4: ...4 Installation and Servicing...
Page 6: ...6 Installation and Servicing...
Page 60: ...60 Ideal Logic System Installation and Servicing...
Page 61: ...61 Installation and Servicing...
Page 68: ...68 NOTES Ideal Logic System Installation and Servicing...
Page 69: ...69 NOTES Ideal Logic System Installation and Servicing...
Page 70: ...70 NOTES Ideal Logic System Installation and Servicing...
Page 71: ...71 NOTES Ideal Logic System Installation and Servicing...
Page 80: ......