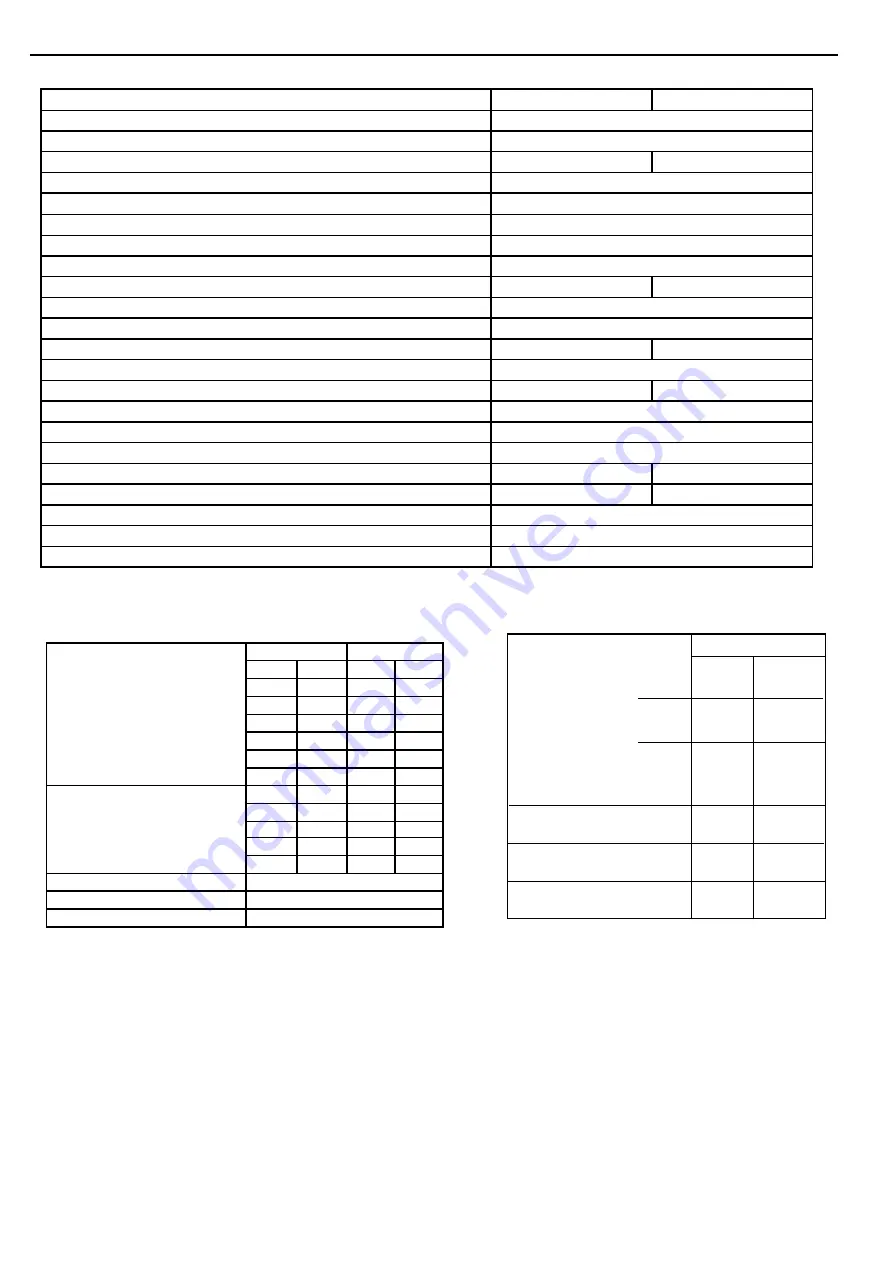
4
SECTION 1 - GENERAL
Note.
Gas consumption is calculated using a
calorific value of 95.65 MJ/m
3
(2569 Btu/ft
3
) gross
or 88 MJ/m
3
(2360 Btu/ft
3
) nett
To obtain the gas consumption at a different
calorific value:
a.
For l/s
- divide the gross heat input
(kW) by the gross C.V. of the gas (MJ/m
3
)
b.
For ft
3
/h
- divide the gross heat input (Btu/h)
by the gross C.V. of the gas (Btu/ft
3
)
c. For m
3
/h
- multiply l/s by 3.6.
Key to symbols
C
13
C
33
=
A room sealed appliance designed for connection via ducts to a
horizontal or vertical terminal, which admits fresh air to the burner
and discharges the products of combustion to the outside through
orifices which, in this case, are concentric. The fan is up stream of
the combustion chamber.
I
3P
= An appliance designed for use on 3rd Family gas, Group P only.
* The value is used in the UK Government’s Standard Assessment Procedure (SAP) for energy rating of dwellings. The test data from
which it has been calculated have been certified by a notified body.
Table 1 - General Data
Maximum DHW Input :
24 30
Nett CV
kW
24.3
30.4
Btu/h 82,912 103,725
Gross CV
kW
26.4
33
Btu/h 90,077 112,596
Gas Consumption
m
3
/h 1.00
1.25
ft
3
/h 35.33 44.20
kg/h 1.83
2.26
Maximum
kW
24.2
30.3
DHW Output
Btu/h
82,570
103,384
DHW Flow Rate
l/min
9.9
12.4
at 35°C temp. rise.
gpm
2.2
2.8
DHW Specific Rate
l/min
11.5
14.5
gpm 2.5
3.2
Table 2 - Performance Data - Central Heating
Table 3 - Performance Data - Domestic Hot Water
*Required for maximum flow rate. Boiler operates down to 2 l/min DHW delivery
Ideal
GB
Series III
24
30
Gas Supply
I
3P
- G31 - 37mbar
Gas Supply Connection
15mm copper compression
Injector Size
mm
3.3
3.75
Inlet Connection
Domestic Hot Water
G ½
Outlet Connection
Domestic Hot Water
G ½
Flow Connection
Central Heating
G ¾
Return Connection
Central Heating
G ¾
Flue Terminal Diameter
mm
100
Average Flue Temp-Mass Flow Rate
DHW
63ºC - 11g/s
68ºC - 13 g/s
Maximum Working Pressure (Sealed Systems)
bar (lb/in
2
)
2.5 (36.3)
Maximum Domestic Hot Water Inlet Pressure
bar (lb/in
2
) (kPa)
10.0 (145) (1000)
Minimum Domestic Hot Water Inlet Pressure*
bar (lb/in
2
) (kPa)
0.8 (11.6) (80)
1.3 (18.9) (130)
Electrical Supply
230 V - 50 Hz.
Power Consumption
W
79
79
Fuse Rating
External : 3A Internal : T4H HRC L250 V
Water Content
Central Heating litre (gal)
1.2 (0.26)
Domestic Hot Water litre (gal)
litre (gal)
0.5 (0.11)
Packaged Weight
kg
32.9
32.9
Maximum Installation Weight
kg
30
30
Boiler Casing Size
Height mm
700
Width mm
395
Depth mm
285
Max.
Min.
Boiler Input :
24
30
24
30
Boiler Input ‘Q’
Nett CV kW
17.3
20.4
4.9
6.1
Btu/h
59030
69607
16720
20814
Gross CV kW
18.8
22.2
5.3
6.6
Btu/h
64148
75749
18084
22520
Gas Consumption
m
3
/h
0.71
0.82
0.20
0.25
ft
3
/h
25.1
29.0
7.1
8.8
Boiler Output :
Non Condensing
kW
17.2
20.4
4.9
6.1
70
o
C Mean Water temp. Btu/h
58688
16720
16720
20814
Condensing
kW
18.2
21.6
5.15
6.45
40
o
C Mean Water temp. Btu/h
62100
73702
17572
22008
Seasonal efficiency*
SEDBUK 2005
24kW = 91.0 30kW = 91.1
Seasonal efficiency*
SEDBUK 2009
24kW = 88.9 30kW = 89.5
NOx Classification
CLASS 6