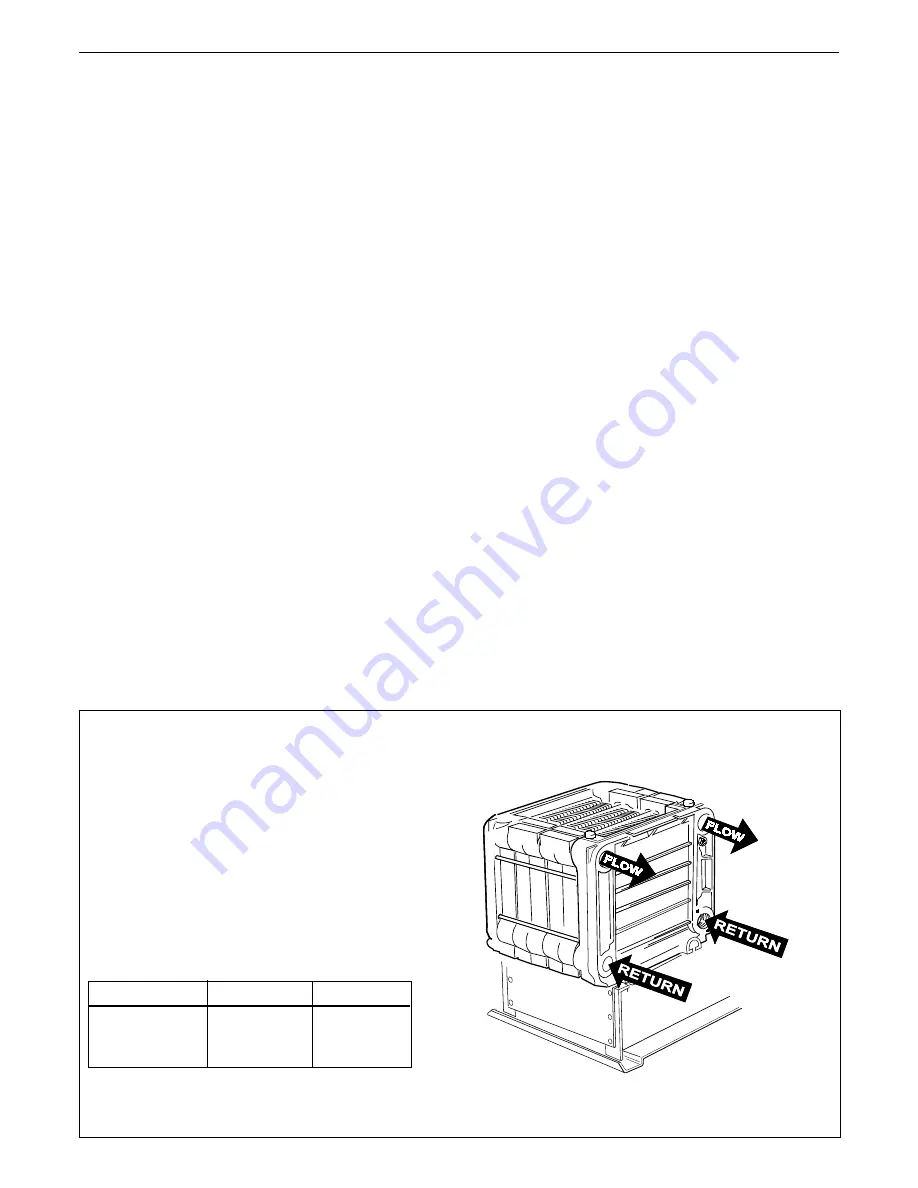
4
Concord CXSD/H -
Installation & Servicing
GENERAL
Flow and return connections are 2" BSP.
A 1" BSP tapping is provided in the redundant return flange for
the cold feed or expansion vessel connection.
Safety Valve
A safety valve must be sized and fitted in accordance with BS.
6644 for every type of system. The valve should be set at 0.7
bar (10 lb/in.
2
) above the operating pressure in the boiler. The
maximum safety valve setting is 0.7 bar (10 lb/in.
2
) above the
maximum design operating pressure of 6 bar (87 lb/in.
2
).
Cold Feed/Open Vent
The independent cold feed and the open vent must comply
with BS. 6644 and be of the following minimum size.
Boiler Size
Cold Feed
Open Vent
CXSD 40/H - 50/H
3/4
"
1"
CXSD 60/H-120/H
1"
1
1/4
"
Sealed system filling point - refer to Frame 8
1
WATER CONNECTIONS
GAS CONTROLS
The gas controls consist of a high / low arrangement with
direct burner ignition.
ELECTRICAL CONTROLS
WARNING. THE
ON/STANDBY [1/0] button does
NOT
electrically
isolate the boiler.
The
CXSD/H
incorporates an advanced microprocessor based
control system which operates all electrical functions of the boiler
including ignition, flame detection, thermostatic control, and high/
low operation. In addition, the microprocessor has onboard
servicing and commissioning instructions and a fault diagnosis
programme.
The illuminated LED display gives a continual read-out of the boiler
status and functions, but in the unlikely event of a fault condition
will display the fault areas.
OPTION KITS
Pressure Gauge Kit
A pressure gauge is available for the range of boilers. Details
for fitting are included with the pressure gauge.
Downdraught thermostat
This kit is optional when used on a single CXSD/H installation,
but mandatory when used on a multiple boiler installation.
Remote Indication Board (volt free)
This provides the ability for remote indication of lockout and
overheat conditions.
Outside Sensor
This kit provides a sensor for temperature compensation when
the outside temperature changes
DUTY
The range of boilers is suitable for: Combined indirect pumped
domestic hot water
and
central heating systems; Independent
indirect pumped domestic hot water
or
central heating systems.
Fully pumped systems may be open vented or sealed.
The range of boilers is NOT suitable for:
1.
Gravity DHW systems.
2.
Gravity heating systems.
3.
Direct domestic hot water supply.
WATER CIRCULATION SYSTEM
Due to the compact nature of the boiler the heat stored within the
castings at the point of shutdown of the burner must be dissipated
into the water circuit in order to avoid the overheat thermostat
tripping. In order to allow pump operation after burner shutdown
the boiler control box incorporates a pump overrun facility which
operates when the boiler switches off and until the flow temperature
is below 75
0
C and, in order to make use of this, the pump must be
wired to the appropriate terminal L
2
(pump) in the boiler control
box.
1.
The minimum flow rate as given in Table 5 must be maintained
whenever the boiler is firing and during the pump overrun
period.
2.
During the period of pump overrun there must be an open
circuit of adequate water volume and/or load. The minimum
size of this circuit is given by the use of Graph 1.
Examples shown on Graph 1
a.
For the
CXSD 90/H
and
CXSD 100/H
the minimum circuit
during pump overrun could be a load of 6 kW with a volume
of 31 litres or any other combination given by the relevant
line.
b.
For the
CXSD 70/H
and
CXSD 80/H
the minimum circuit
during pump overrun could be a load of 2 kW with a volume
of 45 litres or any other combination given by the relevant
line.
The above circuit capacity during pump overrun may be
achieved either by provision of an adequate bypass circuit or
by ensuring that a zone of suitable size is open for circulation
during this period by relevant control of zone valves or pumps.
continued on page 6
Summary of Contents for Concord CXSD 100
Page 1: ......