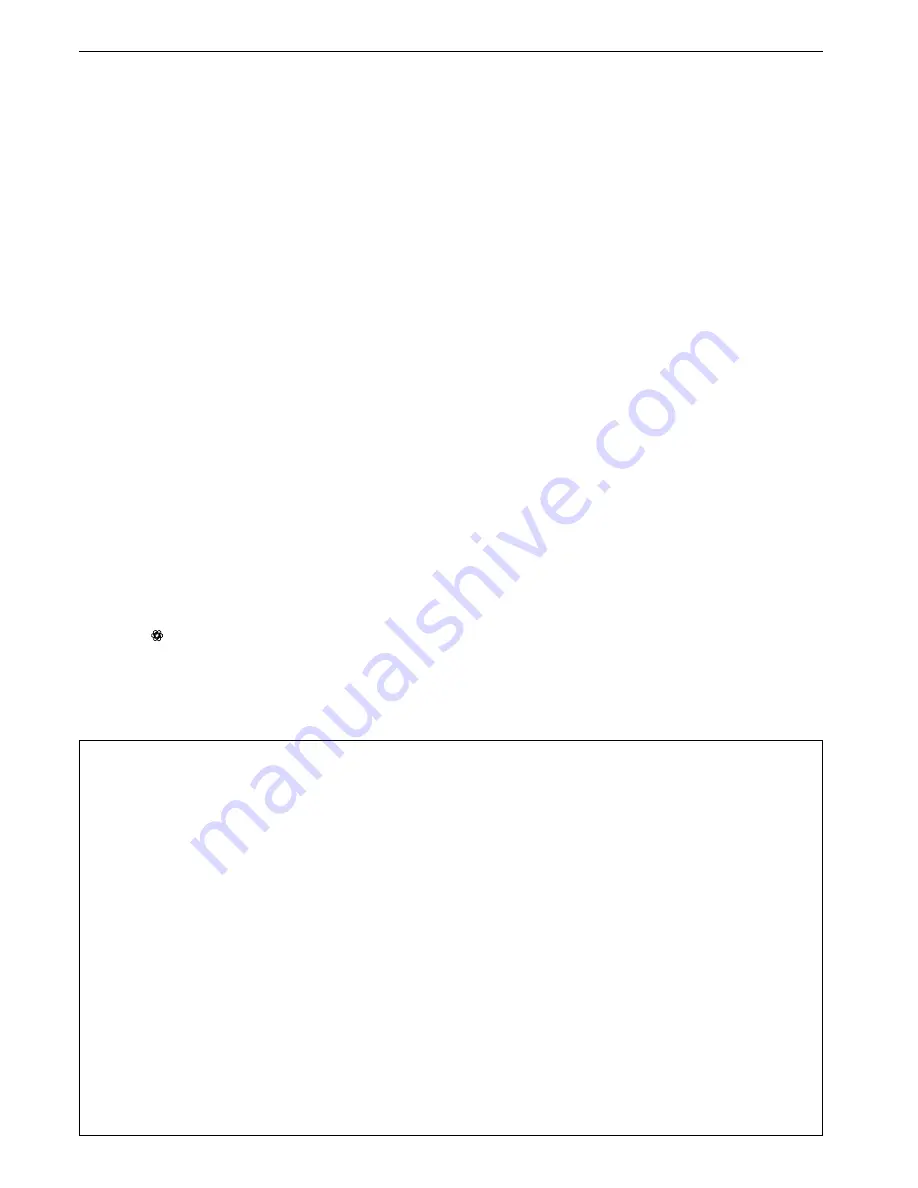
8
Concord CXD -
Installation
4
SEALED (PRESSURISED) SYSTEMS
Working pressure 4.5 bar maximum.
Particular reference should be made to BS. 6644: Section 2;
Subsection 11 and Guidance note PM5 "Automatically controlled
steam and hot water boilers" published by the Health and Safety
Executive.
The information and guidance given below is not intended to
override any requirements of either of the above publications or
the requirements of the Local Authority, gas or water undertakings.
In general commercial closed pressurised systems are provided
with either manual or automatic water make up.
On both instances it will be necessary to fit automatic controls
intended to protect the boiler, circulating system and ancillary
equipment by shutting down the boiler plant if a potentially
hazardous situation should arise.
Examples of such situations are low water level and operating
pressure or excessive pressure within the system. Depending
on circumstances controls will need to be either manual or
automatic reset. In the event of shut down both visual and audible
GENERAL
alarms may be necessary.
Pressure vessels used must comply with BS. 4814 and must be
sized on the basis of the total system volume and initial charge
pressure.
Initial minimum charge pressure should not be less than 0.5 bar
(7.2 psi) and must take account of static head and specification
of the pressurising equipment. The maximum water temperatures
permissible at the point of minimum pressure in the system is
specified in Guidance Note PM5.
When make up water is not provided automatically it will be
necessary to fit controls which shut down the plant in the event
of the maximum system pressure approaching to within 0.35
bar (5 psi) if safety valve setting.
Other British Standards applicable to commercial sealed
systems are:-
BS. 6880: Part 2.
BS. 1212
BS. 6281: Part 1
BS. 6282: Part 1
BS. 6283: Part 4
relevant requirements of the local gas supplier, local authority
and the relevant British Standard Codes of practice and building
regulations.
These appliances are NOT suitable for installation where they will
be exposed to the elements. A boiler room shall be constructed or
adapted to meet the requirements of BS 6644.
The maximum ambient temperature is 32
0
C at 1.5 metres from
the floor with a maximum humidity of 90% RH.
FOR SMALL PIPE INSTALLATIONS;
BS. 6891;
Installation of low pressure pipework
FOR LARGE PIPE INSTALLATIONS:
British Gas Publications:
IGE-UP-1: Purging Procedures of Non-domestic Gas
Installations. Soundness Testing Procedures for
Industrial and Commercial .
IM11:
Flues for Commercial and Industrial Gas Fired Boilers
and Air Heaters.
Gas Installations
IGE-UP-2: Guidance notes on the Installation of Gas Pipework,
Boosters and Compressors in Customer’s Premises
Equal to or Greater than 25mm (Non-domestic).
BS.6644:
Installation of Gas Fired Hot Water Boilers 60kW to
2MW.
CP341:
Water Supply.
CP342:2:
Centralised Hot Water Supply.
Model Water Byelaws.
Manufacturers notes must not be taken, in any way, as overriding
statutory obligations.
The appliance must be installed in a room separated from living
rooms and provided with appropriate ventilation direct to the outside
- see Table 6.
atmosphere if proper venting and expansion of system water is to
be achieved. The same tank is used to fill the system with water
and it is through the cold feed pipe that system water expands
into the tank when the boiler passes heat into the system.
Conversely, when the system cools, water previously expelled is
drawn back from the tank into the system together with a quantity
of dissolved oxygen.
Even if leakage from the heating and hot water system is eliminated
there will be evaporation losses from the surface of the tank which,
depending upon ambient temperature, may be high enough to
evaporate a large portion of the system water capacity over a full
heating season.
There will always be corrosion within a heating or hot water system
to a greater or lesser degree, irrespective of water characteristics,
unless the initial fill water from the mains is treated. Even the
water in closed systems will promote corrosion unless treated. For
the reason stated,
Caradon Plumbing Limited
strongly
recommend that when necessary the system is thoroughly cleaned,
prior to the use of stable inhibitor, which does not require continual
topping up to combat the effects of hardness salts and corrosion
on the heat exchangers of the boiler and associated systems.
Caradon Plumbing Limited
advise contact directly with specialists
on water treatment such as:
Fernox Manufacturing Co. Ltd., or
Sentinel Division,
Tandem House, Marlowe Way,
Betz Dearborn Ltd.,
Croydon, Surrey CRO 4XS
Widnes,
Cheshire, WA8 8UD
Tel 0870 5601 5000
Tel. 0151 424 5351
INSTALLATION REQUIREMENTS
The appliance must be installed by a CORGI registered installer
identified by .
The installation of the boiler must be in accordance with the
relevant requirements of the Gas Safety Regulations, current
I.E.E. (BS. 7671) Regulations, Model Water Bye-laws, local
water authority bye-laws and it should also comply with any
Summary of Contents for Concord CXD 40-100
Page 1: ......