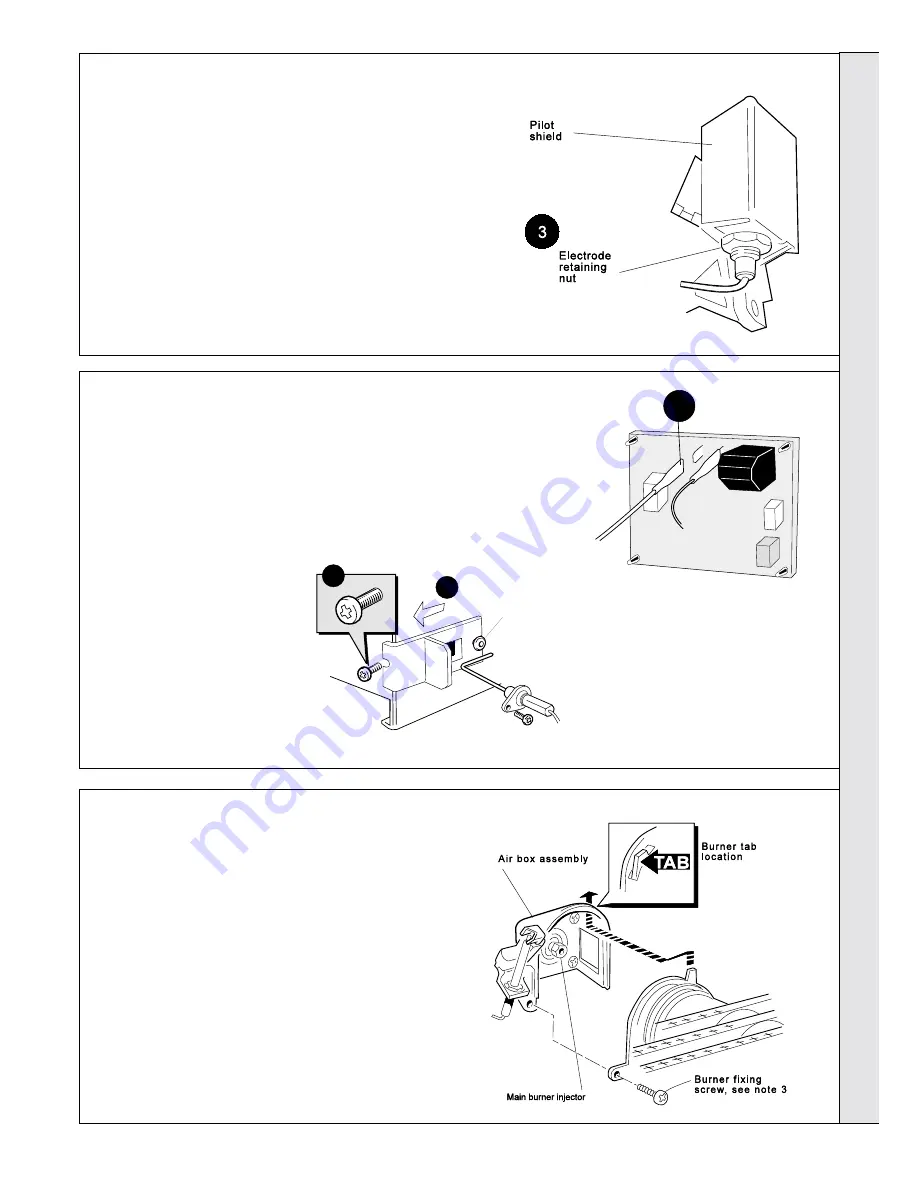
25
Classic RS -
Installation & Servicing
SERVICING
42 DETECTION ELECTRODE REPLACEMENT
1. Refer to Frame 36.
2. Remove the burner and air box assembly. Refer to Frame 43.
3. Remove the electrode retaining nut.
4. Remove the pilot shield.
5. Remove the ignition electrode and integral lead.
6. Refit the new electrode and lead in reverse order.
Ensure that the pilot shield is replaced.
7. Check the spark gap. Refer to Frame 40.
8. Refit the burner.
9. Check the pilot ignition.
41 IGNITION ELECTRODE AND LEAD REPLACEMENT
1. Refer to Frame 36.
2. Remove the screw retaining the front burner support strap
to the combustion chamber.
3. Remove the M5 pozi screw, situated at the LH bottom rear
of the burner. Pull the burner downward to disengage the
retention tab and remove the burner.
4. At this stage the main burner injector can be removed,
checked, cleaned or replaced as required. Ensure that an
approved jointing compound is used sparingly.
5. Fit the new burner, ensuring that the retention tab is
correctly located in the air box slot.
6. Refit the M5 retaining screw.
7. Refit the boiler casing.
9. Check the burner for cross-lighting and flame stability.
43 MAIN BURNER AND MAIN BURNER INJECTOR REPLACEMENT
3
4
Retaining
clip
Cla 2121
2
Clas 2122
1. Refer to Frame 36.
2. Pull the electrode and lead from the PCB connection.
3. Remove the bracket retaining screw.
4. Pull the bracket forward to disengage the rear retaining
clip.
5. Remove the bracket.
6. Remove the screw retaining
the detection electrode.
7. Fit new detection electrode
and reassemble in reverse
order.
SER
VICING