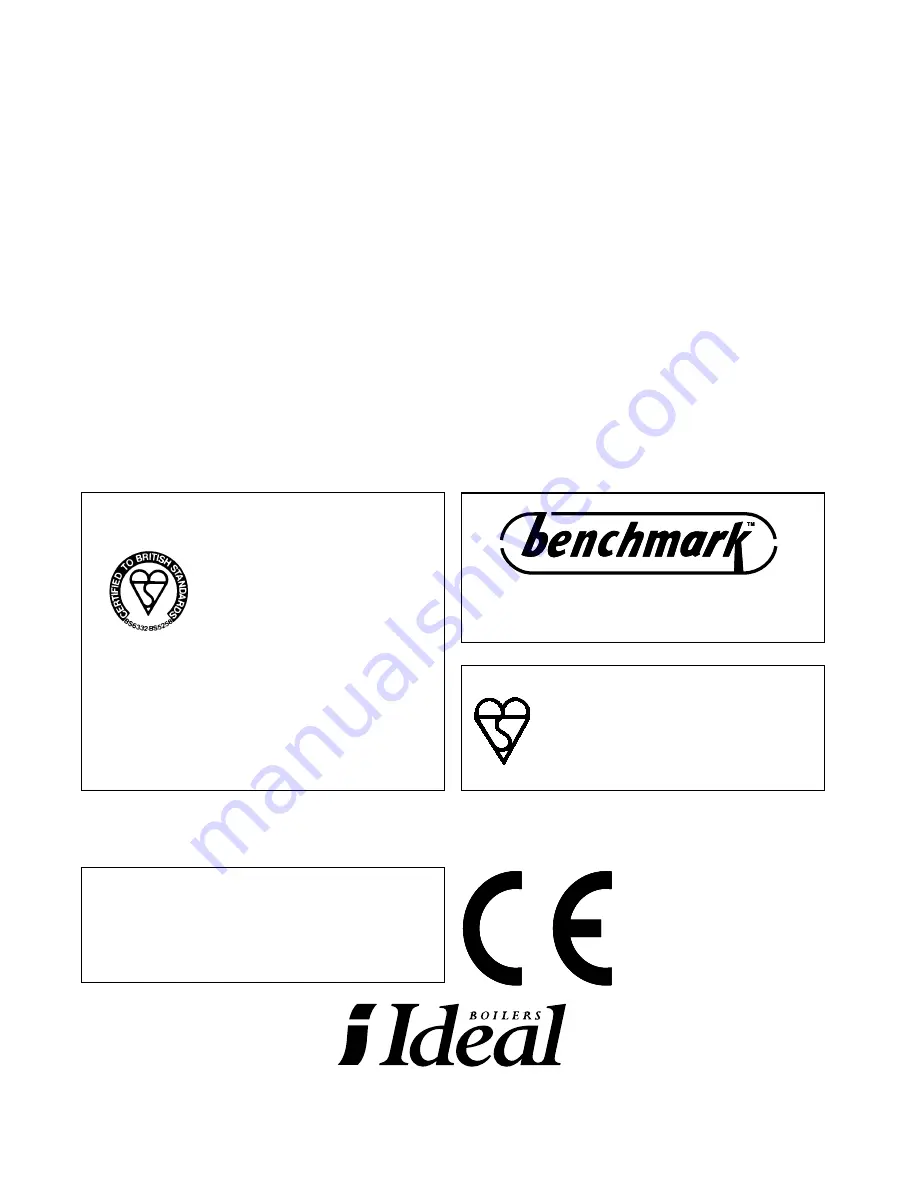
42
Mexico Super CF 3/60P - 3/140P -
Installation
Ideal Installer/Technical Helpline: 01482 498663
Caradon Plumbing Limited
, P.O. Box 103, National Ave, Kingston upon Hull, HU5 4JN. Telephone: 01482 492 251
Fax: 01482 448 858. Registration No. London 322 137. Registered Office: National Avenue, Kingston upon Hull,
HU5 4JN.
A subsidiary of Caradon p.l.c
Technical Training
Caradon Plumbing Limited
pursues a policy of continuing
improvement in the design and
performance of its products. The right
is therefore reserved to vary
specification without notice.
September 1999
151 912 A02
The Caradon Plumbing Limited Technical Training Centre
offers a series of first class training courses for domestic,
commercial and industrial heating installers, engineers and
system specifiers.
For details of courses please ring: ...........
01270 413 624
These appliances are designed for use with Natural
Gas only. They have been tested and conform with
the provisions of BS. 6332 and BS. 5258.
THIS SYMBOL IS YOUR
ASSURANCE OF QUALITY
CERTIFIED PRODUCT
Manufactured under a BS EN ISO 9001: 1994
Quality System accepted by BSI
The code of practice for the installation,
commissioning & servicing of central heating systems
Summary of Contents for 4134899
Page 1: ......