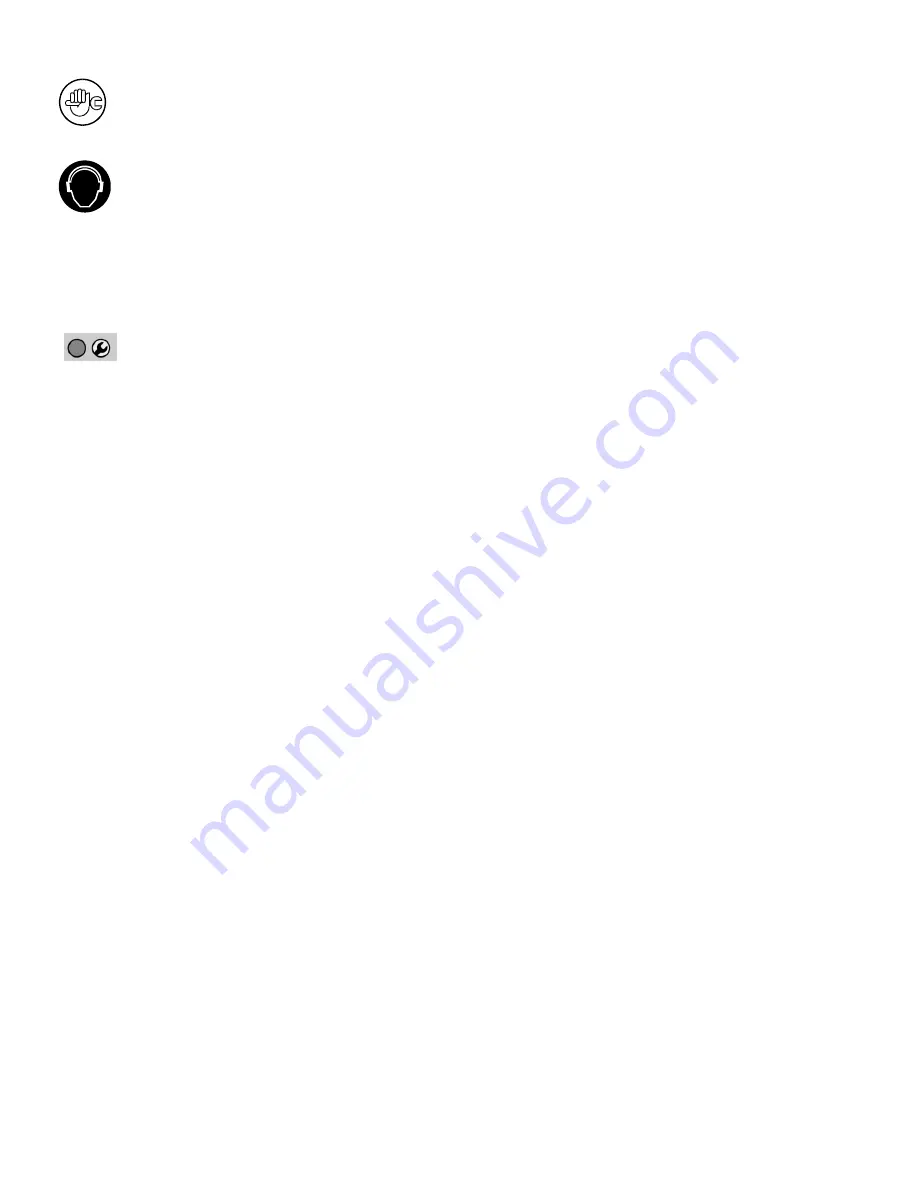
iDRY Series Heatless Regenerated Dryers: IOM10003-C
(Rev. A)
22
9.
TROUBLESHOOTING GUIDE
The troubleshooting and the eventual checks must be performed by qualified personnel only.
The technician that services the machine must wear hearing and eye protection while servicing the dryer.
Each employee must select a proper personal protection device (PPD) hearing protector such as earmuffs,
ear canal caps or earplugs in order to prevent permanent hearing damage or loss.
SYSTEM TROUBLE
POSSIBLE CAUSE
SUGGESTED ACTION
The service LED
on the
controller is
flashing amber or
red.
Service Reminder
Service Due
If the service LED indicator light is flashing amber this is an
indication that the dryer is approaching the annual
maintenance interval, and schedule maintenance should be
performed within the next 5-days. – 360 hours
If the service LED indicator light is flashing red then the dryer
is overdue for scheduled maintenance by approximately one
month, and should be serviced immediately to ensure
trouble free operation. – 400 hours
Dryer stopped
No power
Valve problem
No pilot control air
Solenoid valves
Controller
Compressor off
Check power and electric
Check the operation of inlet and purge exhaust valves
Ensure Control pilot air is delivering at 80 psi
Ensure DIN connectors are properly attached to solenoid
valves
See controller troubleshooting
Check if compressor Sync is commanding dryer off
All the inlet air is
discharged
through the
silencers
Faulty inlet valve
Faulty signal
Faulty Outlet valve
Pneumatic
The inlet valves are blocked – open and clean
The controller continuously supplies solenoid valve PVA
and/or PVB – check the electric wiring and if necessary
replace
Outlet Check valve(s) stuck open – serviceable only by
qualified technician
Ensure tube routing matches diagram
Liquid comes out
of the silencers
High dew point
Overloaded
Ensure operation sequence and purge setting
Check capacity versus operating conditions
Depressurization
No power
Flow control valve
No pilot control air
Exhaust Silencers
Check purge exhaust valve for normal operation
Ensure that the purge exhaust valve actuators is not closed
Ensure pilot air reading is 80 psi
Replace silencer filter elements if clogged
Repressurization
Purge Exhaust Valve
Purge line
Purge Valve
Inlet Valve
See purge Exhaust Valve troubleshooting
Purge setting or clog, full open purge valve to clean out and
then set according to table xx
See Purge valve troubleshooting
See Inlet Valve Failure troubleshooting