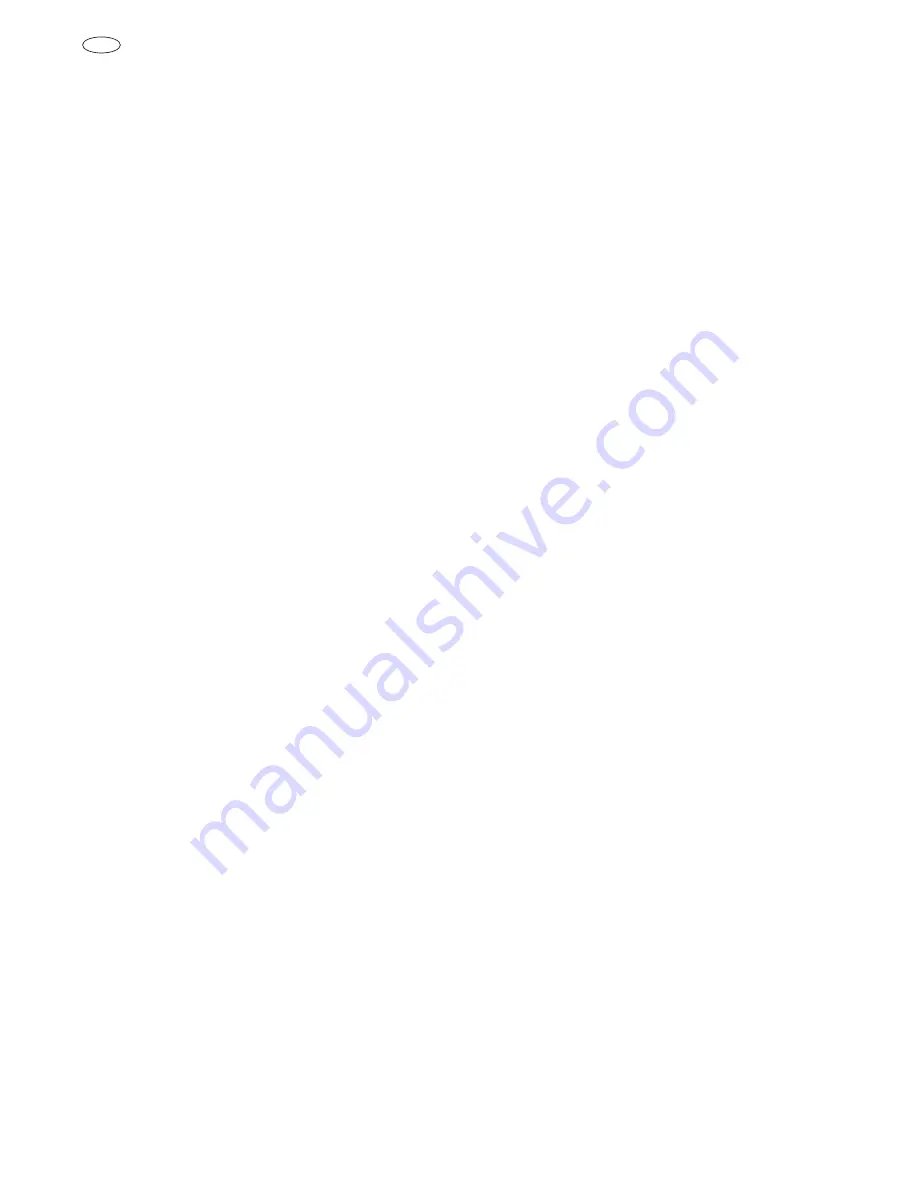
GB
10
PERIODICAL
MAINTENANCE AND CLEANING
N.B.: Cleaning and maintenance especially will vary,
depending upon ambient and use conditions.
In particular affect: hard water, ice volume produced and
location requirements.
The following maintenance procedures should be sched-
uled once per year al least from the local service Agency.
Be sure the electrical power supply of the machine is
OFF, before starting any maintenance and cleaning
procedure.
a) Close the water supply, shut-off valve, disconect the
water inlet pipe and remove the strainer from its seat in
the water inlet elettrovalve withdrawing it bay means of
pilers. Clean the strainer under running water and
reassemble.
b) Check that the ice maker cabinet is levelled in side-to-
side and front-to-rear directions.
c) Check paddle shaft motor and harvest motor opera-
tion.
d) If you think it opportune, check by means of a gauges
the delivery pressure and the evaporator temperature.
e) Clean the air-cooled condenser using a nonmetal
brush or a vacuum cleaner.
f) Check that fan blades move freely and are not touch-
ing any sourfaces.
g) Check for refrigerant leaks.
h) Check for water leaks. Pour water down bin drain to be
sure that drain line is open and clear.
i) Check operation of the bin thermostat.
ICEMAKER CLEANING
a) Remove the top panel.
b) Remove all ice from the storage bin.
c) Close the water supply shut-off valve.
d) Fill tilting pan with a solution of water and citric acid
(200-400 grs. of citric acid in one litre of water) and by
means of a brush clean the inside of the tilting pan and
the evaporator fingers. Start the icemaker to tilt the
pan, rinse with clean water in abudance and repeat
cleaning three times.
e) Add hot water to the ice storage bin and thoroughly
wash and rinse all surfaces within the bin.
f) Clean and sanitize the ice storage bin frequently.
PARTS REPLACEMENT PROCEDURES
A) ADJUSTABLE LEGS FOR N55S÷N90L MODELS
Using the couplings and adjustable feet supplied and
screwing them on the base nipples the icemaker can be
placed at 9,5 cm. abt. from ground level.
Extended feet are available on request to adjust the ice-
maker at 16 cm. about from ground level. A kit of exten-
sion feet can be supplied on request also for the N35S
model.
The adjustment should be performed during initial instal-
lation of the cabinet and any time the cabinet is moved
from the original location to another site.
N.B.: (WARNING) Be sure the electrical power supply
and the water supply are OFF, before starting any
removal and replacement procedures, as a precaution
to prevent possible personal injury or damage to
equipment.
B) COMPRESSOR REPLACEMENT
a) Remove the rear panel on the N25S-N25L model and
the rear panel grid on N35S model
On N45S÷N140 models remove the rear panel grid
and the side panels.
Remove the cover and disconnect the electrical leads
from the compressor junction box.
Bleed off or blow the refrigerant charge through the
valve.
Unsolder and disconnect both the suction line and the
discharge line (from the compressor).
Remove compressor mounting bolts and the compres-
sor from the unit base.
Always install a replacement drier, anytime the sealed
refrigeration system is open. Do not replace the drier
until all other repairs or replacements have been com-
pleted.
To install the replacement compressor follow previous
steps in reverse.
Thoroughly evacuate the system to remove moisture
MAINTENANCE
Summary of Contents for N25S
Page 2: ......
Page 16: ...GB 14 WIRING DIAGRAMS N25S AIR...
Page 17: ...GB 15 N25L N35S AIR...
Page 18: ...GB 16 N25S N25L N35S WATER...
Page 19: ...GB 17 N45S N45L N55S N55L N70S N90S N90L AIR...
Page 20: ...GB 18 N45S N45L N55S N55L AIR...
Page 21: ...GB 19 N50 B I AIR...
Page 22: ...GB 20 N50 B I WATER...
Page 23: ...GB 21 N70S N90S N90L WATER...