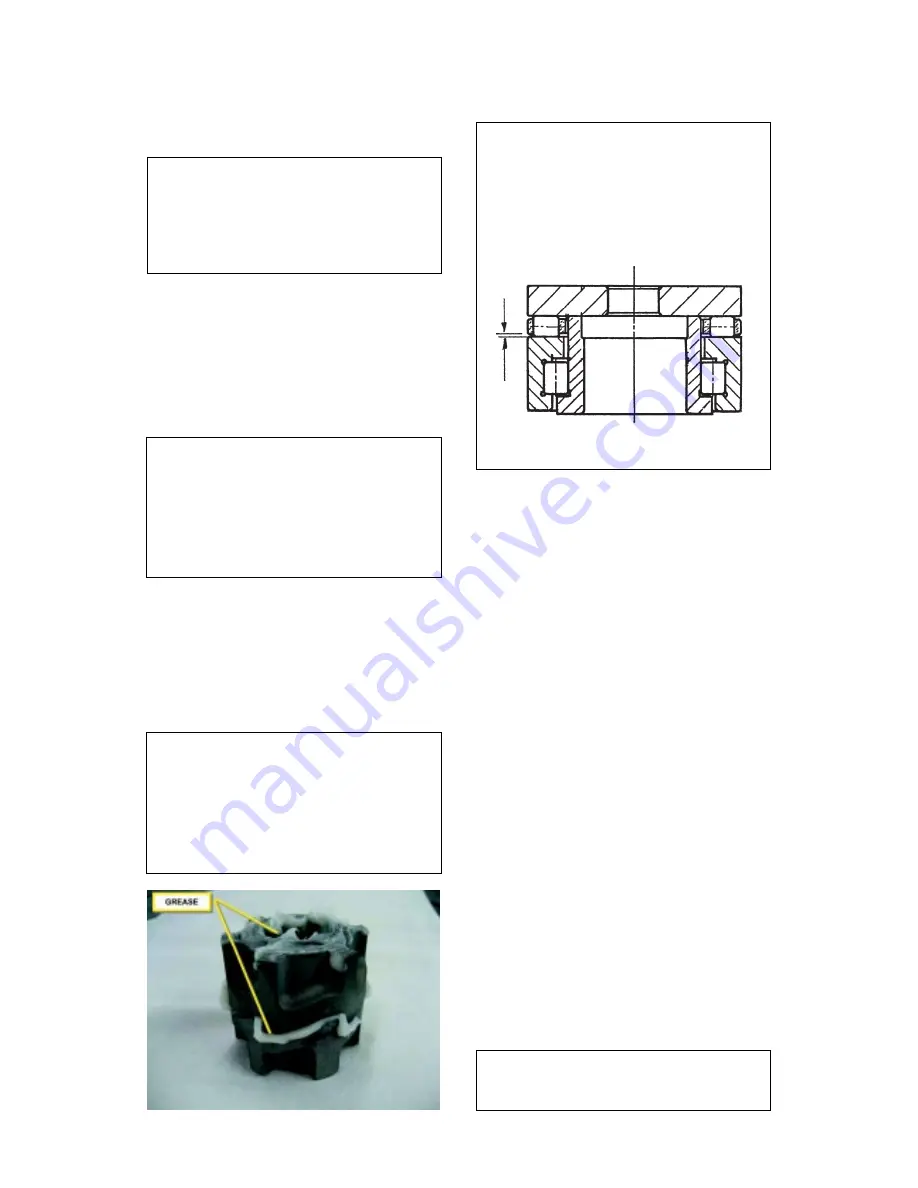
Page 23
Page 23
NOTE. Install the upper bearing into the ice
breaker starting by the radial portion that
must be fitted with the flat surface facing up.
Apply some lubricant (grease) on the upper
surface then install the rollers cage with the
smaller openings of the same facing up so to
leave a small gap between plastic cage and
flat surface of the botton portion of the bearing
(see drawing).
Apply some move lubricant then place the
S.S. trust washer.
J.
REPLACEMENT OF THE GEAR MOTOR
ASSY
1.
Remove the rear side and top panels.
2.
Remove the three bolts and washers
securing the gear reducer base to the unit chassis,
then remove bolts and lockwashers which attach
the bottom of the aluminium adaptor to the gear
reducer case cover.
3.
Disconnect the electrical leads from the
electromagnetic safety device located on top of
drive motor.
4.
Trace and disconnect the electric wires leads
of the drive motor. Lift and remove the entire
gear motor assembly.
5.
To install the replacement gear motor assy
follow the above steps in reverse.
K.
REPLACEMENT OF FAN MOTOR
1.
Remove front and side panels.
2.
Remove screws and yellow green ground
wire. Trace the electrical leads of fan motor and
disconnect them.
3.
Remove the bolts securing the fan motor
bracket to the cabinet base and then remove the
assembly.
4.
To install the replacement fan motor follow
the above steps in reverse.
NOTE. When installing a new fan motor
check that the fan blades do not touch any
surface and move freely.
8.
Slide off from the auger bottom the upper
half of the water seal.
NOTE. Any time the auger is removed for
replacement or inspection use extra care in
handling the water seal parts, so no dirt or
foreign matters are deposited on the surfaces
of the seal. If there is any doubt about the
effectiveness of the water seal or O ring do
not hesitate to REPLACE THEM.
9.
Unloose and remove the three bolts and
lockwashers which attach the freezer assy to the
aluminium adaptor.
10. Raise the freezer assy off the adaptor, secure
it out of the way to allow room to work. Using a
suitable lenght and size wooden dowel or stick
inserted through the top of the open freezer, tap
the lower half of the water seal and the lower
bearing out the bottom of the freezer.
NOTE. It is good practice to replace the
water seal assy and both the top and the
bottom bearings any time the auger is
removed.
To facilitate this, SCOTSMAN EUROPE
Service makes available a service Kit
P/N 001028.07 which includes besides the
above mentioned parts, the ice breaker O ring
and a can of food grade waterproof grease.
11. Reach through the adaptor and remove the
coupling parts.
12. Check both the coupling halves for chipping
and wear and do not hesitate to replace them.
13. To install the ratched coupling, the water
seal, the bearings and auger follow previous
steps in reverse.
NOTE. It is very important to provide correct/
proper lubrication of the inside bore of the
upper semi-coupling as well as to the external
surfaces of the teeth as shown on the here
below photo.
The correct lubrication allows the upper semi-
coupling to move it down, by the load of the
upper spring, in case of any rising up during
its rotation.