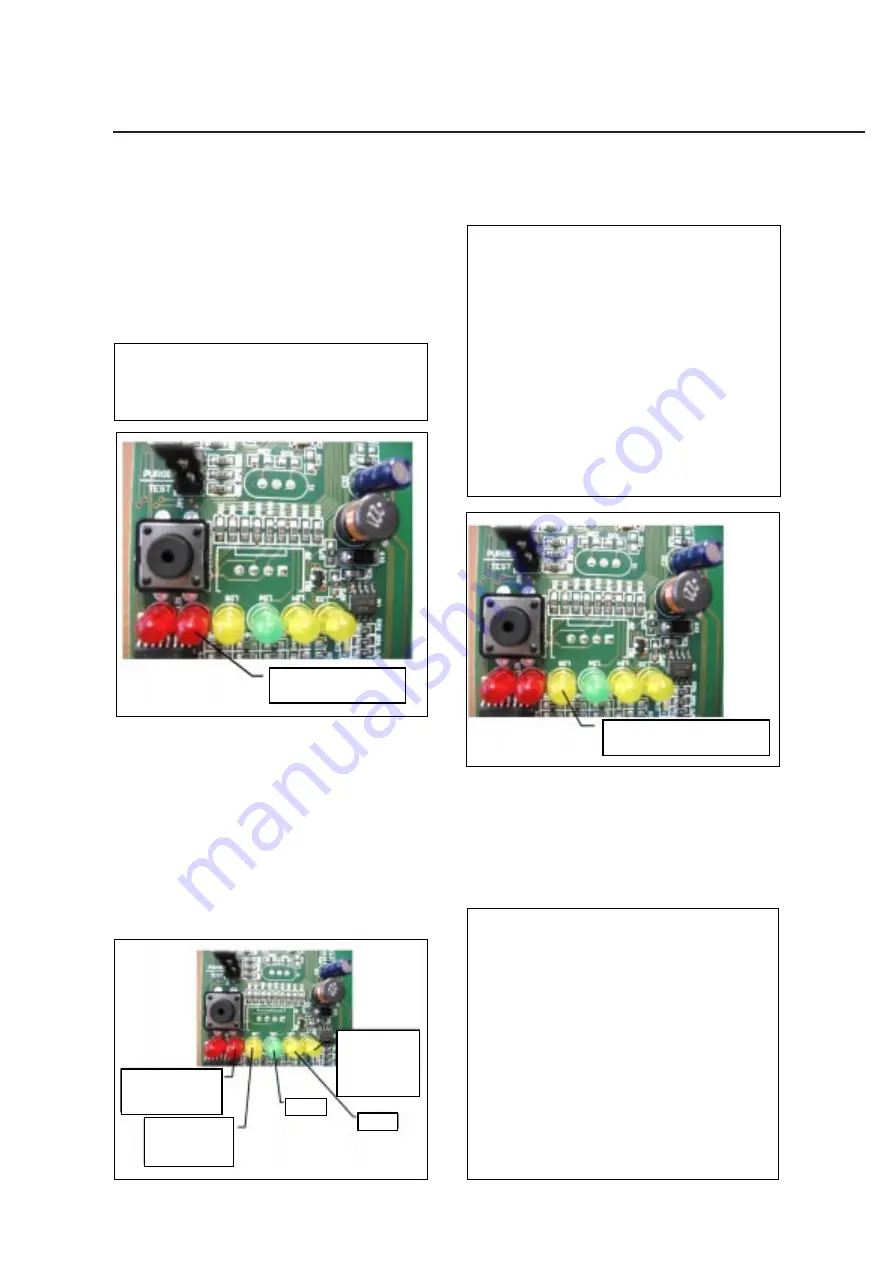
OPERATING INSTRUCTIONS
START UP
After having correctly installed the ice maker and
completed the plumbing and electrical connec-
tions, perform the following “Start-up” procedure.
A.
Open the water supply line shutoff valve and
give power by moving the main switch, on the
power supply line, to the ON position.
The GREEN LED will glow to signal that unit is
under power.
NOTE. Every time the unit is put under power,
after being kept for sometime in shut-off
conditions (electrically disconnected) the 2nd
RED LED will blink for 3 minutes (Fig.1).
B.
Elapsed the 3 minutes - stand by period - the
unit starts operating with the activation in
sequence of the following assemblies:
GEAR MOTOR
COMPRESSOR
FAN MOTOR kept under control by the
condenser temperature sensor which has its
probe within the condenser fins
with the switching off of the 2nd RED LED
(Fig. 2).
C.
2 or 3 minutes after the compressor start up,
observe that flaker ice begins dropping off the ice
spout to fall into the storage bin.
NOTE. If, after ten minutes from the
compressor start-up, the evaporating tem-
perature has not dropped down to a value
lower than -1
°
C (30
°
F) the evaporating tem-
perature sensor detects such an abnormal
situation and stops consequently the unit
operation.
In this circustance, the 3rd warning YELLOW
LED will blink (Fig.3).
After having diagnosed and eliminated the
cause of the poor evaporating temperature
(insufficient refrigerant in the system or
inoperative compressor or evaporator sensor)
it is
necessary to push the RE-SET BUTTON
or De-
engerize and re-engerize unit
.
The unit, before
resuming the total operation,
will go through the
usual 3 minutes STAND-BY period.
OPERATION CHECKS UPON THE UNIT
START UP
D.
Remove service panels and if necessary
install the refrigerant service gauges on the
corresponding Service valves to check both the
HI and LO refrigerant pressures.
NOTE. The condenser temperature sensor,
which is located within the condenser fins,
keeps the head (condensing) pressure
between two preset valves.
In case of condenser clogging such to prevent
the proper flow of the cooling air or, in case
the fan motor is out of operation, the
condenser temperature rises and when it
reaches 70
°
C (160
°
F) the condenser tempe-
rature sensor shuts-off the ice maker with the
consequent light-up of the 2nd RED
WARNING LIGHT (Fig.4).
After having diagnosed the reason of the
temperature rise and removed its cause, it is
necessary to proceed as per the previous
“NOTE” to start up again the operation of the
ice maker.
FIG. 1
BLINKING - FLASHING
3 MINUTES DELAY TIME AT START UP
BLINKING-FLASHING SLOW
INFRARED BEAM CUTTED
WITH MACHINE IN OPERATION
STEADY
MACHINE OFF AT BIN FULL
BLINKING-FLASHING FAST
INFRARED BEAM ON AFTER
THE TRIPPING OFF AT BIN FULL
NO WATER
POWER ON
BLINKING-FLASHING
3 MINUTES DELAY TIME AT START UP
STEADY
TOO HI CONDENSING TEMPERATURE
BLINKING-FLASHING
TOO HI EVAPORATING TEMP.
AFTER 10 MIN. FROM START UP
STEADY
WRONG-NO-SLOW ROTATION
GEAR MOTOR
FIG. 2
FIG. 3
BLINKING - FLASHING
TOO HI EVAPORATING TEMP. AFTER 10 MIN.
FROM START UP
GEMD270A
Page
8