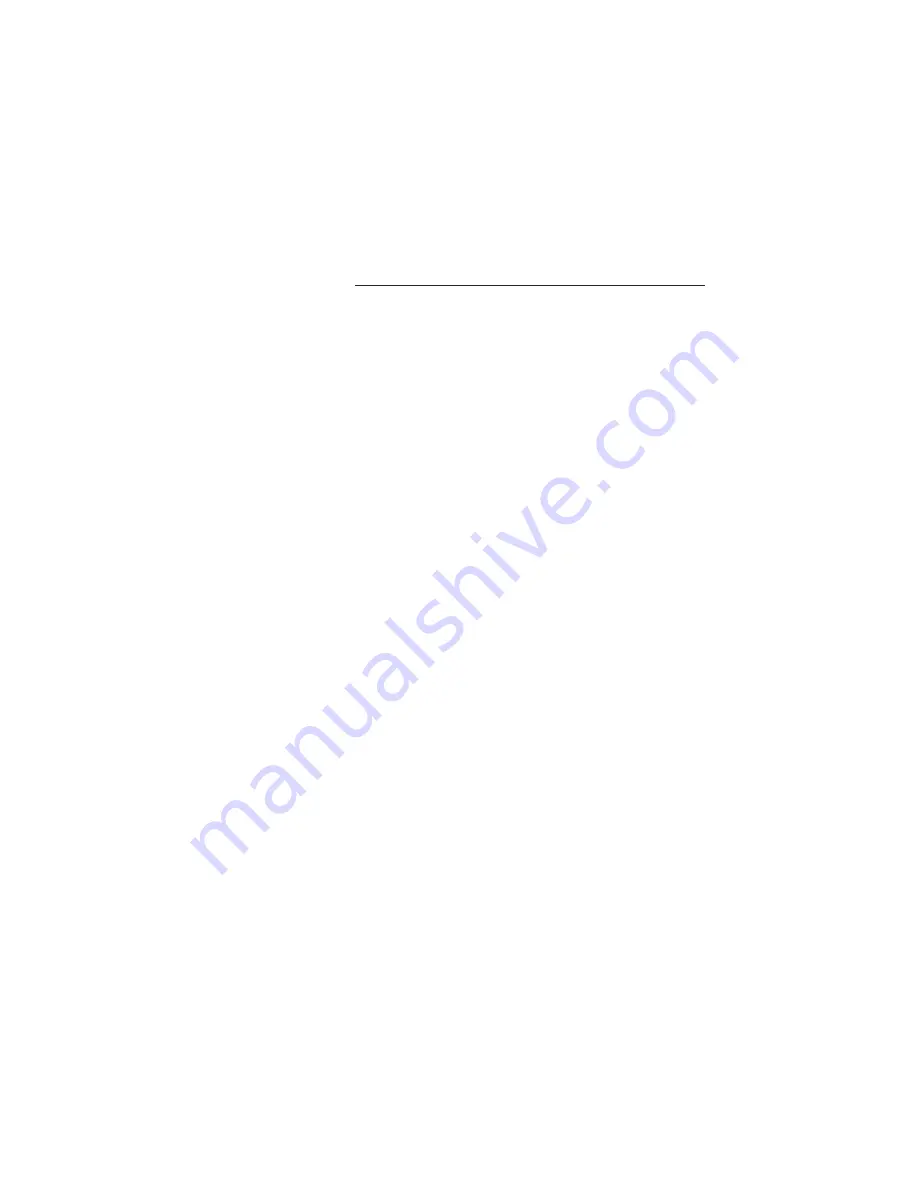
88
Troubleshooting
Advise the user to move the printer to cooler, cleaner location.
2.
Check the kinds of print jobs the user is running: look for very dense graphics
and layouts.
Advise the user to run jobs in smaller batches.
3.
Power off the printer. Remove the paper guide assembly or pedestal top cover.
Check that the power supply guard/air deflector is correctly positioned over the
power supply board. CAUTION: DO NOT TOUCH THE POWER SUPPLY, but
hold your hand close enough to check for heat radiating off the power supply
board.
If the power supply is noticeably hot, replace it.
4.
Check that all fan cables are connected.
Connect all fan cables.
5.
Inspect vents and fan airways for obstructions. Look underneath cabinet models
for items blocking the cabinet exhaust vents.
Remove any obstructions from vents and airways.
6.
Install paper guide assembly or pedestal top cover. Power on the printer. Load
paper. Run the “All E’s” print test for 5–10 minutes.
If the message appears, replace the CMX controller board. Record the
message and return it with the defective board.
081 POWER SUPPLY VOLTAGE FAILURE
1.
The power supply has failed.
Replace the power supply board.
2.
Power on the printer.
If the message appears, replace the CMX controller board.
082 POWER SUPPLY 8.5V FAILED
1.
8.5 Volt Power Failed. Internal power failure.
Cycle power. If the message appears, replace the power supply board.
2.
Power on the printer.
If the message appears, replace the CMX controller board. Record the
message and return it with the defective board.
3.
Power on the printer.
Summary of Contents for 6400 Series
Page 2: ......
Page 3: ...S246 0117 06...
Page 28: ...28 Installation...
Page 34: ...34 Preventive Maintenance...
Page 54: ...54 Principles of Operation...
Page 190: ...190 Adjustment Procedures...
Page 292: ...292 Replacement Procedures and Illustrated Parts List...
Page 305: ...305 Wire Data Cable Routing Cabinet Model...
Page 307: ...307 Wire Data Cable Routing Pedestal Model...
Page 311: ...311 Wire Data Cable Assembly Card Cage Fan Description Part No 14H5285 PIN 1 PIN 1...
Page 313: ...313 Wire Data Cable Assembly Exhaust Fan Description Part No 14H5286...
Page 314: ...Wire Data 314 Cable Assembly Hammer Bank Logic Description Part No 14H5279...
Page 315: ...315 Wire Data Cable Assembly Hammer Bank Power Description Part No 14H5283 PIN 1 PIN 1...
Page 317: ...317 Wire Data Cable Assembly MPU Description Part No 14H5329 PIN 1 PIN 3 PIN 2 PIN 1...
Page 319: ...319 Wire Data Cable Assembly Ribbon Motor Extension Description Part No 63H7464...
Page 320: ...Wire Data 320 Cable Assembly Shuttle Motor Drive Description Part No 14H5330...
Page 322: ...Wire Data 322 Cable Assembly Centronics DataProducts Adapter Description Part No 14H5522...
Page 323: ...323 Wire Data Cable Assembly 5V Remote Power Description Part No 14H5589...
Page 325: ...325 Wire Data Cable Logic Power Stacker Description Part No 24H8976...
Page 326: ...Wire Data 326 Cable Power Power Stacker Description Part No 24H8975...
Page 327: ...327 Wire Data Cable Vertical Rail Power Stacker Description Part No 24H8964...
Page 328: ...Wire Data 328 Fan Assembly Hammer Bank Description Part No 14H5159 P107 HBF P107 HBF...
Page 329: ...329 Wire Data Magnetic Pickup Assembly Description Part No 57G1476...
Page 330: ...Wire Data 330 Switch Assembly Cover Open Description Part No 14H5282...
Page 332: ...Wire Data 332 Switch Assembly Platen Interlock Description Part No 14H5280 P107 PLO...
Page 344: ...344 Printer Specifications...
Page 348: ...348 Torque Table...
Page 356: ...356 Safety Inspection Guide...
Page 364: ...364 Abbreviations and Signal Mnemonics...
Page 404: ...404 Power Stacker 75 80 85 90 85 80 Figure 84 Stacker Detail Rollers...
Page 412: ...412 Power Stacker...
Page 427: ......
Page 428: ...Copyright IBM Corp 1995 1998 S246 0117 06 07S246011706 b7 24H8887 0724H8887 b7 163983 001A...