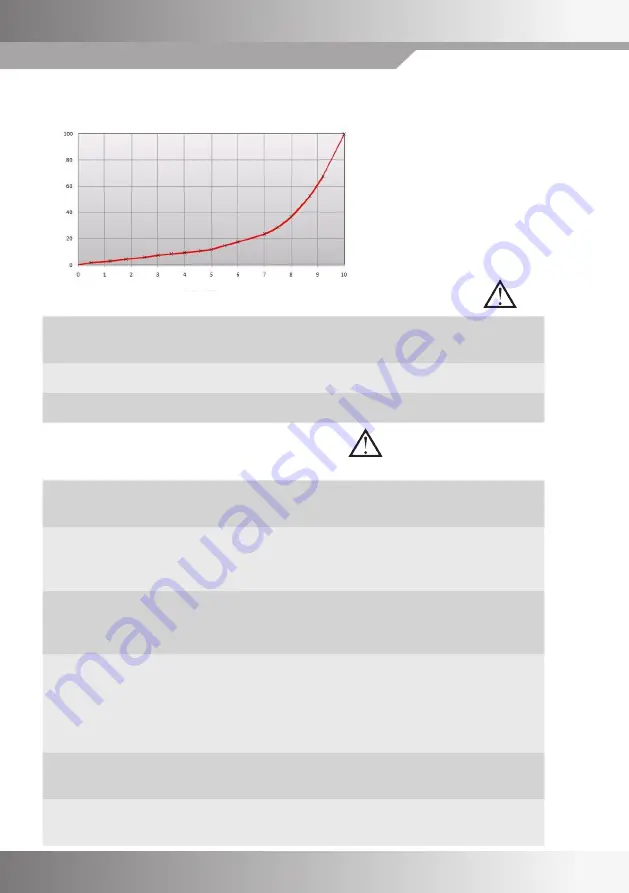
10
Check that
the control unit is connected as per instructions on page 9.
Power supply 230-240 V +/-15%, 50/60 Hz.
Check that
the input signal is 0-10 V.
Check that
the rotation monitor and blow-clean function are connected.
INPUT SIGNAL/ROTATION SPEED
The input signal is directly
proportional to the efficacy of the
rotor, which implies that input signal
and rotation speed are as per the
adjacent diagram.
CHECKS BEFORE POWERING UP THE CONTROL UNIT
Check that
the motor rotates in the right direction in relation to the rotor's direction
of rotation. In the event of a fault, switch two phases to the motor.
Adjustment of max.
speed
Set the High Speed DIP switch to the ON position.
Adjust "Max rpm" so that the rotor rotates at 10-12 rpm
(or as per rotor manufacturer's directions).
Checking minimum
speed
Set the Low Speed DIP switch to ON.
Check that the rotor starts.
The minimum speed is preset.
Checking the blow-clean
function
Switch off the voltage.
Make sure the blow-clean DIP switch is set to ON and the input signal is
disconnected.
After switching on the voltage the rotor rotates for 20 seconds at 12 rpm
on the motor.
Checking the rotation
monitor
The yellow Rotation LED will flash when the magnet passes the magnetic
sensor, regardless of DIP switch position.
Finish by
having the control unit drive the rotor at maximum and minimum
rotation speeds and checking that the operating rotor speed is correct.
COMMISSIONING THE EQUIPMENT
Should be accomplished in sequence
11
Input signal - rotation speed
Rotation speed (%)
Input signal 0-10 V