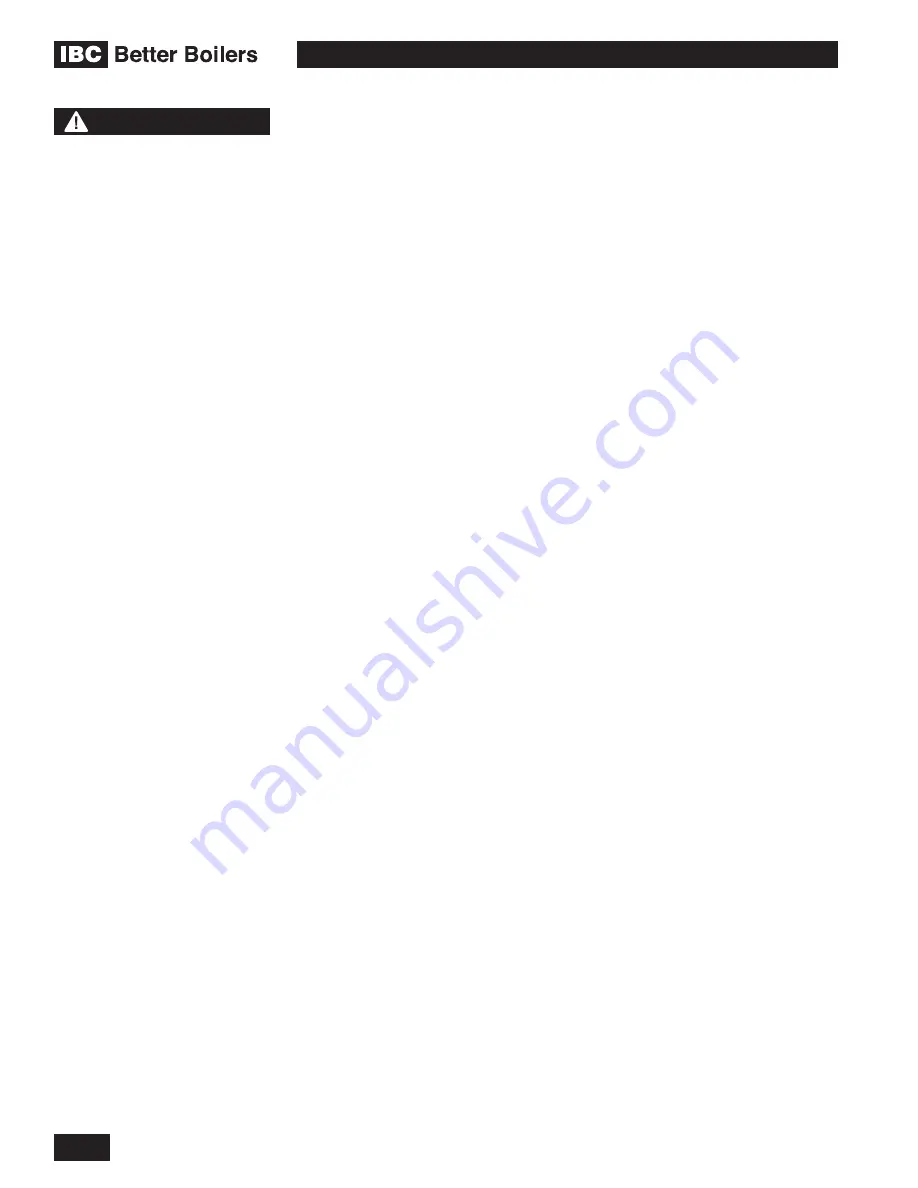
INSTALLATION AND OPERATION INSTRUCTIONS
4-2
VFC 15-150, VFC 45-225 MODULATING GAS BOILERS
4.1.6 Heat Exchanger
During burner inspection (with the burner removed), examine the heat exchanger
tubes adjacent to the burner’s normal position. In areas of poor gas quality, there
may be a buildup of black plaque (typically sulfur). Other fouling agents: airborne
dust, debris and volatiles.
Refer to burner removal instructions in Section 4.3
for access to combustion
chamber and heat exchanger.
Note that the safety warning regarding burner
refractory on this page must be observed.
4.1.7 Pump
Check that the pump is on in normal operation and that the water Δ°T is
reasonable for a given firing rate (e.g. 10°F between supply and return when
firing at 75,000 Btu/hr. for a VFC 15-150 unit).
4.1.8 Gas Piping
Check for damage or leaks and repair as needed.
4.1.9 Control Module
•
Check that boiler operation is consistent with the steps in the
Touch Screen
Boiler Controller Manual.
•
Check that water temperature targets and setpoint is satisfactory and have
not been adversely amended.
•
Check the operating history using the boilers Logs menu and Error Logs
menu. The controller tracks the duty cycle of the boiler in each of the 4 loads
separately. This information can be used to adjust the water temperatures of
each load
.
•
If a problem exists with the control, consult troubleshooting guide.
4.1.10 Water
•
Check water pressure and temperature. There should be no noticeable
change if boiler is functioning normally. Check for any noise in the system.
•
Check water piping for damage or leaks and repair as needed.
•
Check for 12-15 psig in normal operation, and look to ensure pressure does
not run up toward 30 psig at high temperature. If pressure rises sharply,
consider replacement of expansion tank. Check also for noise at high fire,
which may signal water quality problems.
•
Check water piping for damage or leaks and repair as needed.
•
Water chemistry shall be of a quality generally accepted as suitable for
hydronic applications.
See Section 1.6 for details.
•
Ensure any direct “city fill” water connections are left in the
closed
position to
minimize exposure to leaks and flooding.
4.1.11 Freeze Protection
Check freeze protection. Use only antifreeze made specifically for hydronic
systems. Inhibited propylene glycol is recommended. Antifreeze volume must be
between 25-50% of the total volume of water in the system.
CAUTION
The heat exchanger has a
small amount of combustion
chamber insulation
(refractory), which contains
ceramic fibers. When
exposed to extremely high
temperatures, the ceramic
fibers, which contain
crystalline silica, can be
converted into cristobalite
- which is classified as a
possible human carcinogen.
Care should be taken to
avoid disturbing or damaging
the refractory. If damage
occurs, contact the factory for
directions. Avoid breathing
and contact with skin and
eyes and follow these
precautions:
1.
For conditions of frequent
use or heavy exposure,
respirator protection is
required. Refer to the
“NIOSH Guide to the
Selection and Use of
Particulate Respirators
Certified under 42 CFR
84” for selection and use
of respirators certified
by NIOSH. For the most
current information, NIOSH
can be contacted at 1-800-
356-4676 or on the web at
www.cdc.gov/niosh.
2.
Wear long sleeved, loose
fitting clothing, gloves
and eyes protection.
3.
Assure adequate
ventilation.
4.
Wash with soap and water
after contact.
5.
Wash potentially
contaminated clothes
separately from other
laundry and rinse washing
machine thoroughly.
6.
Discard used insulation in
an air tight plastic bag.
NIOSH stated first aid:
•
Eye contact - Irrigate and
wash immediately.
•
Breathing - Provide fresh
air.
Summary of Contents for VFC 15-150
Page 74: ...SERVICE RECORD DATE LICENSED CONTRACTOR DESCRIPTION OF WORK DONE...
Page 75: ...NOTES...
Page 76: ...NOTES...
Page 77: ...NOTES...