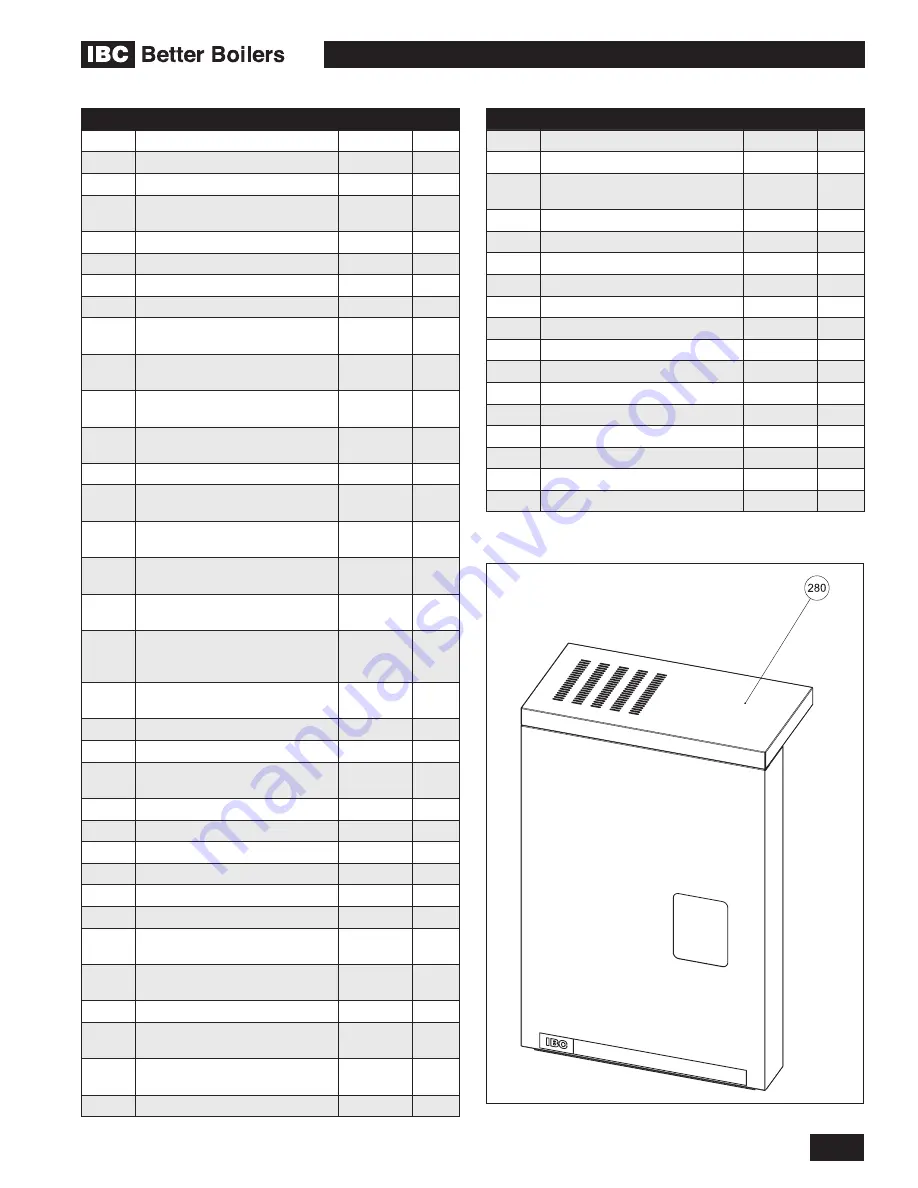
6-5
DIAGRAMS
VFC 15-150, VFC 45-225 MODULATING GAS BOILERS
ITEM# DESCRIPTION
PART#
QTY
5
FAN, NRG 137
240-048
1
10
O-RING
150-073
1
15
FAN ADAPTER PLATE
180-023
1
20
SCREW, M4x10 TAPPING,
FLAT HEAD, EQUIPPED w/FAN
3
25
AIR INTAKE, BASE
180-017
1
30
SWIRL PLATE
180-020
1
35
AIR INTAKE, COVER
180-018
1
40
GAS VALVE
180-022
1
45
SPACER, #8, 1/8” THICK, 1/4”
O.D.
150-092
3
50
SCREW, M4 x 30, TAPPING,
EQUIPPED w/GAS VALVE
3
55
SCREW #10-32 x 7/8” HEX
HEAD
150-110
4
60
GASKET, FAN - FAN
COUPLER
250-381
2
65
FAN COUPLER SPACER
250-370
1
70
NUT, #10-32, w/EXTERNAL
TOOTH WASHER
150-111
4
75
SWITCH, SNAP DISK,
MANUAL RESET, 230F
240-030
1
80
SWITCH, SNAP DISK, AUTO-
RESET, 203F
240-032
1
85
MOUNTING PLATE, SNAP
DISK
250-333
1
90
IGNITION MODULE
(ALTERNATE CAPABLE
CONTROLS 240-049)
240-004C 1
95
SCREW, SHEET METAL, #8
x 3/4”
150-021
2
100
SENSOR, WATER PRESSURE 240-006
2
105
ENCLOSURE
250-312
1
110
MOUNTING BRACKET, GAS
VALVE
250-316
1
115
SENSOR, AIR PRESSURE
240-003
1
120
TRANSFORMER
240-008
1
125
SIDE COVER, CONTROLLER
250-327
1
130
SCREW, #6-32 x 3/8”
150-014
6
135
CHASSIS, CONTROLLER PCB 250-583
1
140
PCB, CONTROLLER V10.0
230-002
1
145
SPACER, MALE - FEMALE,
#6-32 x 3/4”
150-096
4
150
FRONT COVER,
CONTROLLER
250-591
1
155
PIPE CLAMP
150-039
3
160
2” ABS AIR INTAKE
ASSEMBLY
1
165
CLIP NUT, M10, 19mm
CENTER
150-105
4
170
HEAT EXCHANGER
170-009
1
ITEM# DESCRIPTION
PART#
QTY
175
REFRACTORY, OUTER
250-287
1
180
REFRACTORY, INNER
250-306
1
185
GASKET, HEAT EXCHANGER
LID
250-328
1
190
LID, HEAT EXCHANGER
250-284
1
195
SCREW, M10 x 55, HEX HEAD 150-106
4
200
WASHER, FENDER, M10
150-104
4
205
IGNITOR
240-002
1
210
GASKET, IGNITOR
250-050
1
215
SCREW, M4 x 10, PAN HEAD
150-013
4
220
SIGHT GLASS HOLDER
250-309
1
225
GASKET, SIGHT GLASS
250-060
2
230
SIGHT GLASS
250-059
1
235
GASKET, BURNER
250-308
2
240
BURNER
180-021
1
245
V-CLAMP
150-071
1
250
FAN COUPLER
250-280
1
280
FRONT COVER, VFC 225
250-315
1
Diagram 6.2-1 (Parts List)
Diagram 6.2-2: Door Assembly – VFC 45-225
Summary of Contents for VFC 15-150
Page 74: ...SERVICE RECORD DATE LICENSED CONTRACTOR DESCRIPTION OF WORK DONE...
Page 75: ...NOTES...
Page 76: ...NOTES...
Page 77: ...NOTES...