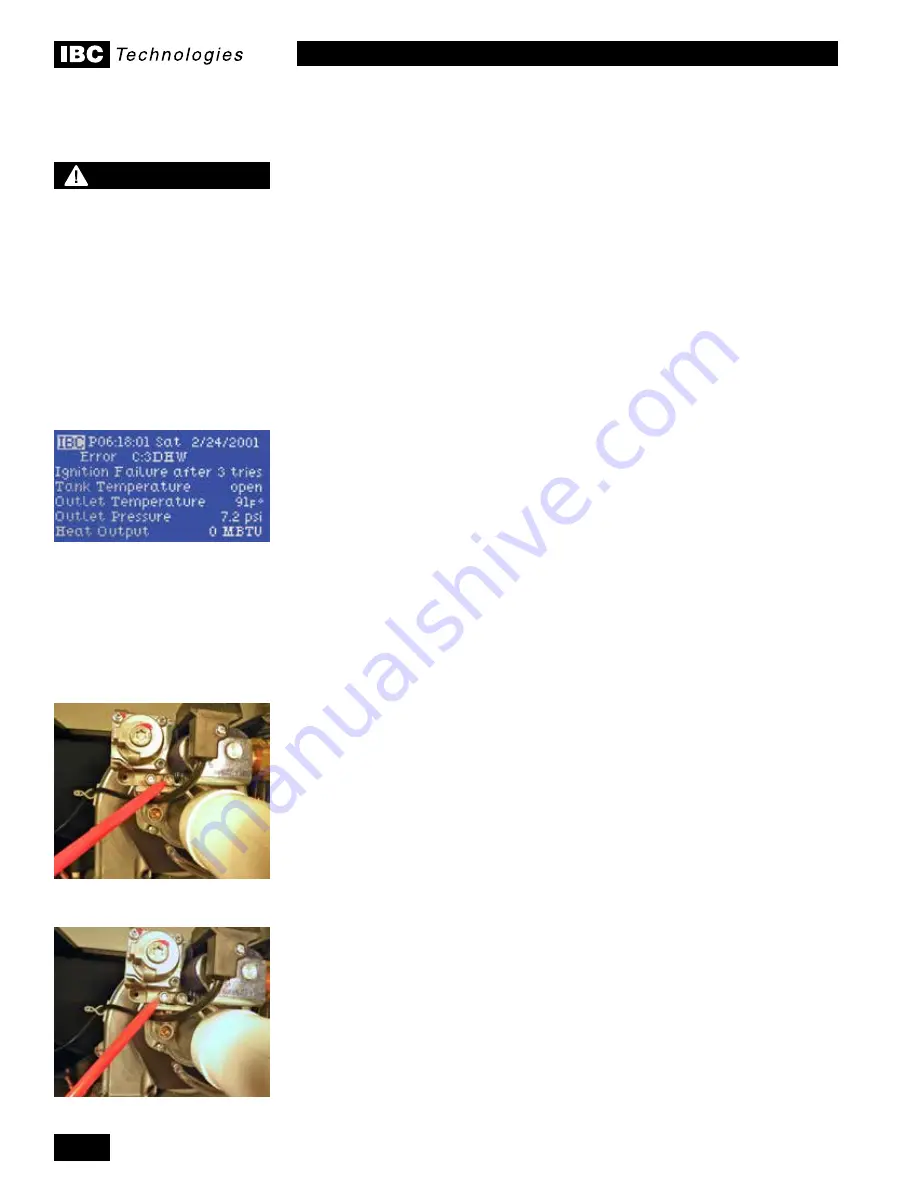
INSTALLATION AND OPERATION INSTRUCTIONS
3-2
SL 30-175, SL 45-260 MODULATING GAS BOILERS
3.2 Prior to start-uP
3.2.1 Pre-Ignition Checks
1.
Ensure venting system is complete and seal tested. Confirm any common
venting system at the installation site is isolated and independent of the sl
boiler, that any holes left from removal of a previous boiler have been sealed,
and that any resizing of the old flue has been done. Fill condensation trap.
2.
Check water piping system is fully flushed and charged, and that all air has
been discharged through loosened bleed caps. note it is possible to switch
all pumps on/off from the keypad – without a call for heat. this greatly
simplifies system filling and air bleeding (go to
Installer Setup
, drop down
to
Pump Purge
and toggle to
On
. When complete, return to
Off
, or this will
automatically occur with a call for heat). use a minimum water pressure of 12
psig. And confirm pressure relief valve is installed and safely drained.
3.
Check to see that adequate gas pressure is present at the inlet gas supply
test port. Open the test port (using a small (1/8” or 3 mm) flat screwdriver,
open the test port by turning its center-screw 1 full turn counterclockwise.
Connect a manometer and open the gas control valve. requirements are
minimum 5” w.c and maximum 14” w.c. Check to ensure no gas leaks.
4.
Perform a final check of electrical wiring and provide power to the boiler to
initialize operation.
3.2.2 Test Ignition Safety Shutoff
With the boiler in operation, test the ignition system safety shutoff device by
shutting the gas control valve immediately outside the boiler case. ensure boiler
has shut off and the appropriate error information is displayed on the lCd
screen. to restart boiler, reset power.
CoMMissioning
the sl 30-175 and sl 45-260 modulating boilers are factory calibrated to
operate with natural gas (or propane if so ordered) at sea level. the Zero-offset
valve adjustment cap has been factory sealed using red paint-seal compound.
This cap must not be tampered with. The Zero-offset screw is not to be
adjusted in the field.
the gas:air ratio adjustment screw may have to be
adjusted to attain optimum combustion results if required, however,
no mixture
adjustment shall be performed unless done by a qualified technician using
properly functioning and calibrated combustion analyzing equipment.
Upon initial set up, the installer can enter the site elevation to compensate
for altitude.
Without such intervention, the gas valve will automatically de-rate
the maximum input in accordance with the density altitude, by approximately 2%
per 1,000’ above sea level. the gas valve’s zero governor will ensure that the
gas:air mixture is not affected at altitude. to verify the proper operation of the
gas valve in the field, the following procedure can be carried out by a qualified
technician
(see Figure 32).
1.
With a small (1/8" or 3 mm) flat screwdriver, open the inlet gas supply
pressure test port by turning its center-screw 1 full turn counterclockwise.
attach a manometer to the pressure test port and turn on gas to appliance.
static manometer reading should be ideally 7” w.c., for natural gas and
11” w.c. for Propane. Minimum and maximum static pressure should be
between 5” and 14” w.c. Monitor pressure throughout the comissioning
procedure. Pressure may droop up to 1” to 2” w.c. at high fire but under no
circumstances should it drop below 4” w.c. at the gas valve inlet test port.
3.3
Inlet gas supply pressure test port
Manifold pressure test port
Error displayed after testing ignition
safety shut off
WARNING
Fill trap with water before
boiler is first fired to prevent
exhaust fumes from entering
room. Never operate the
boiler unless the trap is filled
with water.
Failure to comply will result
in severe personal injury or
death.
Summary of Contents for SL 30-175
Page 76: ...NOTES...