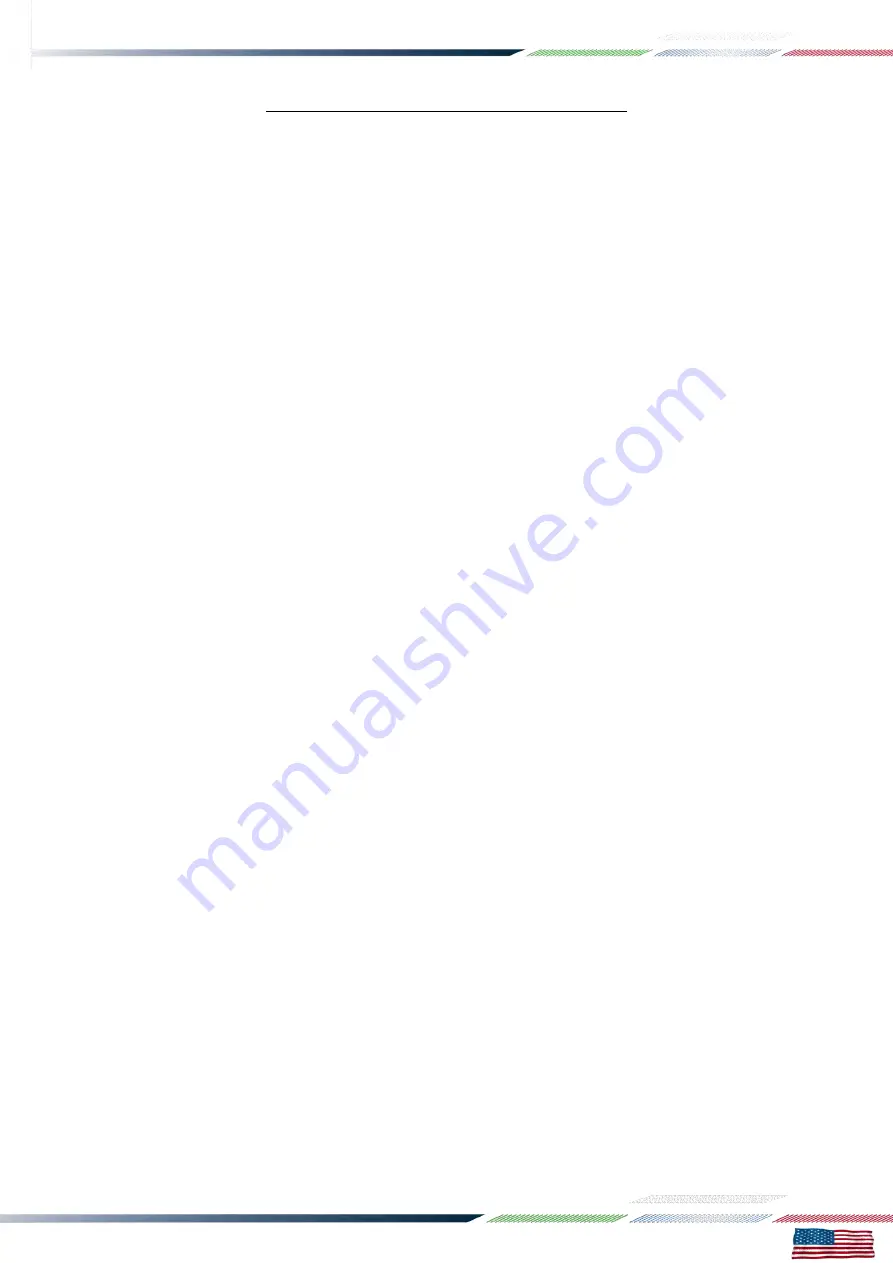
MAN-85 – USA
GENERAL DESCRIPTION OF THE ENGINE
This engine of the TaG series (Touch and Go) has been expressly designed and
developed for the powering of karts, either for hobby or racing, on closed tracks destined
for this specific purpose. When designing this new line of engines, the technical solutions
already adopted for the high performance engines were used, in order to guarantee the
highest reliability and lasting of components, when the operating limits are respected.
The motor is a single cylinder using the two stroke principle.
The cylinder and the crankcase are in aluminium alloy.
The pressed-in liner is made of centrifugated cast iron, fully machined to guarantee the
best possibile stability and sliding homogeneity.
The head is separated from the cylinder and secured by studs.
The crankshaft is built and supported by ball-bearings. The crankshaft is of steel alloy,
hardened and tempered, as is the connecting rod which runs on roller bearings.
The ignition includes a 2 pole stator/rotor, an H.T. coil, a starter relay and complete wiring
harness.
The spark is generated also without a battery: it is therefore possibile, in case of
emergency, to start the engine with an external starter unit.
The engine has an integrated electric starter. By pushing the green start button, the starter
activates a Bendix type gear which engages the starter ring assembled on the clutch.
The engine is provided with a dry centrifugal clutch with low maintenance and with
interchangeable sprocket .
The carburettor type is a diaphragm (series Tillotson HW) includes an integrated fuel pump
and filter, and is able to operate in any position.
The battery (12 V- 7.2Ah) is a sealed, no maintenance, battery is NOT supplied, the
battery supports box be easily adapted to all existing chassis.
The exhaust, included in the supply, is already tuned for the best possibile performance.
The engine is also equipped with a centrifugal dry clutch with low maintenance with
incorporated sprocket.
The exhaust system, including in the supply, is already tuned and optimized to ensure the
best possible performance.