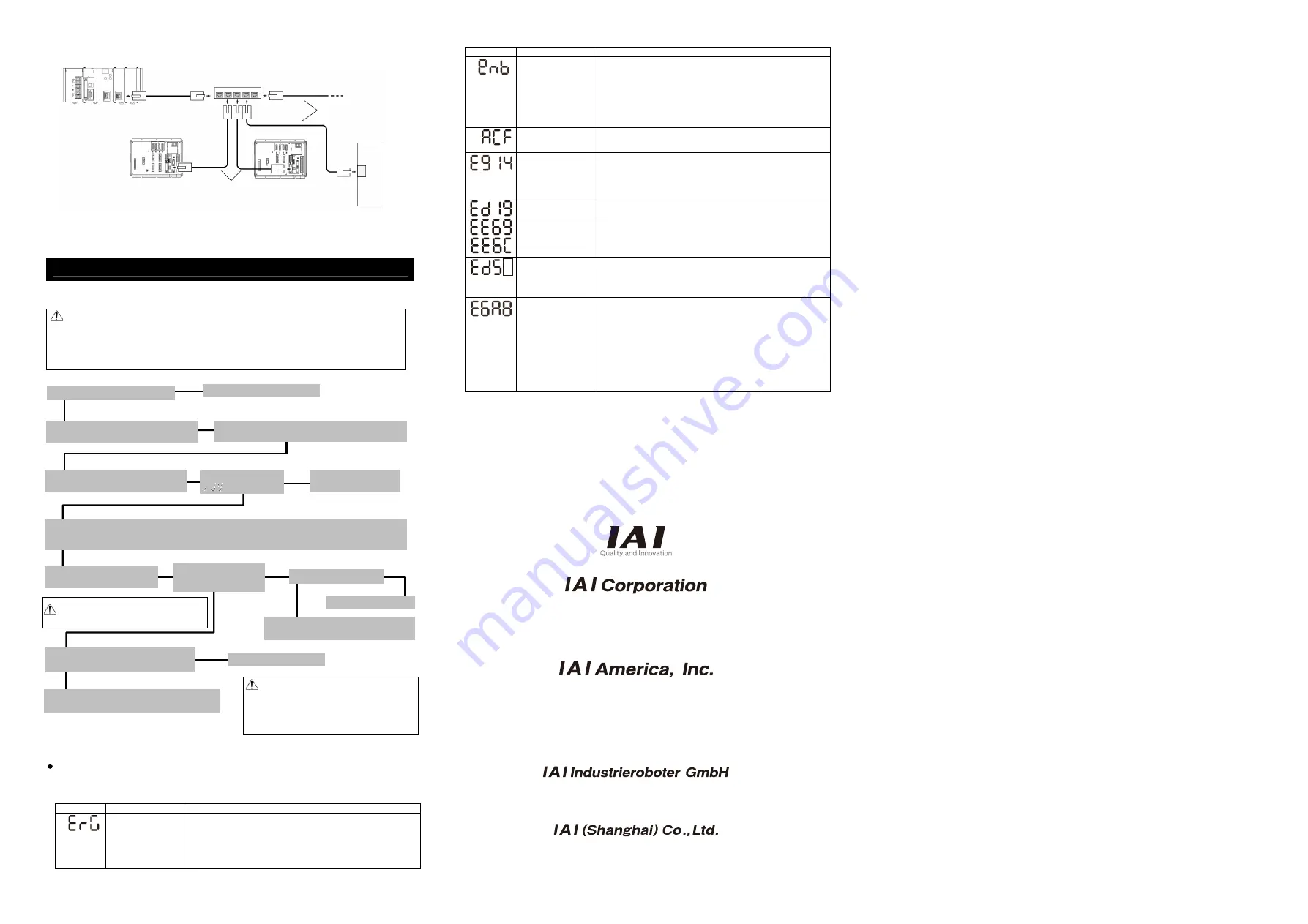
PLC (EtherNet/IP Master Unit)
Ethernet Cable
Ethernet
Cable
XSEL-R
XSEL-S
Hub
Ethernet
Cable
*
*
*
Other Slaves
*
Ethernet Cable: 100m or less of straight cable with Category 5e or more
(Double shielded cable braided with aluminum foil recommended)
(Note) There is no need of terminal treatment.
Starting Procedures
When using this product for the first time, make sure to avoid omission and incorrect wiring by referring to
the procedure below. “PC” stated in this section means “PC software“.
Note:
•
Make sure to put the brake release switch of the controller on the right side (NOM) before
turning ON the power. If on the left (RLS), the actuator may drop with its weight and pinch
yourself or damage the work piece.
•
Make sure to connect the robot with the manufacturing number indicated on the
controller.
Connecting a robot not indicated may cause a wrong operation.
Set-up for operation is complete.
Establish the setting that suits to your operation patterns.
Troubleshooting
Shown below are the alarms that you may often see after power up. Please follow the instructions below.
Please refer to the Operation Manual for other alarms.
Status display
Status contents
Cause and Remedy
During Emergency-stop
It is not an alarm.
•
It is generated when the emergency stop switch in the teaching pendant or
the personal computer application software is not cancelled. In such case,
cancel it.
•
It is generated when the personal computer cable is not connected to the
emergency stop box. Please establish the connection.
•
Check the emergency stop circuit.
Status display
Status contents
Cause and Remedy
Safety Gate Remains
Open
Deadman Switch OFF
It is not an alarm.
•
It is generated when the system I/O ENB signal is opened. Check the ENB
signal. (It is generated when the safety gate is open. Close the safety gate.)
•
This occurs when AUTO/MANU switch is on MANU side for
XSEL-R/RX/RXD Controller but PC or teaching pendant is not connected.
Connect the personal computer or the teaching pendant or set the
AUTO/MANU switch to “AUTO”.
•
When the actuator is to be started up, hold the deadman switch on the
teaching pendant to turn it ON.
AC Power Interruption
Momentary Power Failure
Power Voltage Drop
It is generated when the power voltage is not supplied. It will be generated, for
example, in the case that the 100V AC is supplied to the controller with 200V
AC specified. Check the power supply.
Absolute Data Backup
Battery Voltage Error
It will be generated in the case that the battery has not been attached, or the
battery voltage is dropped.
In the case of the actuator for the single-axis robots or Cartesian robots with
the absolute data specifications, it is generated when the power is connected
for the first time.
Perform the absolute reset.
Encoder Reception Time
Out
It is generated when the encoder is broken, the cable is broken or the encoder
cable is not connected to the controller. Check the wiring.
24V I/O error
DO Output Current Error
It is generated when the +24V power for I/O is not supplied.
Check the power supply.
(How to start up the controller without connecting the I/O 24V power)
Set the I/O parameter No. 10 to No. 13 corresponding to “0”.
FieldBus Error
It is generated when the fieldbus link connection is not established.
Check the link cable connection, I/O parameter and PLC parameter settings.
(How to start up the controller without connecting the field bus)
Set the I/O parameter No. 18 or No. 235 corresponding to “0”.
RC Gateway Serious
Breakdown Error
When the RC gateway is used and an error occurs in the controller mount SIO
(serial communication), it is caused.
The following causes are supposed.
•
All effective RC axes are missing (not recognized).
→
A cable disconnection or wire breaking is supposed. Check the wiring.
•
The power switch on the main CPU shows 0V.
→
Set the +5V power switch to right side (+5V supply side).
•
The DPRAM access right can not be obtained for one hour or more in the
mount SIO.
→
Check the parameters for the X-SEL or RC controller.
•
A serious error such as a CPU error is caused in the mount SIO.
→
It is caused by the hardware breakdown. Consult with our company.
No
→
Important Check Item
•
Have you performed the frame grounding (FG) and protective earthing (PE).
•
Has the noise countermeasure been taken?
↓
Yes
No
→
→
Power Supply and Alarm Check
Connect the personal computer or teaching pendant,
connect the power.
Have an appropriate treatment
following the content of the status
display.
Servo ON
Turn ON the servo motor with the personal
computer or teaching pendant operation.
Check Item
Check that SV is ON in Position
Edit Window on PC software or
teaching pendant.
During the alarm output, confirm the alarm description and
deal with the condition with the personal computer or
teaching pendant operation.
No
→
→
←
Yes
↓
↓
Yes
Check Item
Is the status display showing
[
] ?
Parameter Settings [Refer to Chapter 6]
Set the parameters including I/O parameter with the personal computer or teaching pendant operation.
[Reference] Set I/O Parameters No. 10 to 11 to 0 (Not to Monitor Errors) if starting up the system without connecting I/O 24V power supply for PIO
Type. Set either of I/O Parameter No. 18 or 235 to 0 (Not to Monitor Errors) if starting up the system without connecting Fieldbus for Fieldbus Type.
Check the emergency stop circuit.
Product Check
Have all the items been delivered?
↓
Is the motor cable connected?
No
→
↓
Yes
↓
Yes
No
→
Confirming the operation of the actuator
Confirm that the full stroke operation is performed without any trouble
with the jog operation.
↓
Yes
Check of Safety Circuit
Does the emergency stop circuit (drive cutoff circuit) work
properly and turn the servo OFF?
•
To ensure safety, it is recommended that safety
speed be enabled during initial movements.
•
When the actuator is installed vertically , be
careful so you would not pinch your hand or
damage the robot hand with the actuator
dropped by its own weight when the brake
release switch is put on [RLS] side.
Installation and Wiring
Install the controller and robot and perform installation and
wiring according to the contents in this book.
Contact your local IAI distributor.
Connect the motor cable.
The actuator may drop slightly by its own weight as a
result of turning on/off repeatedly if it is installed
vertically. Be careful so you would not pinch your hand
or damage the robot hand.
↓
Head Office: 577-1 Obane Shimizu-KU Shizuoka City Shizuoka 424-0103, Japan
TEL +81-54-364-5105 FAX +81-54-364-2589
website: www.iai-robot.co.jp/
Ober der Röth 4, D-65824 Schwalbach am Taunus, Germany
TEL 06196-88950 FAX 06196-889524
SHANGHAI JIAHUA BUSINESS CENTER A8-303, 808, Hongqiao Rd. Shanghai 200030, China
TEL 021-6448-4753 FAX 021-6448-3992
website: www.iai-robot.com
Technical Support available in USA, Europe and China
Head Office: 2690 W. 237th Street, Torrance, CA 90505
TEL (310) 891-6015 FAX (310) 891-0815
Chicago Office: 110 East State Parkway, Schaumburg, IL 60173
TEL (847) 908-1400 FAX (847) 908-1399
TEL (678) 354-9470 FAX (678) 354-9471
website: www.intelligentactuator.com
Atlanta Office: 1220 Kennestone Circle, Suite 108, Marietta, GA 30066
Manual No.: ME0314-1C