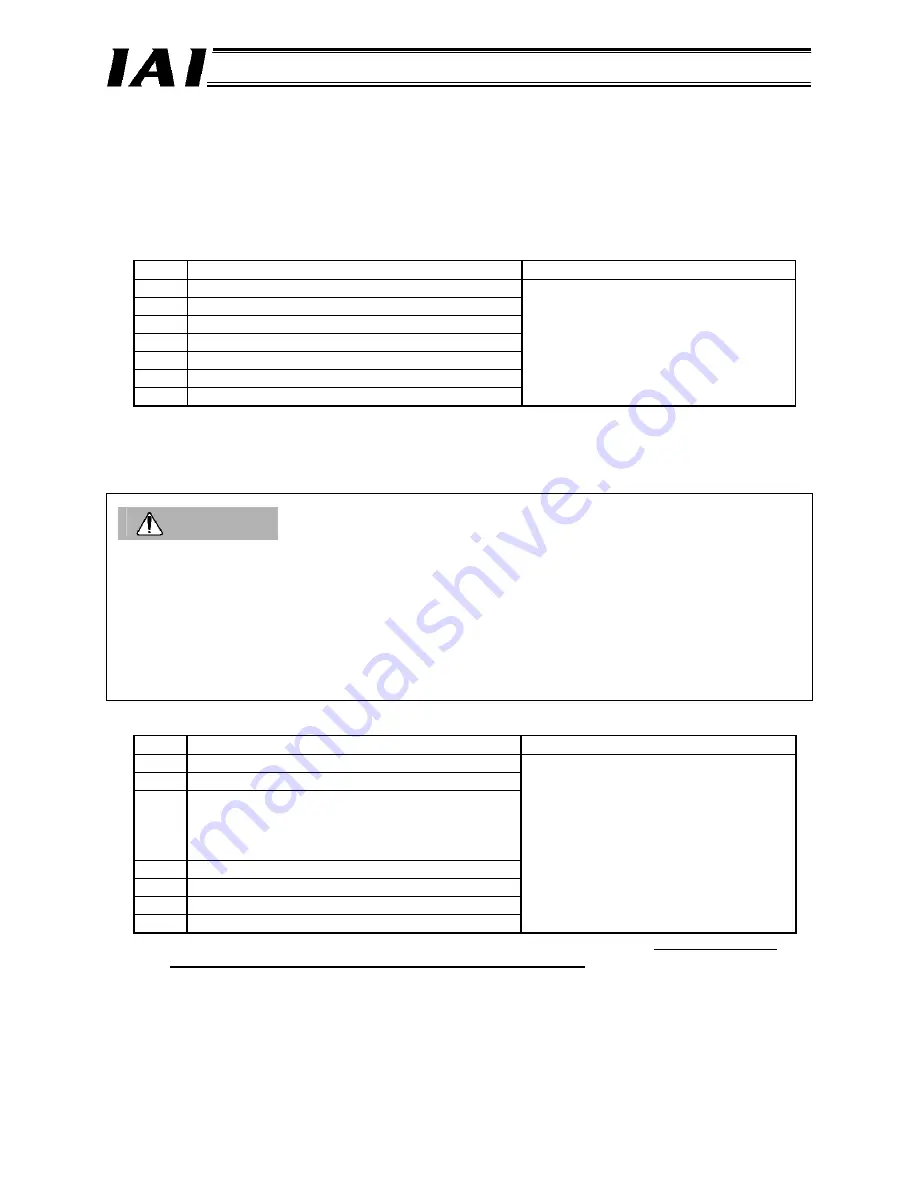
PfofiBus Gateway
[6] Group specification broadcast command
The axes specified by the group number are started simultaneously to the position specified by the
position number.
When this command is issued, the Gateway and each controller communicate in the broadcast
mode, meaning that the controller does not return any response.
The response result indicated by the PLC input only means that the command has been sent
successfully to the applicable controllers; it does not indicate the status of each controller. Check the
status signal of each axis to determine if the command was executed successfully.
Byte+
PLC output (request)
PLC input (response)
+4 0D03H
6
Position number *1
8
Group ID number *2
Same as the value in the request
command if normal.
10 0
12 0
14 (RSV)
16 (RSV)
*1 Values that can be specified vary depending on the type and settings of the applicable ROBO
Cylinder controller.
*2 If this number is “0,” all linked axes will move regardless of the group specification.
A desired group number can be set using the applicable system parameter in the PC software.
Caution
1. If a movement command is issued to each axis via a control signal while the movement specified
by this command is still in progress, the movement by this command will be cancelled and the
operation corresponding to the latest movement command will take place. Since each axis
effectively has two movement command interfaces, make sure the two interfaces are used
exclusively to each other.
2. Even when the link was cancelled by turning OFF the CFG bit of the gateway control signal, once
the link is established again the controller will always receive this command to perform the
specified operation.
[7] PIO/Modbus switching command
Byte+
PLC output (request)
PLC input (response)
+4 0DA1H
6 0
8 Coil
ON/OFF
00FFH = ON: Modbus (Disable PIO command)
0000H = OFF: PIO (Enable PIO command)
*1 to *3
Same as the value in the request
command if normal.
10 0
12
Axis number 0 to FH
14 0
16 0
*1 The PIO/Modbus switching status is reflected in the status signal PMSS. Also note that this
command cannot be set for position number specification axes (if issued, the command will
generate an invalid request command error (0103H)).
*2 Even if the coil is set to OFF (Enable PIO command), axis position data can still be changed
from the PLC via Modbus communication (although the link must be retained).
*3 The controller will still accept and execute movement commands via Modbus communication
even after the control authority is switched to PIO.
73