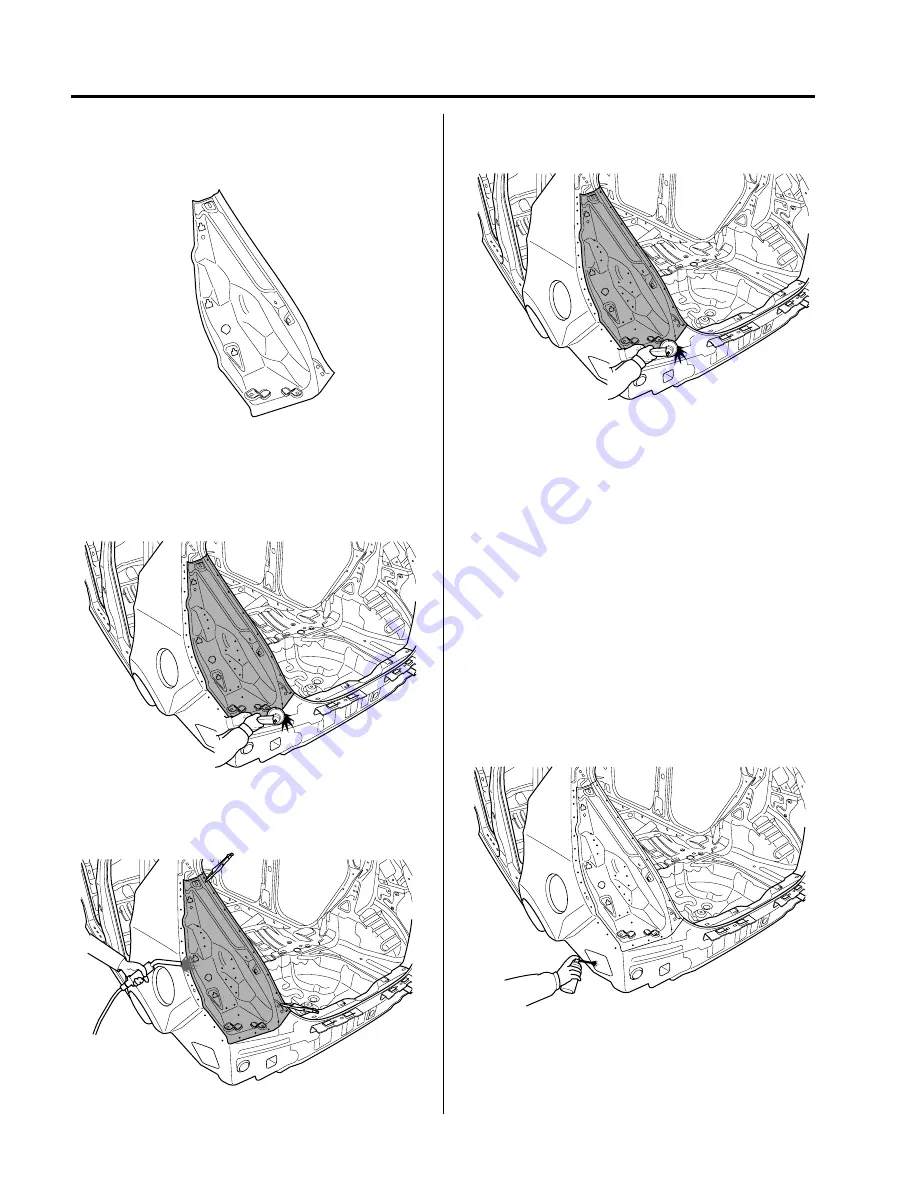
BP-60
BODY PANEL REPAIR PROCEDURE
16. Clean and prepare all welds, remove all residue.
17. Apply the two-part epoxy primer to the interior of the
rear floor side member.
18. Apply an anti-corrosion to the interior of the rear floor
side member.
(Refer to the CORROSION PROTECTION)
19. Prepare exterior surfaces for priming, using wax and
grease remover.
20. Apply metal conditioner and water rinse.
21. Apply conversion coating and water rinse.
22. Apply the two-part epoxy primer.
13. Fit and clamp the new rear combination lamp housing
panel assembly in place.
14. Measure each measurement point (Refer to the BODY
DIMENSIONS) and correct the installation position.
15. MIG plug weld all holes.
BFDBP6710
BFDBP6701C
BFDBP6701B
BFDBP6701C
BFDBP6701D
Summary of Contents for 2008 Elantra Neos
Page 19: ...BODY CONSTRUCTION BC 5 BFDBC6112 Z ...
Page 21: ...BODY CONSTRUCTION BC 7 Cross Sectional Views BFDBC6115 TOP VIEW RH SIDE VIEW RH B B C C A A ...
Page 22: ...BC 8 BODY CONSTRUCTION Cross Sectional Views BFDBC6117 TOP VIEW LH SIDE VIEW LH ...
Page 28: ...BC 14 BODY CONSTRUCTION Cross Sectional Views BFDBC6138 J J C C D D A A G G B B K K E E ...
Page 32: ...BC 18 BODY CONSTRUCTION BFDBC6149 TOP VIEW SIDE VIEW F F A A B B C C D D E E ...
Page 35: ...BODY CONSTRUCTION BC 21 BFDBC6156 Cross Sectional Views A A ...
Page 38: ...BC 24 BODY CONSTRUCTION Cross Sectional Views BFDBC6164 TOP VIEW REAR VIEW A A ...
Page 41: ...BODY CONSTRUCTION BC 27 Cross Sectional Views BFDBC6168 ROOF SUN ROOF C C E E A A B B Y Z ...
Page 43: ...BODY CONSTRUCTION BC 29 Cross Sectional Views BFDBC6197 C C A A B B HOOD ...
Page 47: ...BODY CONSTRUCTION BC 33 Cross Sectional Views BFDBC6190 D D B B A A E E C C TAIL GATE ...
Page 132: ...BS 2 BODY SEALING LOCATIONS EXTERIOR BFDBS6006 G K K A C B D E F J J H H I I N N L L M M ...
Page 138: ...BS 8 BODY SEALING LOCATIONS UNDER BODY BFDBS6502 BFDBS6002 BFDBS6501 A B A B ...