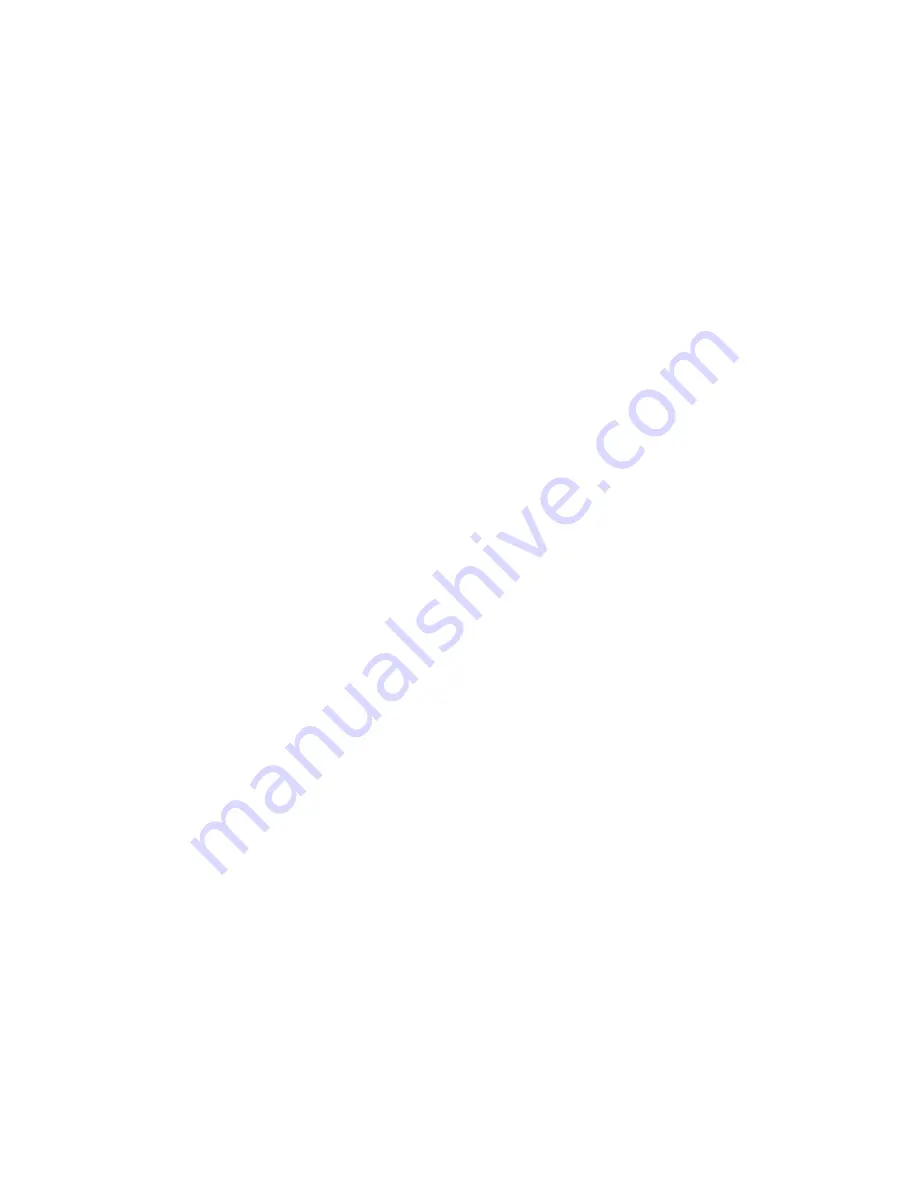
Load Moment Interrupt (Optional)
This function disables the lift and backward tilt
functions via a pressure switch in the main control
valve. This function also limits the maximum load
that can be lifted.
CAN BUS COMMUNICATION
CAN Bus communication can be considered both as
an input and output signal.
The hydraulic controller communicates via the SAE
J1939 CAN Bus circuit with the following control-
lers:
• Instrument cluster - for displaying mes-
sages on the fault code display. See Fault Co-
des.
• Engine Control Module - for the Anti-Stall
and Temperature Protection features. See
Programmed Features.
• Transmission Controller (APC200 or
TCU) - for the Loaded Speed Reduction fea-
ture. See Programmed Features.
OUTPUT SIGNALS
Output signals can be digital (ON/OFF), analog
(with a certain value and within a specified range),
or CAN bus messages.
Depending on settings and programmed features,
the output signals can be different than standard
programming. See Settings and Programmed Fea-
tures.
Analog Outputs
Analog signals for proportional hydraulic functions
are PWM outputs and operate in a nominal range
of 6-12-18 volts. The neutral position of the valve
corresponds with 12 volts. 6 volts and 18 volts each
determine maximum demanded flow and flow di-
rection.
For front-end equipment using fixed PT hydraulic
lines, the analog output signal is between 12 and 6
volts, which determines the valve flow in one direc-
tion only. The direction of the hydraulic function is
determined by a separate valve that receives a sep-
arate digital signal.
Analog outputs are used for the lift, tilt, and auxili-
ary functions.
Digital Outputs
Digital signals are ON/OFF signals providing 24
volts when activated, and 0 volts when deactivated.
In general, digital signals are used for auxiliary
functions.
For alternating PT systems there is a maximum of
four digital outputs available: Digital Out Aux0,
Digital Out Aux1, Digital Out Aux2, and Digital
Out Aux3.
For fixed PT systems, each of the above Digital Out
signals receives an additional letter designation (A
or B) to indicate the different flow directions for
these functions. The letters A and B correspond to
flow direction as intended by the lever movement.
The connector housing on the auxiliary valve pre-
vents incorrect connection of the signal wires.
One digital output (pin 39) is used as a power sup-
ply for all PVEA and PVEH solenoids.
Another digital output (pin 40) is used to enable the
lowering functionality when there is no oil supply
coming from the hydraulic pumps.
PROGRAMMED FEATURES
The controller has been programmed for a number
of standard features and can also be programmed
for optional features. The following standard and
optional features are described below:
• Anti-Stall (Standard)
• Temperature Protection (Standard)
• Low Temperature Protection (Standard)
• High Temperature Protection (Option)
• Dynamic Control (Option)
• Loaded Speed Reduction (Option)
2200 SRM 1481
Description
5