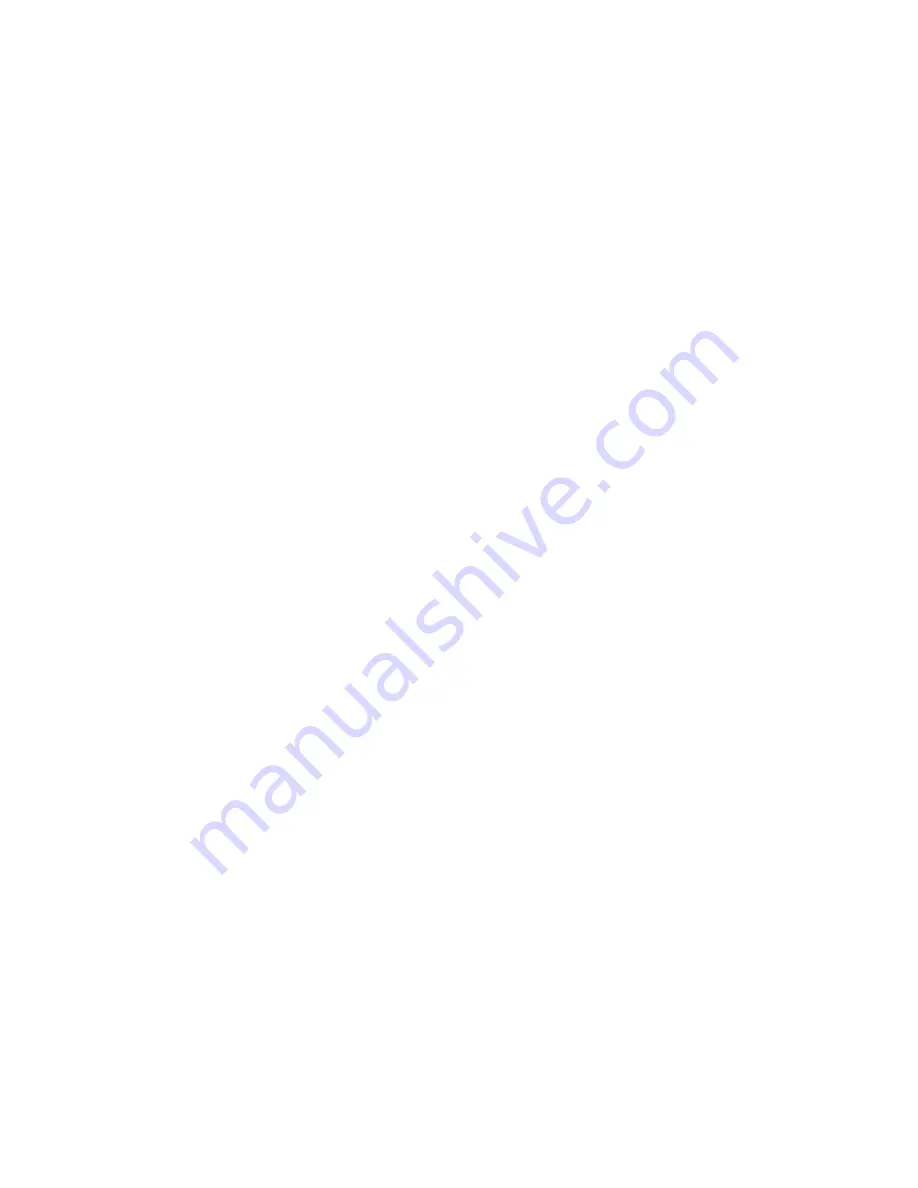
Elongation Through Wear
When the chain articulates, the inner plates rotate
over the link pin and cause wear. Wear reduces the
pin diameter and enlarges the hole in the plate,
which results in chain elongation. When elongation
has reached 3%, the entire chain must be replaced.
Speed of Wear
The speed of wear of link pin and inner plates
depends on the following factors:
• Load and impact load. The chain load
depends on the weight lifted and the weight of
the carriage and forks. Impact loads occur,
when the truck drives over uneven surfaces.
The forces generated by an impact load can be
a multiple of those of normal chain load.
• Number of link movements. The number of
link movements directly relates to the
number of times the chain passes over the
sheave when the mast is raised or lowered.
Chain elongation must therefore be measured
at that chain section that runs over the
sheave most often. The chain section close to
the carriage will have the lowest number of
articulations and is irrelevant for measuring
chain elongation.
• Lubrication. An oil film at the contact area
between link pin and inner plates reduces
wear and preserves the smooth surface of this
contact area. The oil film is particularly
important for new chains, when the contact
areas are being broken in. Therefore, it is
essential that new chains are lubricated with
oil before they are put into service. See
Plate Height Wear
The chain plates also wear at the contact area
between chain and chain sheave. When the chain
moves onto the sheave, the plates rotate slightly to
follow the radius of the sheave. In combination with
the high pressure between chain plates and sheave,
this movement causes wear, which affects the
strength of the plates. The maximum allowed wear
is 5% of the original link plate height.
Lubrication
An oil film at the contact area between link pin and
inner plates reduces wear and preserves the smooth
surface of this contact area. See Figure 9.
The oil film between pin and plates is pushed away
under load conditions and must be allowed to
restore daily by removing the load and allowing oil
to penetrate again. Restoring the oil film is effected
by the capillary action of oil. This process is to be
considered separately from applying new oil to the
chain.
Insufficient lubrication causes damage to the
smooth contact area between pin and plates. The
resulting increased friction can cause that the inner
plates rotate the pin in the outer plates, which
destructs the integrity of the chain structure.
Restoring the Oil Film
The capillary action of oil allows restoring the oil
film between chain pin and inner plates, provided
that sufficient free flowing oil is present between
the plates, and provided that chain tension is as low
as possible during a certain time.
The required time to maintain this low chain
tension varies with chain cleanliness and
availability of free flowing oil between the plates.
This time can be as short as 30 minutes or extend
infinitely when conditions are unfavorable.
Chain tension should not exceed the own weight of
the chain when restoring the oil film. This means
that chains must be slack.
Interruption of the oil film between pin and chain
outside reduces the capillary action, but also allows
entry of humidity. Humidity activates the formation
of corrosion products, making it even more difficult
for oil to reach the pin contact area. This means
that new fresh oil must be applied to the chain
before the oil film on the outside is interrupted.
Maintenance
The purpose of applying new oil to chain is to
replenish free flowing oil and restore outside oil
film. Adding new oil will extend the proper
conditions for restoring the oil film at the pin area.
The interval for applying new oil depends on applied
load, the number of chain articulations, and
ambient conditions like rain, temperature, presence
of dust and dirt.
In many cases the simple application of oil on the
chains is sufficient to cover the period until the next
planned service interval. Main pre-condition is that
contamination has not progressed too far, which
would prevent oil to penetrate.
4000 SRM 1664
Description And Operation
7