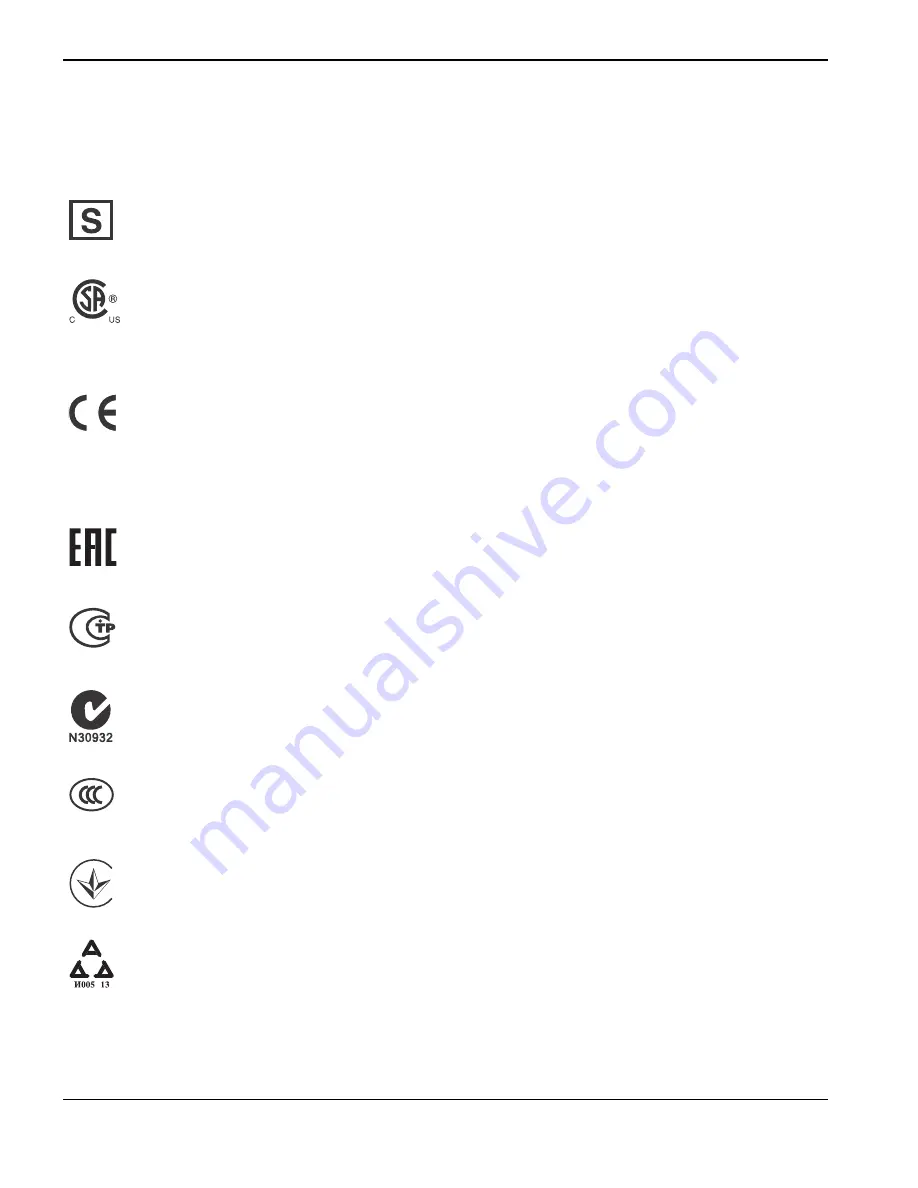
24
Powermax125
Operator Manual 808080 Revision 0
1 – Specifications
Symbols and markings
Your Hypertherm product may have one or more of the following markings on or near the data plate. Due to differences
and conflicts in national regulations, not all marks are applied to every version of a product.
S mark
The S mark indicates that the power supply and torch are suitable for operations carried out in
environments with increased hazard of electrical shock according to IEC 60974-1.
CSA mark
Hypertherm products with a CSA mark meet the United States and Canadian regulations for product
safety. The products were evaluated, tested, and certified by CSA-International. Alternatively, the product
may have a mark by one of the other Nationally Recognized Testing Laboratories (NRTL) accredited in
both the United States and Canada, such as Underwriters Laboratories, Incorporated (UL) or TÜV.
CE mark
The CE marking signifies the manufacturer’s declaration of conformity to applicable European directives
and standards. Only those versions of Hypertherm products with a CE marking located on or near the
data plate have been tested for compliance with the European Low Voltage Directive and the European
Electromagnetic Compatibility (EMC) Directive. EMC filters needed to comply with the European
EMC Directive are incorporated within versions of the product with a CE marking.
Eurasian Customs Union (CU) mark
CE versions of Hypertherm products that include an EAC mark of conformity meet the product safety and
EMC requirements for export to Russia, Belarus, and Kazakhstan.
GOST-TR mark
CE versions of Hypertherm products that include a GOST-TR mark of conformity meet the product safety
and EMC requirements for export to the Russian Federation.
C-Tick mark
CE versions of Hypertherm products with a C-Tick mark comply with the EMC regulations required for
sale in Australia and New Zealand.
CCC mark
The China Compulsory Certification (CCC) mark indicates that the product has been tested and found
compliant with product safety regulations required for sale in China.
UkrSEPRO mark
The CE versions of Hypertherm products that include a UkrSEPRO mark of conformity meet the product
safety and EMC requirements for export to the Ukraine.
Serbian AAA mark
CE versions of Hypertherm products that include a AAA Serbian mark meet the product safety and EMC
requirements for export to Serbia.
s