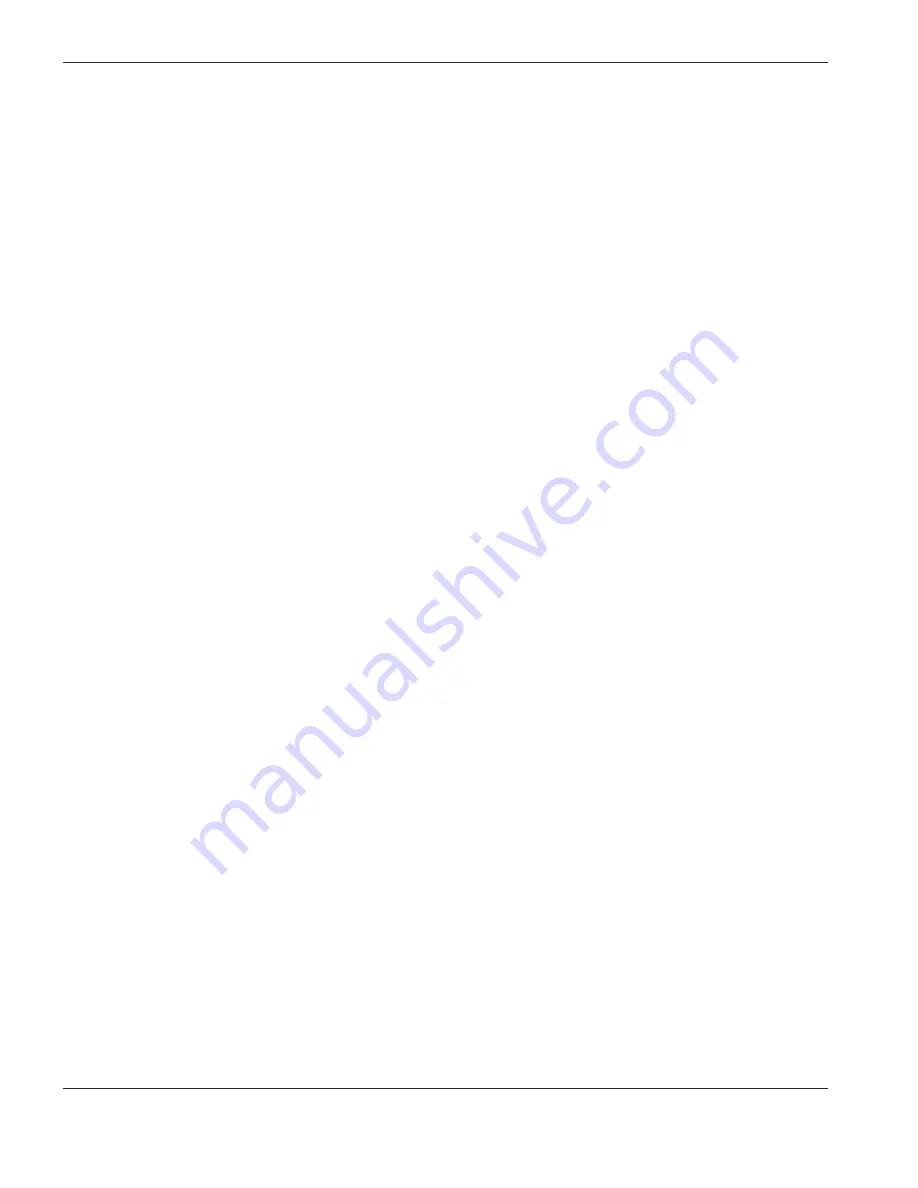
OPERATION
3-2
Duramax Retrofit Torch
Operator Manual
Using the cut charts
The following sections provide cut charts for each set of mechanized consumables. A consumable diagram with part
numbers precedes each cut chart.
The cut charts are intended to provide a good starting point for each different cut assignment. Every cutting system
requires “fine tuning” for each cutting application in order to obtain the desired cut quality.
The arc voltage increases as the consumables wear and the voltage setting should be increased to maintain the correct
Torch-to-Work Distance.
The 45 amp nozzle (part number 220941) provides the best results across the 40 - 55 amp cutting range for both the
mechanized shielded and unshiedled consumables.
Note:
Hypertherm collected the data under laboratory test conditions using new consumables.
• Maximum travel speeds are the fastest travel speeds possible to cut the material without regard to cut quality.
• Optimum travel speeds provide the best cut angle, least dross and best cut surface finish.
• Best Quality Settings (cut speed and voltage) — Settings that provide the starting point for finding the best
cut quality (best angle, least dross, best cut-surface finish). Adjust the speed for your application and table to
obtain the desired result.
• Production Settings (cut speed and voltage) — 80% of the maximum speed ratings. These speeds result in the
greatest number of cut parts, but not necessarily the best possible cut quality.
Summary of Contents for Duramax Series
Page 2: ......
Page 10: ......
Page 30: ...Torch setup 2 16 Duramax Retrofit Torch Operator Manual ...
Page 58: ...OPERATION 3 28 Duramax Retrofit Torch Operator Manual ...