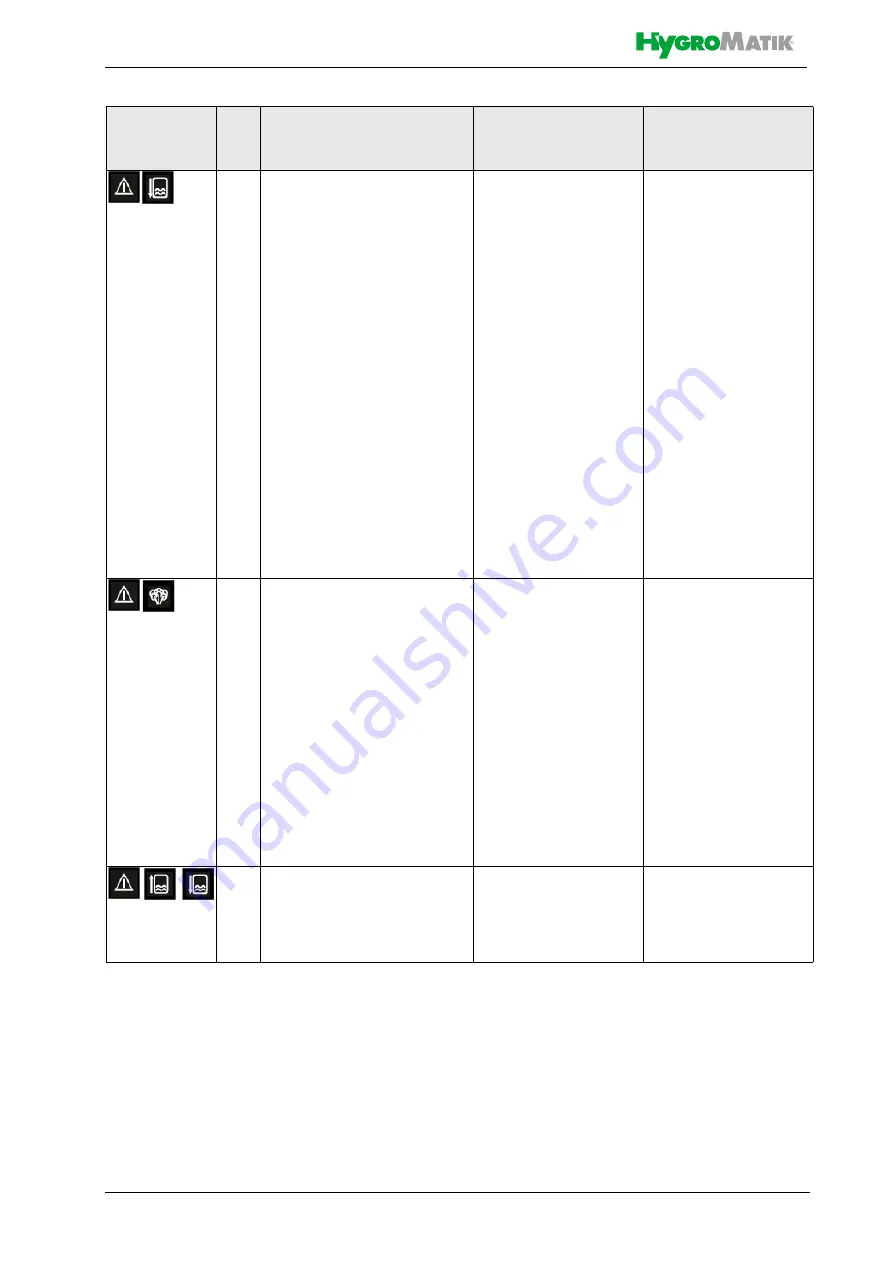
Page 73
061
062
065
066
067
Blow-down fault
, relates to:
Partial blow-down
Full blow-down
Max level blow-down
Stand-by blow-down
Start_blow-down
Indicated blow-down was not
successful
•
Blow-down pump not
driven
- electrical wiring not
o.k.
- Main PCB relay not
energised
- Check wiring and re-
place, if required
- Measure voltage on
main PCB terminal 10
against N; replace
PCB, if required
•
Blow-down pump de-
fective
•
Replace blow-down
pump
•
Blow-down pump
working but water is
not drained (i.e. cylin-
der drain is blocked)
•
Clean cylinder and
cylinder base carefully
to ensure that no
blocking will occur in
the near future
•
Blow-down pump
blocked by hardeners
•
Check blow-down
pump, drainage sys-
tem and steam cylinder
for hardeners and
clean
120
Thermo switch
One of the thermo switches
has triggered
•
Thermo switch on
steam cylinder cover
has triggered due to
lime coating on heating
element
•
Switch off power sup-
ply. Remove lime coat-
ing. Allow cool-down
of steam cylinder.
Push-back unblocking
pin on thermo switch
with needle-nose pliers
or a screwdriver
•
Capillary tube defec-
tive
•
Replace thermo
switch
•
Thermo switch on
solid state relay has
triggered due to
blocked ventilation
•
Switch off unit. Allow
cool-down of heat sink.
Restart humidifier op-
eration.
121
Water sensor
Water sensor output signal
not plausible
•
Water sensor is
defective
•
Replace water sen-
sor
•
Connecting hoses
blocked
•
Clean hoses
Icons
Code
Error message
Possible cause
Counter measure