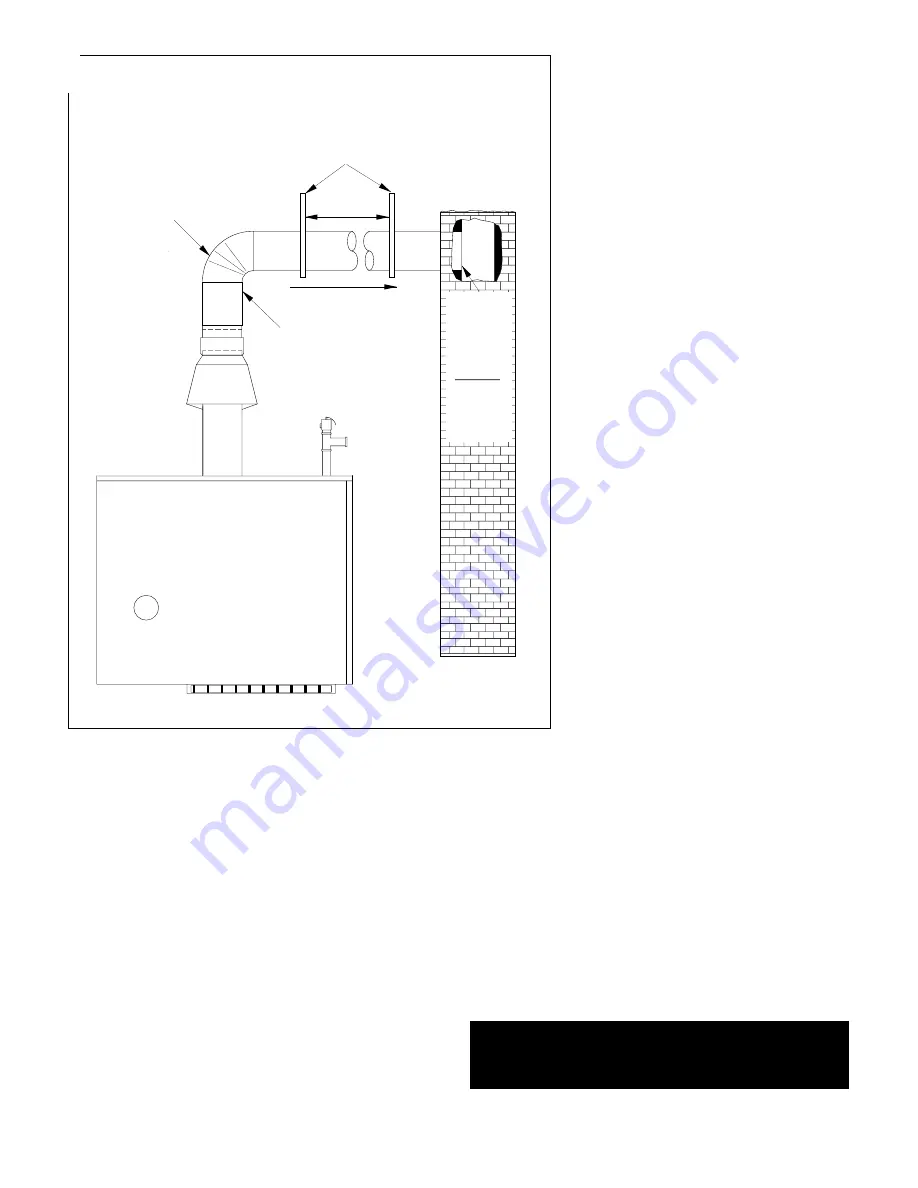
9
ADDITIONAL VENTING REQUIREMENTS: When connecting
to gas vents or chimneys, vent installations shall be in accor-
dance with Part 7, Venting of Equipment, of the National Fuel
Gas Code, ANSI Z223.1-latest edition, or applicable provisions
of the local building codes.
Vent connectors serving appliances vented by natural draft
shall not be connected into any portion of mechanical draft
systems operating under positive pressure.
When two or more appliances vent into a common flue, the
area of the common flue should be at least equal to the area
of the largest flue plus 50% of the areas of the additional flue
or vent connectors.
When an existing boiler is removed from a common venting
system, common venting system is likely to be too large for
proper venting of appliances remaining connected to it. At time
of removal of existing boiler, following steps shall be followed
with each appliance remaining connected to the common vent-
ing system placed in operation, while other appliances remain-
ing connected to common venting system are not in operation:
1. Seal all unused openings in common vent-
ing system.
2. Visually inspect the venting system for
proper size and horizontal pitch and deter-
mine there is no blockage or restriction, leak-
age, corrosion and other deficiencies which
could cause an unsafe condition.
3. Insofar as is practical, close all building
doors and windows and all doors between the
space in which the appliances remaining con-
nected to the common venting system are
located and other spaces of the building. Turn
on clothes dryers and any appliance not con-
nected to the common venting system. Turn
on any exhaust fans, such as range hoods
and bathroom exhausts, so they will operate
at maximum speed. Do not operate a summer
exhaust fan. Close fireplace dampers.
4. Place in operation the appliance being in-
spected. Follow the lighting instructions. Ad-
just thermostat so appliance will operate con-
tinuously.
5. Test for spillage at draft hood relief opening
after 5 minutes of main burner operation. Use
the flame of a match or candle, or smoke
from cigarette, cigar or pipe.
6. After it has been determined that each ap-
pliance remaining connected to common
venting system properly vents when tested as
outlined above, retur n doors, windows,
exhaust fans, fireplace dampers and any
other gas-burning appliance to previous con-
ditions of use.
7. Any improper operation of the common
venting system should be corrected so instal-
lation conforms with the National Fuel Gas
Code, ANSI Z223.1-latest edition. When
resizing any portion of the common venting
system, the common venting system should
be resized to approach the minimum size as
determined using the appropriate tables in Appendix G in the
National Fuel Gas Code, ANSI Z223.1-latest edition. For
Canada, the provisions of CAN/CGA B149.1 or .2 shall apply.
ADDITIONAL CHIMNEY REQUIREMENTS: Chimney condi-
tion is of paramount importance for a safe and efficient boiler
installation. All installations must include a chimney inspection
by a qualified individual or agency. Chimney construction
materials must be compatible with the fuel being used.
Particular attention should be paid on all oil-to-gas conver-
sions. Soot may have accumulated in the chimney and/or
degraded the chimney liner. Most utilities require complete
chimney cleaning. Others may require installation of a new
liner, or other chimney upgrades. Check with local utility for
required safety precautions.
MAXIMUM
6-FT
APART
PITCH 1/4"
PER FOOT
SECURE
FLUE PIPE
TO VENT
DAMPER
USE VENT SUPPORT(S) AS REQUIRED TO PREVENT SAGGING
INSTALL
FLUSH
WITH
INSIDE
CHIMNEY
LINER
SEAL
WITH
FURNACE
CEMENT
SINGLE WALL
OR TYPE B
FLUE PIPE
EW-65 = 5"
EW-85 = 5"
EW-100 = 5"
EW-125 = 6"
EW-145 = 6"
EW-165 = 7"
PROCEDURE C: Install flue pipe between vent damper and
chimney. A 6" minimum clearance is required
between flue pipe and all combustible con-
struction.
FIGURE 1.15
DANGER: A chimney which does not meet modern
safety standards will result in a fire or deadly car-
bon monoxide poisoning of the building residents.
➤
Summary of Contents for EW2-1203
Page 21: ...21...