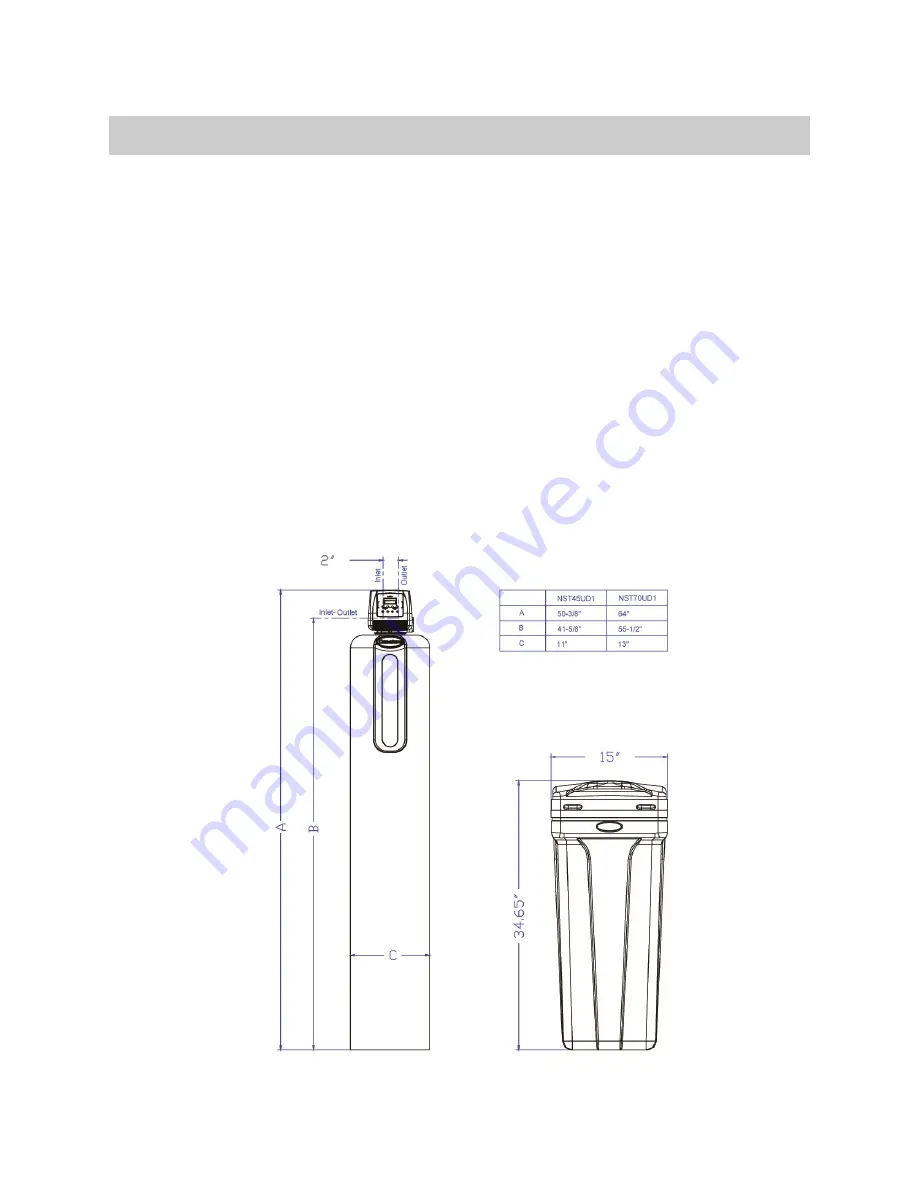
Proper Installation
This water softening system must be properly installed and located in accordance with the
Installation Instructions before it is used.
Do not
install or store where it will not be
exposed to temperatures below freezing or
exposed to any type of weather. Water
freezing in the system will break it. Do not
attempt to treat water over 100°F.
Do not
install in direct sunlight. Excessive
sun or heat may cause distortion or other
damage to non-metallic parts.
Properly ground to conform with all gov-
erning codes and ordinances.
Use only
lead-free solder and flux
for all
sweat-solder connections, as required by
state and federal codes.
Maximum allowable inlet water pressure is
125 psi. If daytime pressure is over 80
psi, night time pressure may exceed the
maximum. Use a pressure reducing valve
to reduce the flow if necessary.
Softener resins may degrade in the pres-
ence of chlorine above 2 ppm. If you
have chlorine in excess of this amount,
you may experience reduced life of the
resin. In these conditions, you may wish
to consider purchasing a whole house car-
bon filter softener system with a chlorine
reducing media.
WARNING:
Discard all unused parts and
packaging material after installation. Small
parts remaining after the installation could
be a choke hazard.
3