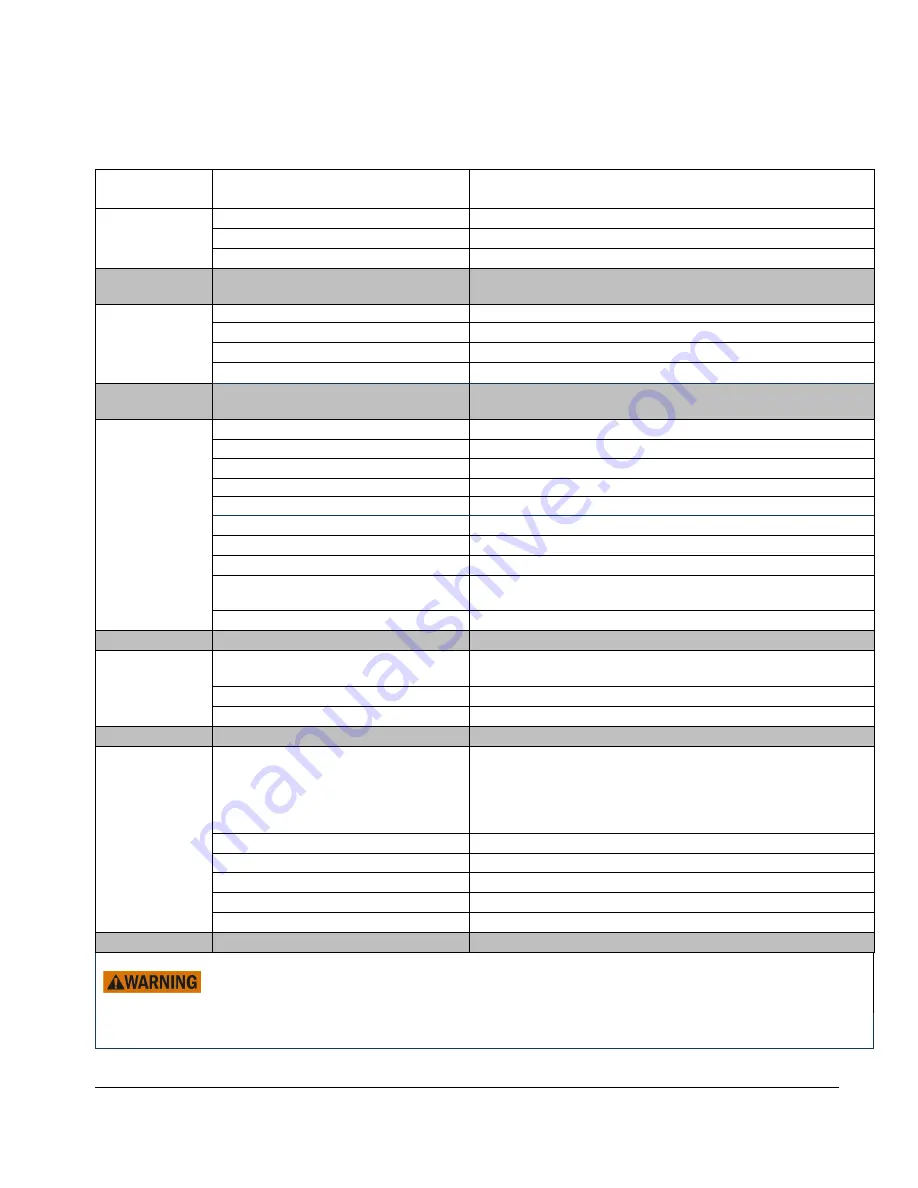
5
Note:
Disconnect the vacuum hose, but leave the solution hose connected to help support the
hoses in the front of the unit. The recovery tank can be removed with the solution hose
attached.
TROUBLESHOOTING – Spot Extractor
Problem
Cause
Solution
Machine not
Building circuit breaker tripped.
Reset breakers or move cords to other outlets
turning on -
Faulty power cord
Replace cord
No power
Faulty switches or internal wiring
Check wiring & test switches - Repair as needed *
Solution Pump
not running
Building circuit breaker tripped.
Reset breakers or move cords to other outlets
Faulty power cord
Replace cord
Faulty switches or internal wiring
Check wiring & test switches - Repair as needed *
Pump faulty
Replace pump
Low Solution
Pressure
and/or
Pulsation
Jets too large for pressure desired
Check jets size & flow rates / use smaller jets
Jets worn allowing too much flow
Replace jets
Hose from solution tank restricted
Repair or replace hose
Pump intake hose or fittings leaking
Repair or replace hose. Tighten clamps or replace fittings
Solution tank empty
Add water to tank
Pump faulty
Repair or replace pump
Tool valve faulty
Repair or replace valve
Quick connects or hoses restricted
Clean out or replace quick connects and/or hoses
Pressure Relief Valve Stuck Open
(Heated Units Only)
Replace the pressure relief valve
Heater Restricted with scale
De-scale or replace the heater
Can't connect
Pressure in lines
Release pressure
solution hose
Quick connects faulty
Replace quick connects (AH101B, AH102B)
to machine
Wrong style/size quick connects
Replace quick connects to match connects on machine
Heater Not
Heating
(Heated Units
Only)
Faulty switches or internal wiring
Check wiring & test switches - Repair as needed *
Temperature Switch tripped
Reset manual reset temperature switch.
Faulty temperature switches
Replace temperature switches on heater
Faulty Heater Core
Replace heater core
Flow too high for proper heating
Use smaller jet or slow use of water
Water Starting out too cold
Heat water before filling tank – Maximum 130°F
: To reduce the risk of fire electrical shock or injury repairs to wiring should only be performed by
experienced service technicians.
*If you are not experienced in checking electrical wiring, contact your nearest authorized service center to perform
tests and repairs to wiring and switches.
Summary of Contents for MA72
Page 9: ...6 ...