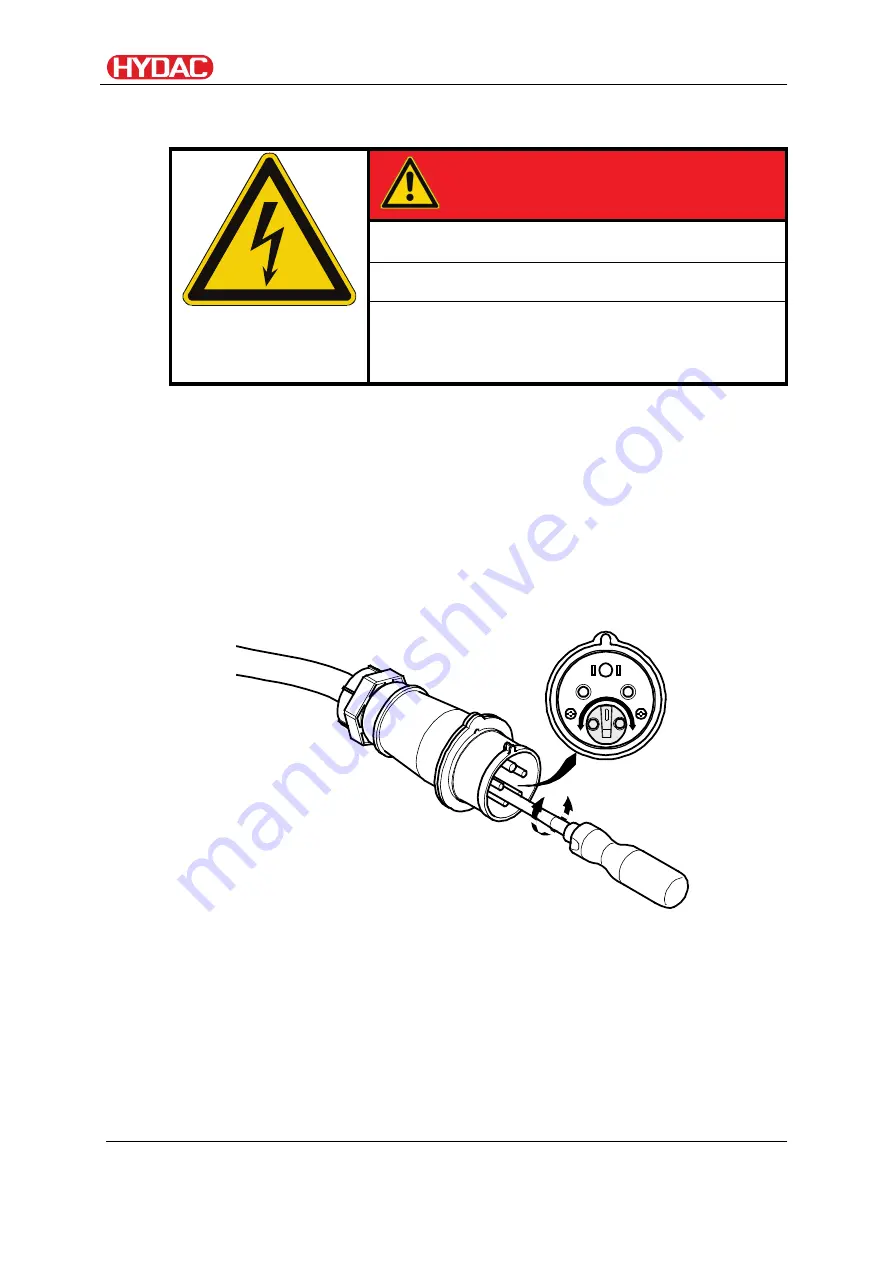
Connecting up unit
Electrical connection of the unit
DANGER
Electric shock
Danger of fatal injury due to electric shock
►
Any work involving the electrical system may
only be done by a properly trained, certified
electrician.
Check that the voltage and frequency information on the power unit type
label coincides with the predominant voltage supply.
Plug the power unit into a properly fused socket for operation.
Switch the pump on and off briefly to check the direction of rotation (jog
mode). In the event of incorrect direction of rotation, reverse the polarity of
two phases. When viewing from the motor-fan side, the direction of rotation
is to the right, in clockwise direction.
The rotating field of the connection socket must be clockwise. If this is not
the case, then the phases can be rotated in the 16A connection plug with the
aid of the phase inverter in the plug.
VMU 1 ATEX II 2G IIC T4
en(us)
Page 34 / 68
BeWa VMU_1_ATEX-II2GIICT4_10000649233 en-us 2017-03-07.doc
2017-03-07