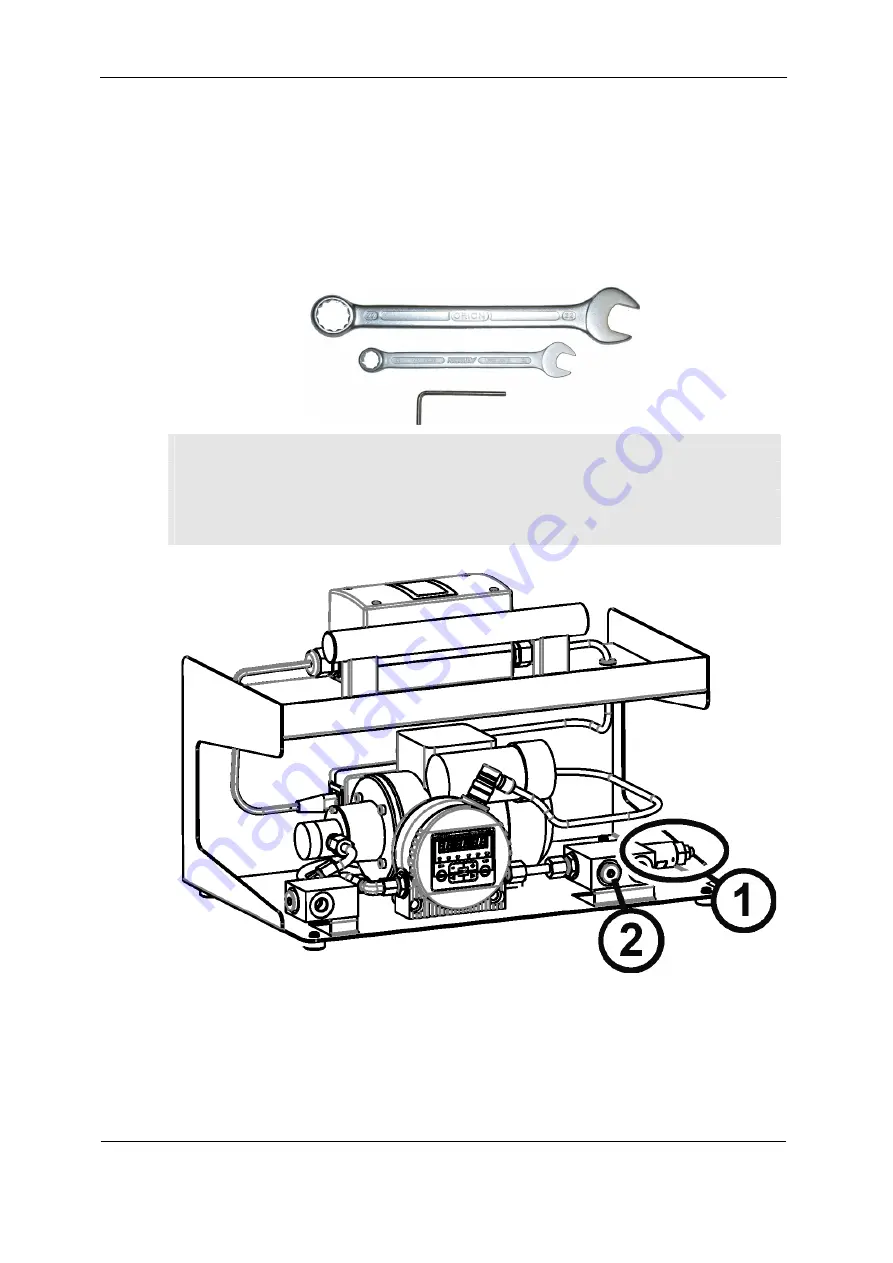
CMP
Adjusting the counter balance valve
Adjusting the counter balance valve
The counter balance valve is set to 8 bar at the time the unit is shipped. Correct this
setting in exceptional cases only.
Required tools and measuring instruments
Combination wrench, size 22 mm
Combination wrench, size 13 mm
Allen wrench, size 4 mm
Allen wrench, size 6 mm
HYDAC FILTER SYSTEMS GMBH
en(us)
Page 25 / 36
BeWa CMP1321 3765034 en 2012-09-25.doc
2012-09-25
Summary of Contents for CMP 1321
Page 35: ...Notes ...