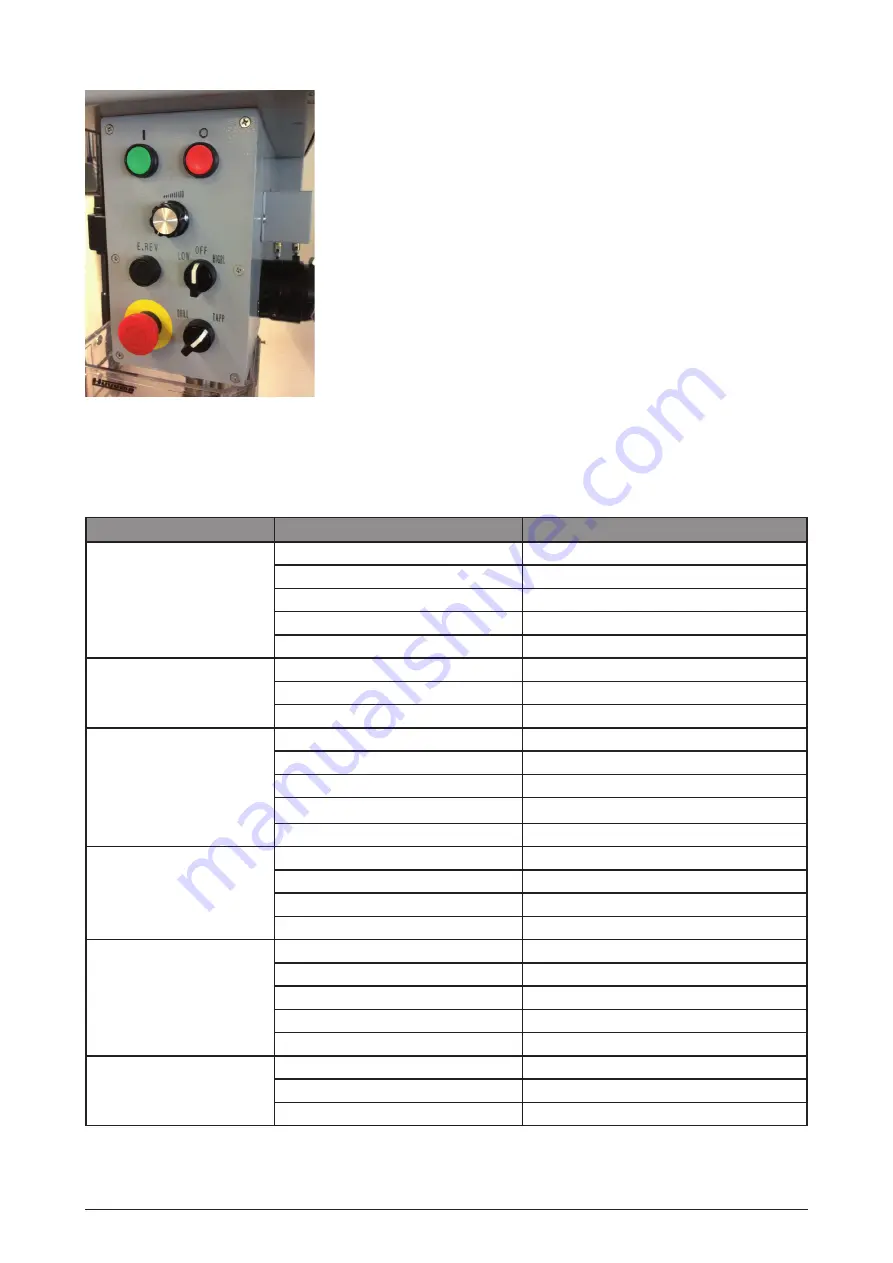
8
CHANGES AND T YPING ERRORS RESERVED
CHANGES AND T YPING ERRORS RESERVED
7.7 Tapping
Tapping can be done as follows:
• Turn the switch for drilling and tapping in the ‘TAPP’ position.
• Set the depth with the depth adjustment on the right-hand side of the
machine (see also 5.2).
• Turn the switch for high or low speed to ‘OFF’.
• Set the speed with the rotary speed knob.
• Move the spindle downwards with the feed handles.
When the set depth is reached, the turning direction of the spindle
automatically reverses and the spindle can be taken out of the tapping
hole.
Always use a low speed for tapping!
7.8 e.reV
buTTon
With this button you can reverse the turning direction of the spindle manually.
8. T
roubleshooTing
Problem
Possible cause
Possible solution
Too much noise
Wrong belt tension
Adjust tension
Spindle not lubricated
Remove spindle quill and lubricate
Pulley loose
Tighten pulley
V-belt loose
Adjust belt tension
Worn bearing
Exchange bearing
Play of the chuck
Drill chuck loose
Tighten by pressing chuck against table
Worn spindle shaft or bearing
Replace spindle shaft or bearing
Worn drill chuck
Replace drill chuck
Motor won't start
Power supply
Check power cord
Motor connections
Check motor connections
Switch connections
Check switch connections
Motor windings burned
Replace motor windings
Switch broken
Replace switch
Drill binds in work piece
Excessive pressure on feed handle
Apply less pressure
V-belt loose
Check belt tension
Drill chuck loose
Tighten drill with key
Speed too high
Adjust speed
Drill burns or smokes
Wrong speed
Check speed table
Chips not discharging
Clean drill
Dull drill
Check sharpness and taper
Needs lubrication
Lubricate during drilling
Wrong feed
Apply less pressure
Table difficult to raise
Needs lubrication
Lubricate with a little oil
Bent rack
Straighten
Clamp bolt locked
Loosen clamp bolt
Figure 9