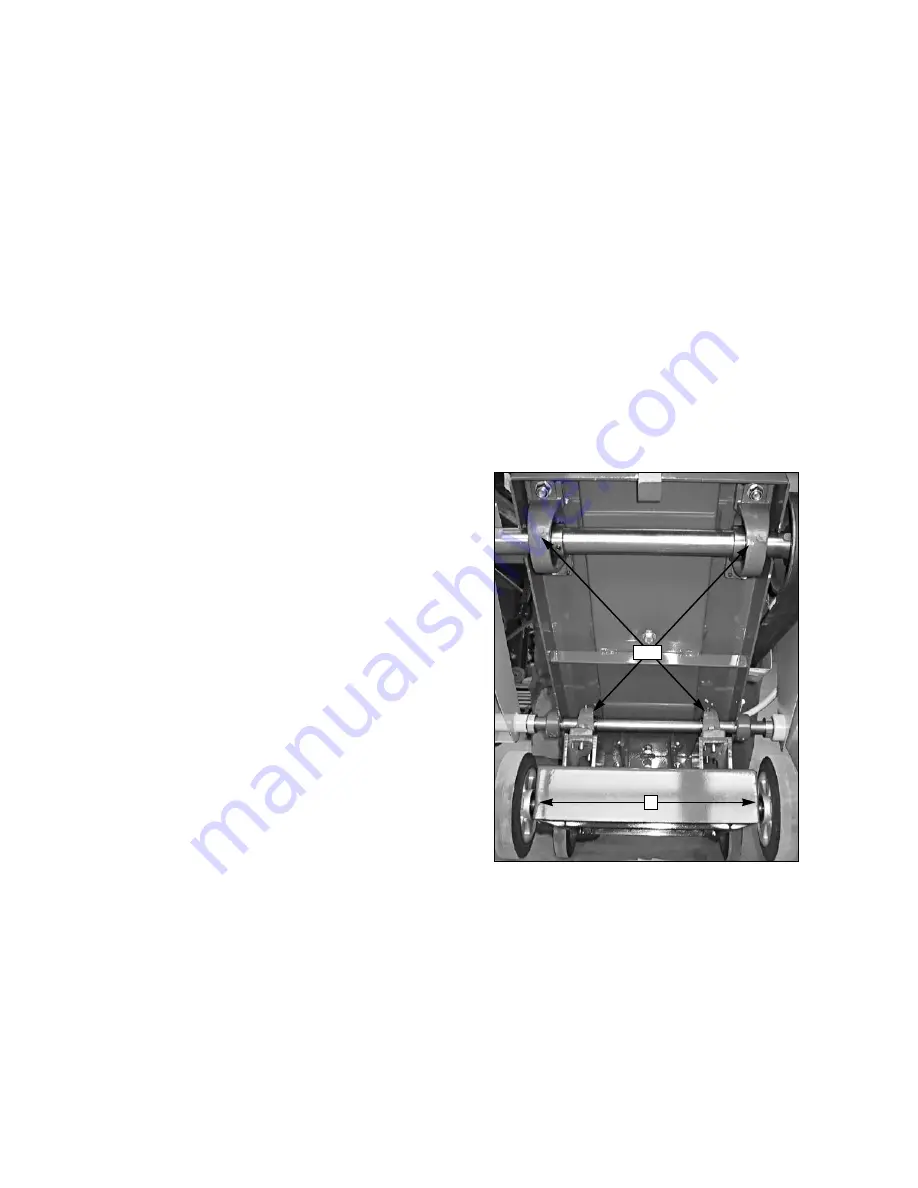
7
•
Check your safety equipment and any protective clothing
you are wearing.
•
Apply the parking brake.
•
If the machine is fitted with a base plate (optional acces-
sory). Lower the base plate by raising the safety catch.
•
Turn on the cooling water to provide adequate cooling
and prevent dust formation.
•
Release the parking brake, while holding the guide hand-
le on the machine with your other hand.
•
Turn the height adjustment wheel clockwise to lower the
blade to a depth that is suitable for the material you are
cutting, but no less than 20 mm.
•
Cut a guide slot at this depth, moving steadily along your
marked line. When you have completed the guide slot,
turn the wheel to raise the blade, turn off the cooling
water and stop the saw by pressing the red switch. Drag
the machine back to the starting point.
•
Realign the floor saw with the guide slot with the aid of
the alignment guide, then start the machine as described
above.
•
Lower the saw blade to a suitable depth. The right cutting
depth depends on the composition of the floor and the
cutting speed. Generally, if the floor saw tries to climb up
out of the slot then the cutting depth is too deep and/or
the cutting speed is too high. The floor saw must not be
advanced so fast that the blade tries to climb out of the
slot. Adjust the cutting depth.
•
Advance the machine smoothly and methodically, making
sure that the alignment guide always follows the guide
slot.
5. Maintenance
NOTE! Always disconnect the power cables before carrying out
any maintenance, repairs or servicing.
•
Clean the machine after completing a series of cuts. Note!
Avoid spraying water at the electric motor and wiring.
•
Lubricate the blade shaft bearing at the end of each day's
use. During intensive cutting the blade shaft must be
lubricated several times a day. Always use high quality
water-resistant grease.
•
Lubricate all other grease points at least once a week, or
more often if necessary. See figures 5.1.1-4 and 5.4.1-2.
Grease the wheel bearings as necessary. See figure 5.1.5.
•
The safety devices are provided for your safety, so it is
extremely important that you check all safety equipment
regularly. If you discover a fault, contact your supplier.
NOTE! Do not start the saw if you know that any of the
machine's safety devices is faulty.
•
Keep the machine's drive belts free of oil, dirt and dust.
Check the belt tension regularly as described below. If the
belts require tensioning, use the adjuster screw in front of
the drive motor. Turn this clockwise to tighten the belts.
See figures 5.2.2 and 5.3.
•
Check the condition of the diamond blade regularly to
make sure it is not damaged or worn down. Replace the
blade when the segments are worn down or have become
narrower than the body of the blade.
•
Check that the water supply is working correctly. If not,
clean the nozzle. See figure 5.2.1.
•
Regularly check that electrical wiring and couplings are in
good condition and that all screws are tight.
Figure 5.1
5.1.1-4 Bearing housing grease points
5.1.5. Wheel bearings
_ _ _ _ _ _ _ _ _ _ _ _ _ _ _ _ _ _ _ _ _ _ _ _ _ _ _ _ _ _ _ _ _ _ _ _ _ _ _ _ _ _ _ _ _ _ _ _ _ _ _ _ _ _ _ _ _ _ _ _ _ _ _ _ _ _ _ _ _ _ _ _ _ _ _ _ _ _ _ _ _ _ _ _ _ _ _ _ _ _ _ _ _ _ _ _ _ _ _ _ _ _ _ _ _ _ _ _ _ _ _ _ _ _ _ _ _ _ _ _ _ _ _ _ _ _ _ _ _ _ _ _ _ _ _ _ _ _ _ _ _ _ _ _ _ _ _ _ _ _ _ _ _ _ _ _ _ _ _ _ _ _ _ _ _ _ _ _ _ _ _ _ _ _ _ _ _ _ _
1 – 4
5