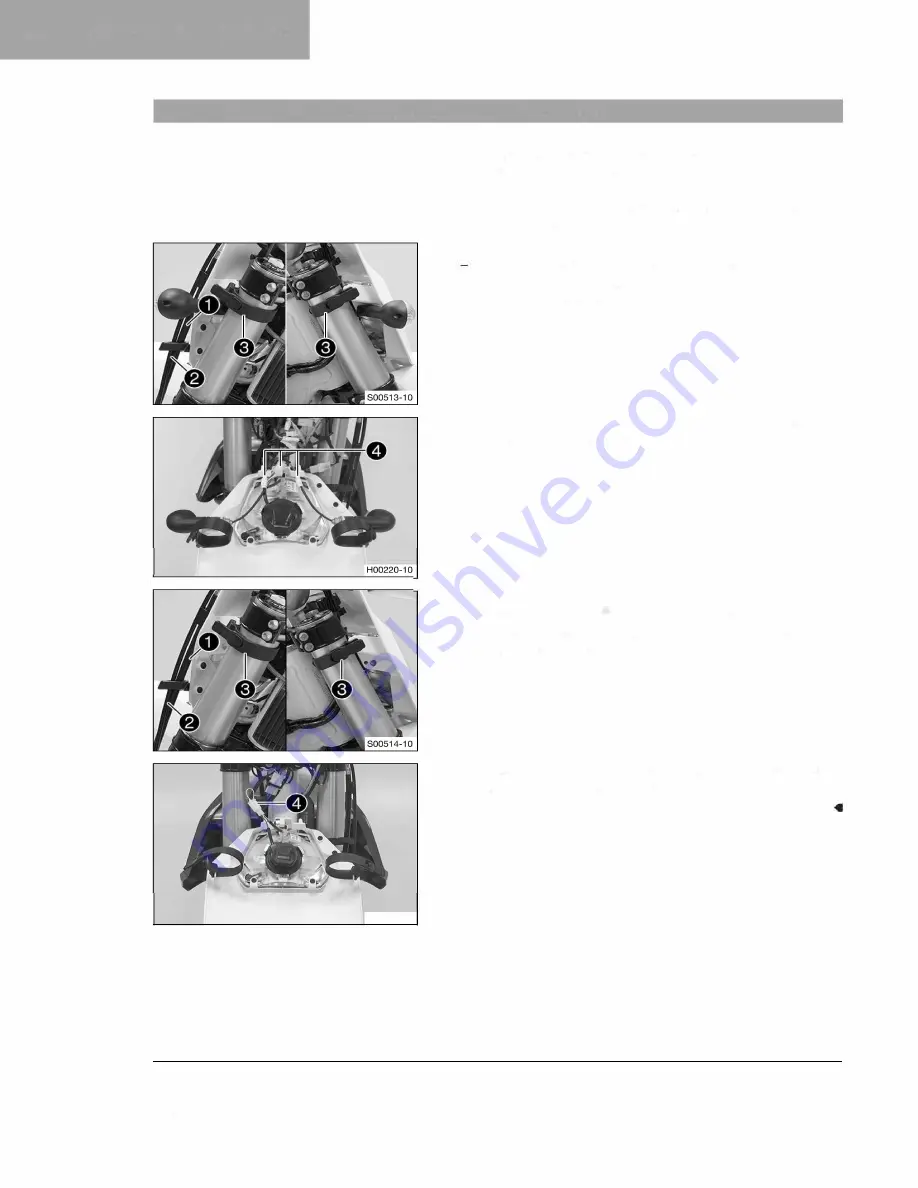
13 MASK, FENDER
13.3
Removing the headlight mask with the headlight
S00893-10
104
(FE EU/AU)
-
Press and hold the kill switch � while the engine is idling
until the engine stops.
(FE US)
-
Press and hold the kill switch � while the engine is idling
until the engine stops.
(FE EU/AU)
Detach brake line
O
and wiring harness f!}.
-
Release rubber bands (D. Slide the headlight mask up
and swing it forward.
-
Detach plug-in connectors
8
and take off the headlight
mask with the headlight.
(FE US)
-
Detach brake line
O
and wiring harness f!}.
-
Release rubber bands (D. Slide the headlight mask up
and swing it forward.
-
Disconnect plug-in connector
8
and take off the head
light mask together with the headlight.