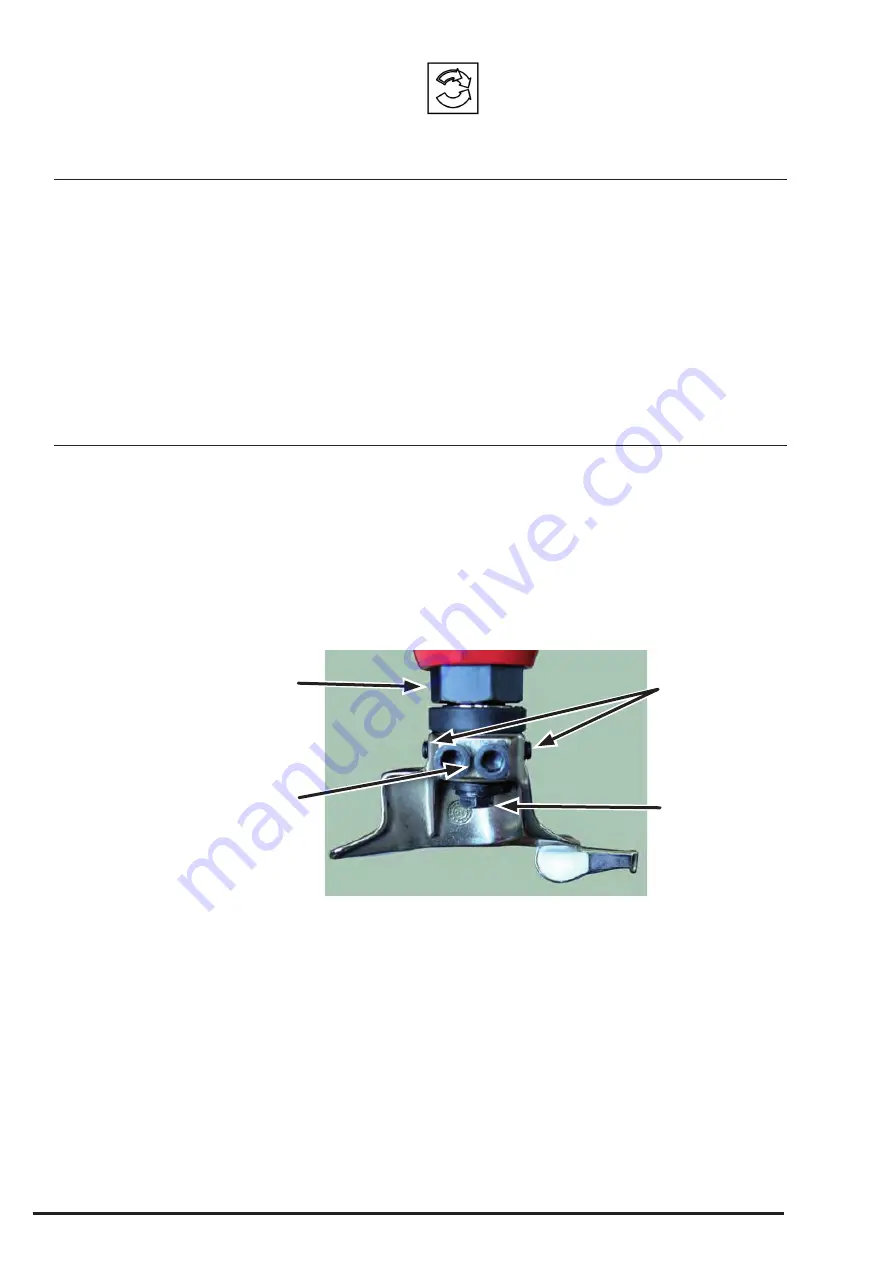
Operation Instructions for TCX56/57 Tire Charger
52
Step down on the wheel rotation pedal
to rotate wheel clockwise until the entire
bead is lifted from the rim.
3.3 Advanced Mounting Procedures
Always use this “checklist” as a guide when mounting tires to ensure proper service.
There are four basic steps when mounting a tire to a rim:
•
Position the bead on top of the rear lip of mount/demount head.
•
Position the bead under the front lip of the mount/demount head.
•
Lock the tire to the rim in the mounting position.
•
Slip the bead into the drop center.
These four basic steps to mounting do not necessarily follow the same sequence, however
all four steps need to be performed to properly mount a tire to a rim.
3.4 Standard Mount/Demount Head Assembly
There are plastic and steel mount/demount head assemblies available for the TCX56 tire
changer family. Both use standard procedures for mounting and demounting.
To change the mount/demount head assembly:
1- Loosen the set screws (steel heads only) and the adjustment bolts.
2- Remove the head retaining bolt.
3- Remove the mount/demount head assembly.
HEX SHAFT
PIN
SET SCREWS
ADJUSTMENT
BOLTS
HEAD
RETAINING
BOLT
4- Place the mount/demount head assembly that you wish to use over the lower section of
the hex shaft and reverse the above procedures to install.
Checking Mount/Demount Head Calibration
For Steel Heads
Calibration will require the use of a 17-18” bare rim.
Set Position of Steel Mount/Demount Head on Hex Shaft
1- Clamp rim without a tire on the tire changer turntable.
2- Loosen the head retaining bolt slightly so that the head is still attached.
3- Loosen the two adjustment bolts and set screws so that the tool head can swivel on the
hex shaft pin.
Summary of Contents for TCX56
Page 2: ......
Page 8: ......
Page 13: ...Operation Instructions for TCX56 57 Tire Charger 13 ...
Page 63: ...Operation Instructions for TCX56 57 Tire Charger 63 5 Glossary 5 1 Rim Diagram ...
Page 64: ...Operation Instructions for TCX56 57 Tire Charger 64 5 2 Illustrations of Various Rim Designs ...
Page 65: ...Operation Instructions for TCX56 57 Tire Charger 65 ...
Page 67: ......