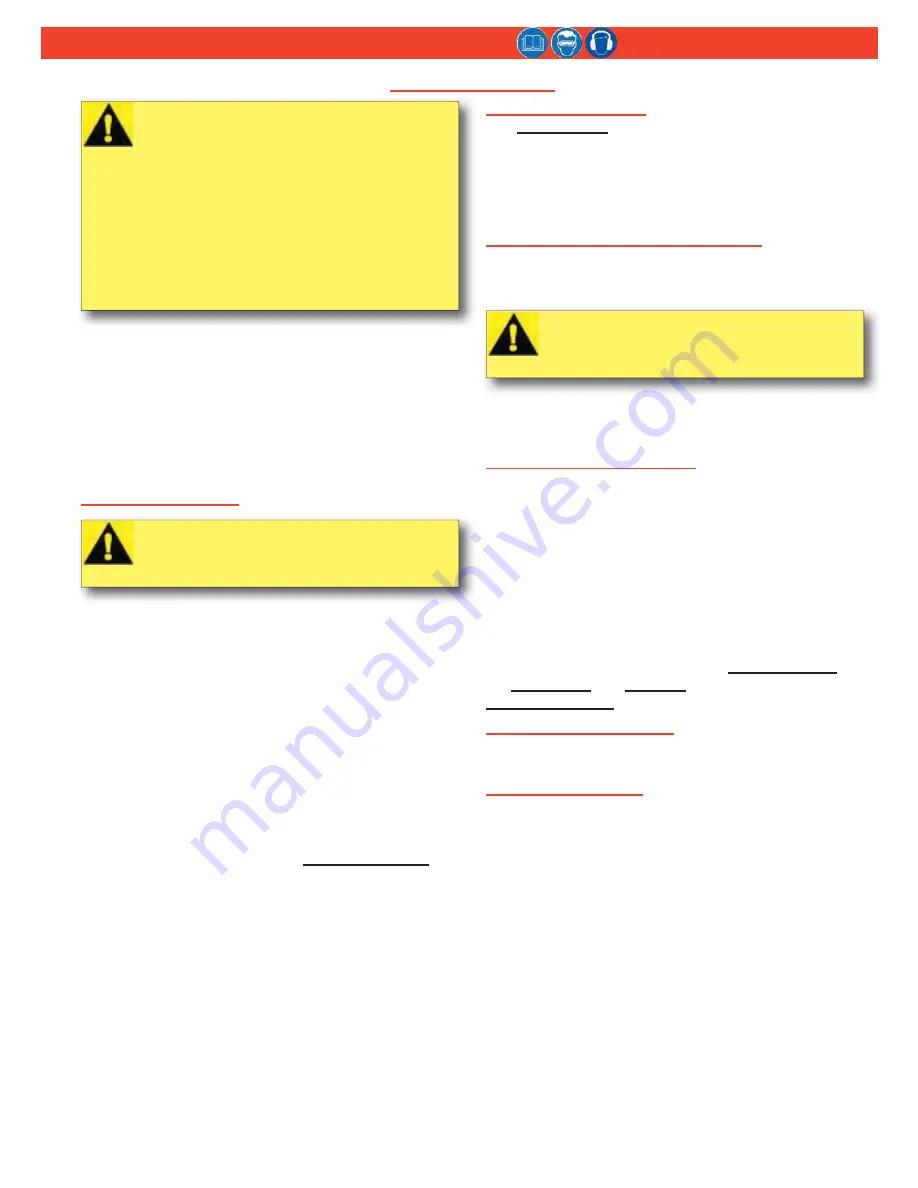
11
2620 Series Hydraulic Installation Tools (
HK1012
)
Alcoa Fastening Systems & Rings
The operating effi ciency of your tool is directly related
to performance of the entire system, including the
tool and nose assembly, hydraulic hoses, control
trigger assembly, and the POWERIG
®
Hydraulic Unit.
Therefore, an effective preventive maintenance program
includes scheduled inspections of the system to detect
and correct minor troubles.
NOTE
:
Where a part number (P/N) is given, Huck
sells that part.
SYSTEM INSPECTION
- Inspect the tool daily. Check hoses, fi ttings, and
couplings for leaks and damage. Clear air-lines of dirt
and water.
- Service the tool in a clean, well-lighted area. Take
special care to prevent contamination of pneumatic
and hydraulic systems.
- Carefully handle all parts and components. Before
reassembly, examine them for damage and wear;
replace when necessary. Replace O-rings and
Back-up rings when the tool is disassembled for any
reason.
- Have available all necessary hand tools (standard and
special); a half-inch brass drift and wood block; an
arbor press; and a soft-jaw vise. Unsuitable hand tools
could cause tool damage. See
K
ITS
& A
CCESSORIES
.
- Follow the disassembly and assembly procedures in
this manual. If Huck recommended procedures are
not followed, the tool could be damaged.
- Disassemble and assemble tool components in a
straight line. Do NOT bend, twist, or apply undue
force.
- Apply continuous steady pressure to disassemble a
component. An arbor press provides steady pressure
to press a component into or out of an assembly.
- Never force a component if it is misaligned. Reverse
the procedure to correct misalignment and start over.
FLUID MAINTENANCE
See
S
PECIFICATIONS
for fl uid type. For fl uid maintenance,
refer to NAS 1638 class 9, ISO CODE 18/15, or SAE
level 6. Dispose of fl uid in accordance with local
environmental regulations. Recycle steel, aluminum, and
plastic parts in accordance with local lawful and safe
practices.
STANDARD SEALANTS, LUBRICANTS
- Apply Parker Threadmate
®
, Loctite
®
567, or Slic-Tite
®
to male pipe threads per manufacturer’s instructions (to
ease assembly and to prevent leaks).
- Smear LUBRIPLATE
®
130-AA or SUPER-O-LUBE
®
on rings and mating parts to ease assembly and to
prevent damaging rings on rough and sharp surfaces.
PREVENTIVE MAINTENANCE
Huck recommends that you:
- Inspect the tool and nose daily for damage and wear.
Inspect the tool before each use for leaks.
- Verify that hoses, fi ttings, and trigger connections are
secure and free of leaks.
- Inspect hydraulic hoses for signs of damage. Replace
if necessary.
- Inspect the tool, hoses, and POWERIG during
operation to detect abnormal heating, leaks, or
vibration.
For supplementary information, see
T
ROUBLESHOOTING
,
the
D
ISASSEMBLY
and
A
SSEMBLY
procedures, and the
A
SSEMBLY
D
RAWINGS
in this manual.
POWERIG MAINTENANCE
Maintenance instructions and repair procedures are in
the appropriate POWERIG Instruction Manual.
TOOL MAINTENANCE
Whenever disassembled, and at regular intervals,
depending on use, replace all O-rings and Back-up
rings. Tool-specifi c Spare Parts Service Kits (P/N
2620KIT
or
2620-PTKIT
) should be kept on hand.
Inspect cylinder bore, piston, piston rod, and unloading
valve for scored surfaces, excessive wear, and damage;
replace as necessary.
M
AINTENANCE
The operating efficiency of your tool is directly related
CAUTIONS:
- Consult the Material Safety Data Sheet
(MSDS) before servicing tool.
- Keep foreign matter out of the hydraulic
system. Keep separated parts away from
dirty work surfaces.
- Dirt and debris in hydraulic fl uid causes
valve failures in tool and POWERIG
®
.
- Check the Assembly Drawings in this
manual for the proper direction of the
fl ats on the dump valve.
Inspect the tool daily Check hoses fittings and
CAUTION: Always replace all seals, wipers,
O-rings, and Back-up rings when the tool is
disassembled for any reason.
continued...
CAUTION: Do NOT use Tefl on
®
tape on pipe
threads. Tape can shred and break free into
fl uid lines, resulting in malfunctions.