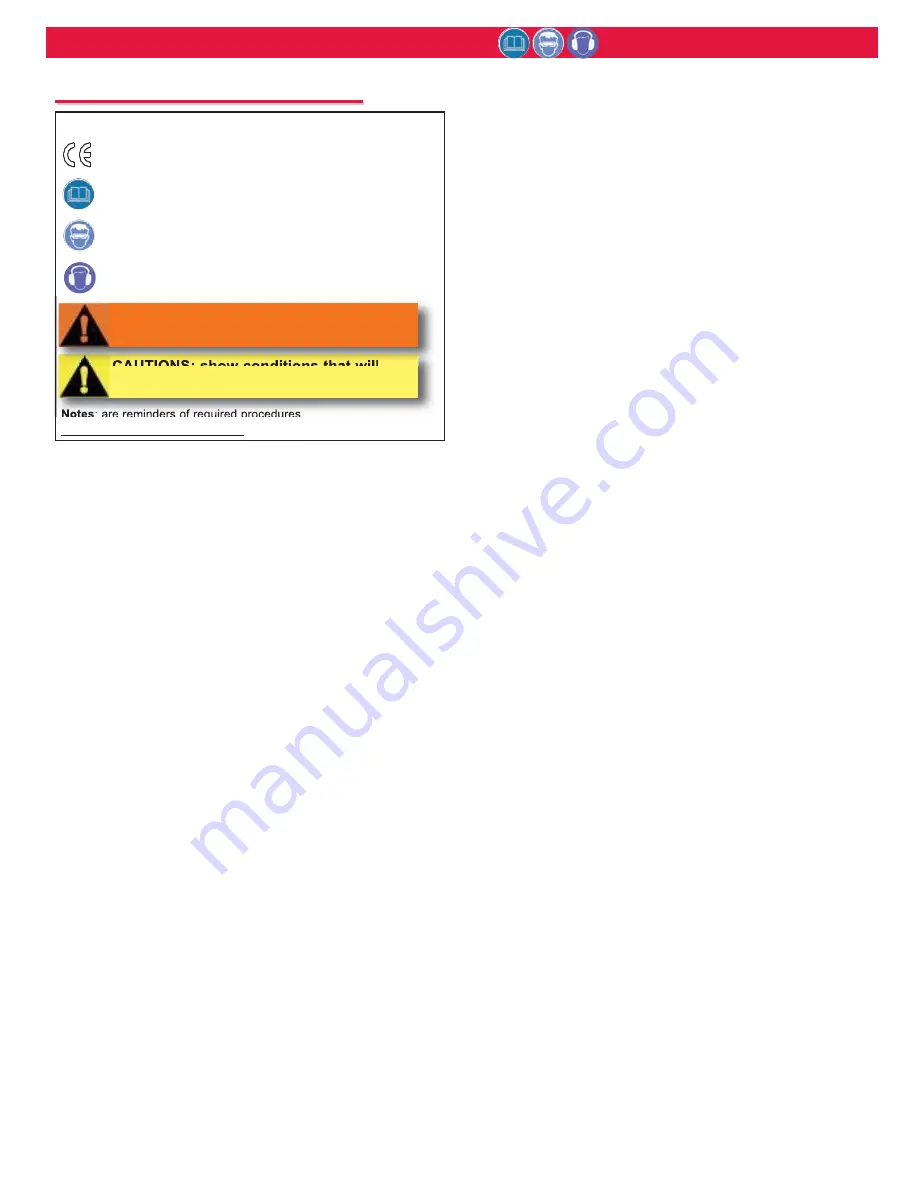
256BT Pneudraulic Installation Tool
(HK1109)
Alcoa Fastening Systems
4
I. GENERAL SAFETY RULES:
1. A half hour long hands-on training session with qualified personnel is
recommended before using Huck equipment.
2. Huck equipment must be maintained in a safe working condition at all
times. Tools and hoses should be inspected at the beginning of each
shift/day for damage or wear. Any repair should be done by a qualified
repairman trained on Huck procedures.
3. For multiple hazards, read and understand the safety instructions before
installing, operating, repairing, maintaining, changing accessories on, or
working near the assembly power tool. Failure to do so can result in
serious bodily injury.
4. Only qualified and trained operators should install, adjust or use the
assembly power tool.
5. Do not modify this assembly power tool. This can reduce effectiveness of
safety measures and increase operator risk.
6. Do not discard safety instructions; give them to the operator.
7. Do not use assembly power tool if it has been damaged.
8. Tools shall be inspected periodically to verify all ratings and markings
required, and listed in the manual, are legibly marked on the tool. The
employer/operator shall contact the manufacturer to obtain replacement
marking labels when necessary. Refer to assembly drawing and parts list
for replacement.
9. Tool is only to be used as stated in this manual. Any other use is
prohibited.
10. Read MSDS Specifications before servicing the tool. MSDS
specifications are available from the product manufacturer or your Huck
representative.
11.Only genuine Huck parts shall be used for replacements or spares. Use of
any other parts can result in tooling damage or personal injury.
12.Never remove any safety guards or pintail deflectors.
13.Never install a fastener in free air. Personal injury from fastener ejecting
may occur.
14.Where applicable, always clear spent pintail out of nose assembly before
installing the next fastener.
15.Check clearance between trigger and work piece to ensure there is no
pinch point when tool is activated. Remote triggers are available for
hydraulic tooling if pinch point is unavoidable.
16.Do not abuse tool by dropping or using it as a hammer. Never use
hydraulic or air lines as a handle or to bend or pry the tool. Reasonable
care of installation tools by operators is an important factor in maintaining
tool efficiency, eliminating downtime, and preventing an accident which
may cause severe personal injury.
17.Never place hands between nose assembly and work piece. Keep hands
clear from front of tool.
18.Tools with ejector rods should never be cycled with out nose assembly
installed.
19.When two piece lock bolts are being used always make sure the collar
orientation is correct. See fastener data sheet for correct positioning.
II. PROJECTILE HAZARDS:
1. Risk of whipping compressed air hose if tool is pneudraulic or pneumatic.
2. Disconnect the assembly power tool from energy source when changing
inserted tools or accessories.
3. Be aware that failure of the workpiece, accessories, or the inserted tool
itself can generate high velocity projectiles.
4. Always wear impact resistant eye protection during tool operation. The
grade of protection required should be assessed for each use.
5. The risk of others should also be assessed at this time.
6. Ensure that the workpiece is securely fixed.
7. Check that the means of protection from ejection of fastener or pintail is in
place and operative.
8. There is possibility of forcible ejection of pintails or spent mandrels from
front of tool.
III. OPERATING HAZARDS:
1. Use of tool can expose the operator’s hands to hazards including:
crushing, impacts, cuts, abrasions and heat. Wear suitable gloves to
protect hands.
2. Operators and maintenance personnel shall be physically able to handle
the bulk, weight and power of the tool.
3. Hold the tool correctly and be ready to counteract normal or sudden
movements with both hands available.
4. Maintain a balanced body position and secure footing.
5. Release trigger or stop start device in case of interruption of energy
supply.
6. Use only fluids and lubricants recommended by the manufacturer.
7. Avoid unsuitable postures, as it is likely for these not to allow
counteracting of normal or unexpected tool movement.
8. If the assembly power tool is fixed to a suspension device, make sure that
fixation is secure.
9. Beware of the risk of crushing or pinching if nose equipment is not fitted.
IV. REPETITIVE MOTION HAZARDS:
1. When using assembly power tool, the operator can experience discomfort
in the hands, arms, shoulders, neck or other parts of the body.
2. When using tool, the operator should adopt a comfortable posture while
maintaining a secure footing and avoid awkward or off balanced postures.
3. The operator should change posture during extended tasks to help avoid
discomfort and fatigue.
4. If the operator experiences symptoms such as persistent or recurring
discomfort, pain, throbbing, aching, tingling, numbness, burning
sensations or stiffness, these warnings should not be ignored. The
operator should tell the employer and consult a qualified health
professional.
V. ACCESSORIES HAZARDS:
1. Disconnect tool from energy supply before changing inserted tool or
accessory.
2. Use only sizes and types of accessories and consumables that are
recommended. Do not use other types or sizes of accessories or
consumables.
VI. WORKPLACE HAZARDS:
1. Be aware of slippery surfaces caused by use of the tool and of trip hazards
caused by the air line or hydraulic hose.
2. Proceed with caution while in unfamiliar surroundings; there could be
hidden hazards such as electricity or other utility lines.
3. The assembly power tool is not intended for use in potentially explosive
environments.
4. Tool is not insulated against contact with electrical power.
5. Ensure there are no electrical cables, gas pipes, etc., which can cause a
hazard if damaged by use of the tool.
VII. NOISE HAZARDS:
1. Exposure to high noise levels can cause permanent, disabling hearing
loss and other problems such as tinnitus, therefore risk assessment and
the implementation of proper controls is essential.
2. Appropriate controls to reduce the risk may include actions such as
damping materials to prevent workpiece from ‘ringing’.
3. Use hearing protection in accordance with employer’s instructions and as
required by occupational health and safety regulations.
4. Operate and maintain tool as recommended in the instruction handbook
to prevent an unnecessary increase in the noise level.
5. Select, maintain and replace the consumable / inserted tool as
recommended to prevent an unnecessary increase in noise.
6. If the power tool has a silencer, always ensure that it is in place and in
good working order when the tool is being operated.
VIII. VIBRATION HAZARDS:
1. Exposure to vibration can cause disabling damage to the nerves and
blood supply to the hands and arms.
2. Wear warm clothing when working in cold conditions and keep hands
warm and dry.
3. If numbness, tingling, pain or whitening of the skin in the fingers or hands,
stop using the tool, tell your employer and consult a physician.
4. Support the weight of the tool in a stand, tensioner or balancer in order to
have a lighter grip on the tool.
IX. PNEUMATIC / PNEUDRAULIC TOOL SAFETY INSTRUCTIONS:
1. Air under pressure can cause severe injury.
2. Always shut off air supply, drain hose of air pressure and disconnect tool
from air supply when not in use, before changing accessories or when
making repairs.
3. Never direct air at yourself or anyone else.
4. Whipping hoses can cause severe injury, always check for damaged or
loose hoses and fittings.
5. Cold air should be directed away from hands.
6. Whenever universal twist couplings (claw couplings) are used, lock pins
shall be installed and whipcheck safety cables shall be used to safeguard
against possible hose to hose or hose to tool connection failure.
7. Do not exceed maximum air pressure stated on tool.
8. Never carry an air tool by the hose.
GLOSSARY OF TERMS AND SYMBOLS:
-
Product complies with requirements set forth by the
relevant European directives.
-
READ MANUAL
prior to using this equipment.
-
EYE PROTECTION IS REQUIRED
while using this
equipment.
-
HEARING PROTECTION IS REQUIRED
while using this
equipment.
Notes
: are reminders of required procedures.
Bold, Italic type and underlining
:
emphasizes a specific instruction.
S
S
AFETY
AFETY
I
I
NSTRUCTIONS
NSTRUCTIONS
CAUTIONS: show conditions that will
damage equipment and or structure.
WARNINGS: Must be understood to avoid
severe personal injury.