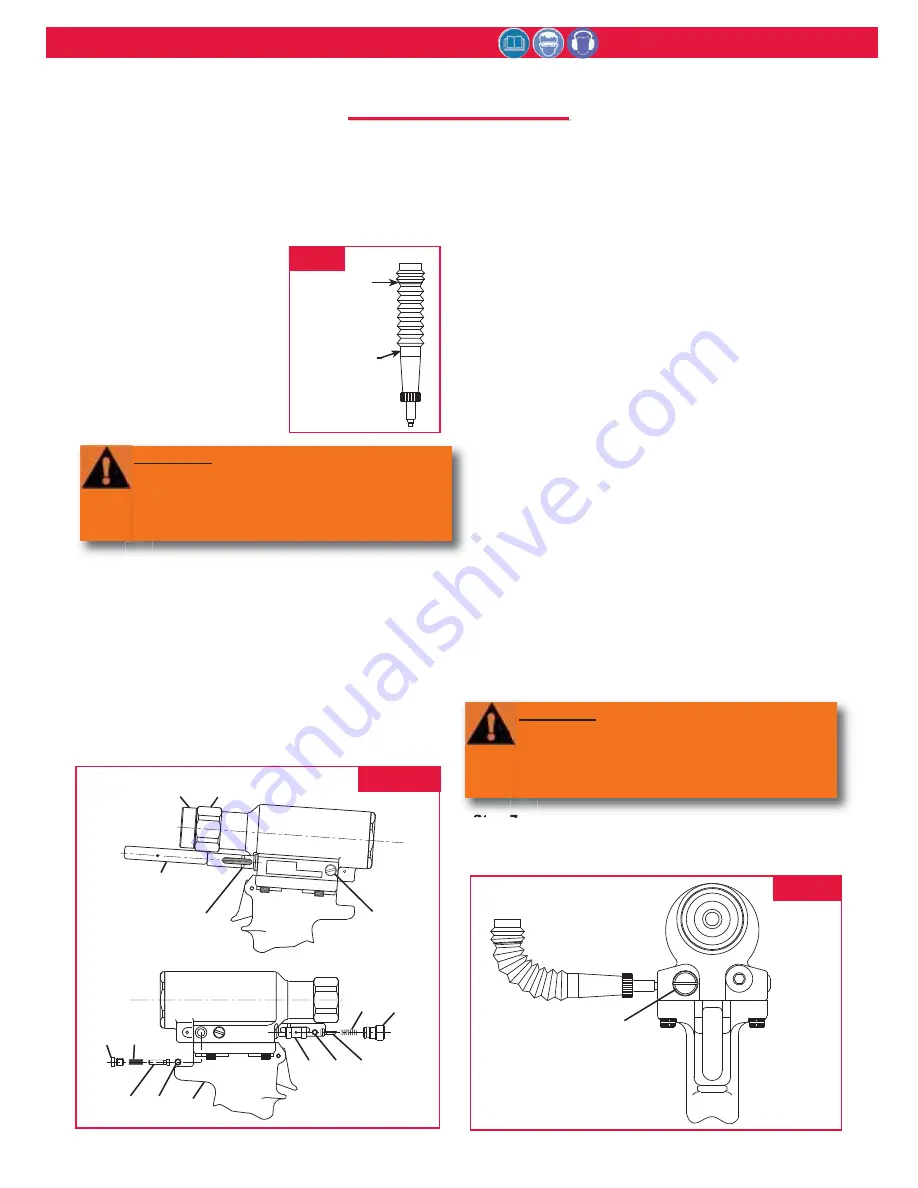
256BT Pneudraulic Installation Tool
(HK1109)
Alcoa Fastening Systems
12
Equipment Required:
- Shop airline with 90 - 100 psi max.
- Air regulator
- Fill bottle, 120337, (supplied with tool).
- Large flat blade screwdriver
- Optional Stall Nut 120824
- Nose assembly
- Fasteners (Optional)
Preparation:
1. Install air regulator in
airline and set pressure to
20-40 psi.
2. Fill bleed bottle almost full
of DEXRON III - ATF or
equivalent. (Fig.6)
Refill tool only when red line on plunger drops below the
red line on the reservoir housing or when tool is rebuilt.
USE: AUTOMATIC TRANSMISSION FLUID DEXRON
III, OR EQUIVALENT.
Step 1
Screw Fill Tool into Reservoir Plunger, pull Plunger into
Housing and lock Fill Tool in full forward position by
tilting handle (long side touching tool) and locking in
place. (Fig. 7)
Step 2
Remove Plugs (57) and (50) and all guides, springs and
balls from ports in head. Reinstall Plug (57) in head in
Relief Valve port (front of tool). (Fig. 7 & 8).
Step 3
Screw retaining nut onto head assembly. Screw Stall
Nut (optional see note:) onto Piston and tighten to
ensure full thread engagement. Back off retaining nut
until it engages stall nut. Check Piston location. Piston
must be all the way forward and locked with stall nut
and retaining nut.
Note:
If Stall Nut is not used, piston
must be pushed to the full forward position before
installing valves.
Step 4
Attach the tool air source momentarily to seat air piston
at bottom of cylinder. Disconnect tool. With fill port
facing up, (check valve on side) lay tool on its side.
Step 5
Install fill bottle in head fill port (check valve hole).
(Fig. 7 & 8)
Step 6
Connect tool to shop air regulated to 20 to 40 psi. Cycle
tool 20-30 times. Watch for air bubbles escaping from
the tool into bottle. (You may rock the tool to free
trapped air in the tool.) Do not allow the air to re-enter
the tool.
Step 7
When air bubbles no longer appear in bottle, remove fill
bottle while tool is lying on its side.
Stall Nut
120824
8
HUCK
U.S. PAT. 4597263
256/257
57
56
54
53
55
50
44 43
45
1
Fill Tool
Red Line
Indicator
33
FIG. 7
FILL
POINT
120337
Fill Bottle
Assembly
FIG. 6
57
FIG. 8
WARNING: Avoid contact with hydraulic
fluid. Hydraulic fluid must be disposed of
in accordance with Federal, State and Local
Regulations. Please see MSDS for
Hydraulic fluid shipped with tool.
WARNING: Air pressure MUST be set to 20
to 40 psi to prevent possible injury from
high pressure spray. If plug (50) is
removed, fill bottle must be in place before
cycling tool.
F
F
ILL
ILL
AND
AND
B
B
LEED
LEED