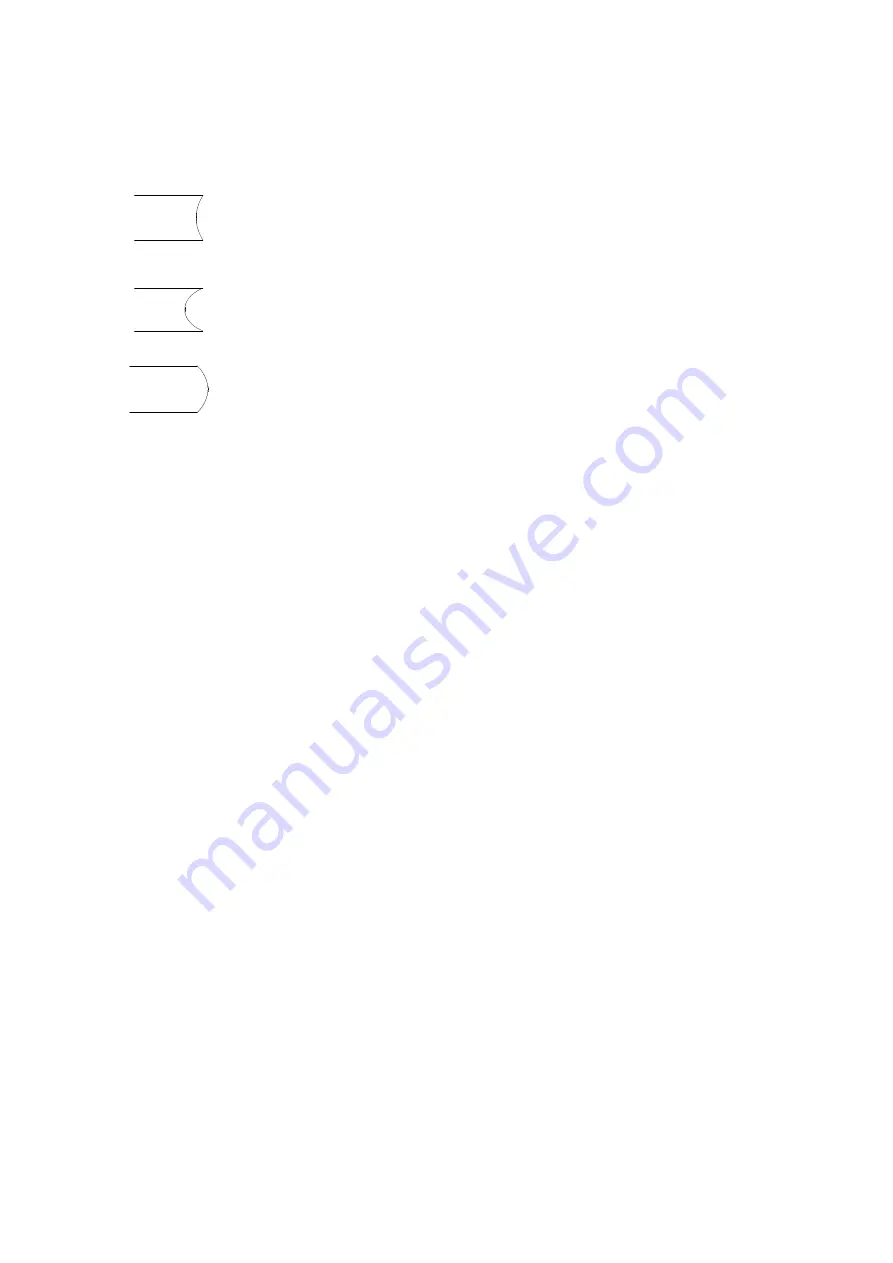
- 28 -
Consumables damage may cause continuous slag
5
、
Cutting surface straightness
Cutting surface dimple or convex require the torch height correct to get
cutting surface flat
If the distance from torch to workpiece too short, there will be dimple at the
surface, enlarge the arc voltage need enlarge the distance from torch to
workpiece to get better surface.
When the distance from workpiece to torch too far or cutting current too big,
there will be convex at the surface. Then need to lower the arc voltage and
cutting current. If can;t change the cutting current, then need to use smaller
consumables
6
、
Other improvement
⑴
piercing
The piercing delay time need be enough so that can penetrate the material, but if delay
too long the arc can;t find the edge of the hole. The time need delay if the consumables loss.
The piercing delay time is got according to the consumable average delay time.
Piercing finish signal can keep high shield prefow pressure to protect the consumables.
For some special situation, when piercing diameter near to the max.thickness, need
consider the following:
a) The leading distance should be same with the material thickness, means 20mm
material need 20mm leading distance
b) To avoid the slag damage the protection cap, need to clean the slag before put
down the torch
c) Different material may affect the piercing capacity, especially the high strength,
high Mn or Gi steel, the piercing capacity will be low.
d) If machine is difficult to piercing some material or some thickness, increase the
shield gas preflow can help, the disadvantage is lower the arc strike success ratio
e) Adopt fly piercing (without leading)may increase the piercing capacity under some
situation.but this may cause damage to the torch or other parts, which not suggest
Summary of Contents for POWERCUT105
Page 22: ...18 Ratio Connection Ratio Connection 1 50 1 40 1 30 1 21 1 1 20 1 1...
Page 41: ...37 3 Circuit Diagram...
Page 42: ...38...