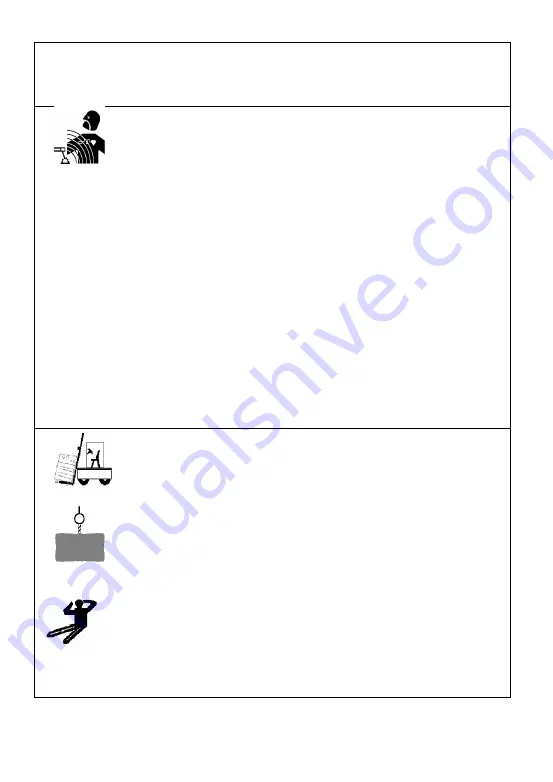
不要将手放置在风扇附近,不要在设备运行时拨动刹车柄。
为了避免设备在维护时被意外启动,维护前应除去引擎与焊接设备的连线。
8
电磁场
:焊接电流流经的任何场合都会产生电磁场,焊接设
备本身也会有电磁辐射。
电磁场对心脏起搏器有影响,安装有心脏起搏器的用户,
须咨询自己的医生。
电磁场对健康的影响未经证实和查明,不排除对身体有负面影响。
焊接施工人员应按如下方法减少电磁场对人体的危害:
1.
将焊接和接工件的电缆捆扎在一起。
2.
切勿将电缆环绕身体的全部或局部。
3.
不要置身于焊接电缆和接地(工件)电缆中间,如果焊接电缆在左边,
则接地电缆也应在左边。
4.
接地和焊接电缆应尽量地短。
5.
不要在焊接电源附近施工。
9
提升装置
:华远焊机的供货状态为纸箱或木箱包装,设备到
达用户现场后,在其包装物上并没有提升装置,
用户可以采用升降叉车将其运输到位,
然后拆箱。
当焊机设置有提升吊环时,可以利用吊环进行场内搬运,
华远焊机提醒用户,焊机提升对焊机有潜在的危险,除
非特殊情况,一般的搬运应使用其滚轮推动焊机移位。
起吊时应保证焊机所有附件已经拆除。
当焊机起吊时,应保证焊机下方没有人员驻留,并随时提
醒过路行人。
严禁吊车快速移动。
焊机安装到位后应按使用说明书的相关章节由专业人员认真安装焊机。
Summary of Contents for LGK-240P
Page 1: ...LGK 240P INVERTER AIR PLASMA CUTTING MACHINE...
Page 2: ...1 2 3 IP21S 4 5 A...
Page 3: ...1...
Page 4: ...2 3 4...
Page 5: ...5 6 7...
Page 6: ...8 1 2 3 4 5 9...
Page 7: ...10 80...
Page 8: ...1 4 4 4 5 7 8 8 9 11 12 12 13 14 1 15...
Page 9: ...1...
Page 10: ...2 60 10 6 4...
Page 11: ...3 1 2 20 90 40 50 3 10 40 4 5 30cm 30cm 6 1000m...
Page 12: ...4 L G K 2 40 P 40A 220V IGBT GB T 15579 1 2013 GB T8118 2010...
Page 14: ...6 2...
Page 15: ...7 IGBT 40KHz PWM IGBT AC AC DC PI IGBT AC DC...
Page 16: ...8 1 2 3 4 5 6 7 8 9 AC220 10 1 2 4 5 6 7 8 9 10 3...
Page 17: ...9 1 2 3 4 1 2 3 4 IP21S 5 15 1...
Page 18: ...10 6 6mm2 7 6mm2 8 9...
Page 19: ...11 10 1 2 3 220VAC 220VAC...
Page 20: ...12 6...
Page 21: ...13 1 1 2 1 2 2 1 2 3 1 2 3 3 1 1 4 1 2 3 4 5 1 2 3 4 5 5 1 2 1 2...
Page 22: ...14 1 1 2 1 3 1 4 1...
Page 23: ...15 1...
Page 24: ...LGK 240P INVERTER AIR PLASMA CUTTING MACHINE...
Page 38: ...6 2 Cutting capacity Technical specifications...
Page 48: ...16 Electric Diagram...
Page 49: ...17...