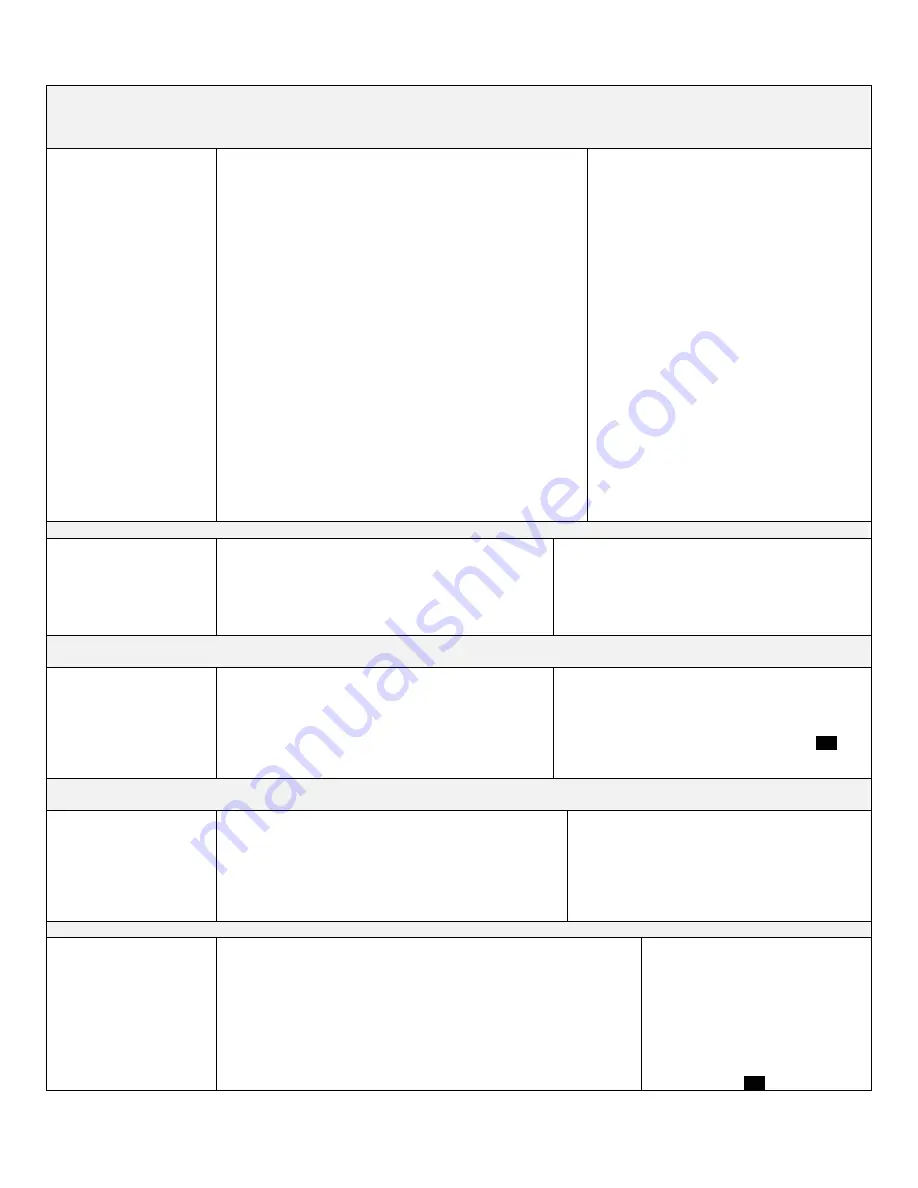
64
LP- 428 REV. 9.2.14
Fault Code F01
FLUE TEMP/WAT LV F01
PUMP ON
This code indicates that one of the safety interlock switches
present in the unit has tripped. There are several interlock
switches that could possibly trip and cause this error. The
following four switches are installed in each boiler of the MODCON
1000 or MODCON 1700 unit and are standard equipment in all
boilers.
1.
Flue ECO
– Trips if the flue temperature is excessive. This
switch has to be manually reset.
2.
Boiler module thermal fuse
– Trips if there is excessive heat
on the rear of the heat exchanger.
3.
Boiler module front temperature limit switch - Trips if there is
excessive heat on the front of the heat exchanger.
4.
Blocked vent pressure switch (BVPS)
– This switch trips if
there is excessive pressure in the flue and automatically
resets.
The following switches are optional equipment that may be
installed on MODCON 1000 and MODCON 1700 units. These
devices have indicator lights on them showing of they are tripped.
1.
High gas pressure switch
– This switch trips if there is
excessive gas pressure on the outlet side of the gas valve
and must be manually reset.
2.
Low gas pressure switch
– This switch trips if there is low gas
pressure on the inlet side of the gas valve and must be
manually reset.
3.
UL 353 Low Water Cutoff
– This device trips if the water level
in the boiler is low and must be manually reset.
1.
Check to see if the boiler with the F01 code
displayed has any of the optional switches
installed.
2.
If so, check to see if the indicator light on any
of the devices is showing that they are
tripped.
3.
If an indicator light is illuminated, investigate
the source of the error for that particular
switch.
4.
If there are no optional switches or none of
the indicator lights is illuminated on the
optional switches then use an ohmmeter to
test each of the standard switches one at a
time. Turn the power off to the boiler and
disconnect the switch to be tested from the
boiler to determine which one has tripped.
When you find the tripped switch investigate
the cause of the fault based on the purpose
of the switch. NOTE: The common reasons
for the temperature switches to trip are a) low
water flow through the boiler, or b) poor heat
transfer from the water to the load.
5.
If no switches are tripped, push RESET on
the boiler. If the boiler tries to ignite or ignites
and only runs for a short time and the F01
code returns, investigate the flue for
blockage.
Fault Code F02
SUPPLY SENSOR F02
PUMP ON
Indicates that the supply temperature sensor of the boiler
has failed. This is a serious safety issue and the boiler will
not restart until the sensor is replaced by a technician and
he pushes the RESET button on the display. This situation
is indicated by the red light on the display and the flashing
word LOCKOUT. During this lockout fault, the pump will be
on as indicated on the second line of the display.
1. Check the electrical connection to the thermistor on
the outlet manifold. Verify 5 VDC by checking in Molex
connector. If there is no 5 VDC, check the harness. If
harness is OK, replace control. NOTE: The boiler will
reset automatically. Verify thermistor values by
referencing chart in this manual.
2. Replace thermistor if necessary.
Fault Code F03
RETURN SENSOR F03
PUMP ON
This display indicates that the return temperature sensor of
the boiler has failed. This code indicates a serious safety
issue and the boiler will not restart until the sensor is
replaced by a technician and he pushes the RESET button
on the display. This situation is indicated by the red light on
the display and the word LOCKOUT flashing on the display.
During this lockout fault, the pump will be on as indicated on
the second line of the display.
1. Check circulator pump operation.
2. Assure that there is adequate flow through the boiler
by accessing the status menu and assuring that there is
less than a 50°F rise from the return thermistor to the
supply thermistor.
3. Troubleshoot thermistor by following steps in
F02
.
Fault Code F04
FLUE SENSOR F04
PUMP ON
This display indicates that the flue temperature sensor of the
boiler has failed. This is a serious safety issue. The boiler will
not restart until the sensor is replaced by a technician and he
pushes the RESET button on the display. This situation is
indicated by the red light and the flashing word LOCKOUT on
the display. During this lockout fault, the pump will be on as
indicated on the second line of the display.
Inspect the flue sensor for physical damage or
corrosion and replace it if necessary. Check the
electrical connection to the flue sensor and repair as
necessary. Measure the resistance of the sensor and
refer to the Supply Temperature Sensor chart in
Figure 29 of this manual. The temperature on the
chart should be close to the same as the temperature
in the flue. If not, replace the flue sensor.
Fault Code F05
SUPPLY TEMP HIGH F05
PUMP ON
This display indicates that the supply temperature of the boiler is excessive.
If accompanied by the red FAULT light and LOCKOUT flashing on the
display, this code indicates that the temperature on the supply sensor has
exceeded 230
o
F and a serious safety issue exists. The boiler will not restart
until the cause of the excessive temperature is repaired by a technician and
the RESET button is pushed on the display.
If the FAULT light is not illuminated and this message is displayed, then the
supply temperature of the boiler is at or above 210
o
F. The message will clear
automatically when the temperature drops below 194
o
F. During the time that
this message or lockout fault is displayed, the pump will be on as indicated
on the second line.
1.
Check circulator pump operation.
2. Assure that there is adequate flow
through the boiler by accessing the
status menu and assuring that there is
less than a 50°F rise from the return
thermistor to the supply thermistor.
3. Check the direction of flow off the
boiler circulator. (See Piping Details in
this manual.)
4. Troubleshoot the thermistor by
following steps in
F02
.
Summary of Contents for MODCON1000
Page 40: ...40 LP 428 REV 9 2 14 E GAS VALVE Figure 22 Mod Con 1000 Gas Valve ...
Page 46: ...46 LP 428 REV 9 2 14 Figure 25 Figure 26 Cascade Resistor Plug Installation Detail ...
Page 47: ...47 LP 428 REV 9 2 14 Figure 27 Mod Con Cascade Master and Follower Wiring ...
Page 48: ...48 LP 428 REV 9 2 14 Figure 28 Mod Con Internal Connection Diagram LP 428 K ...
Page 70: ...70 LP 428 REV 9 2 14 Figure 31 MOD CON 1000 External Parts Blowout ...
Page 71: ...71 LP 428 REV 9 2 14 Figure 32 MOD CON 1700 External Parts Blowout ...
Page 72: ...72 LP 428 REV 9 2 14 Figure 33 ...
Page 73: ...73 LP 428 REV 9 2 14 Figure 34 LP 445 S ...
Page 74: ...74 LP 428 REV 9 2 14 Figure 35 LP 428 V ...
Page 75: ...75 LP 428 REV 9 2 14 Figure 36 ...
Page 78: ...78 LP 428 REV 9 2 14 ...
Page 79: ...79 LP 428 REV 9 2 14 ...