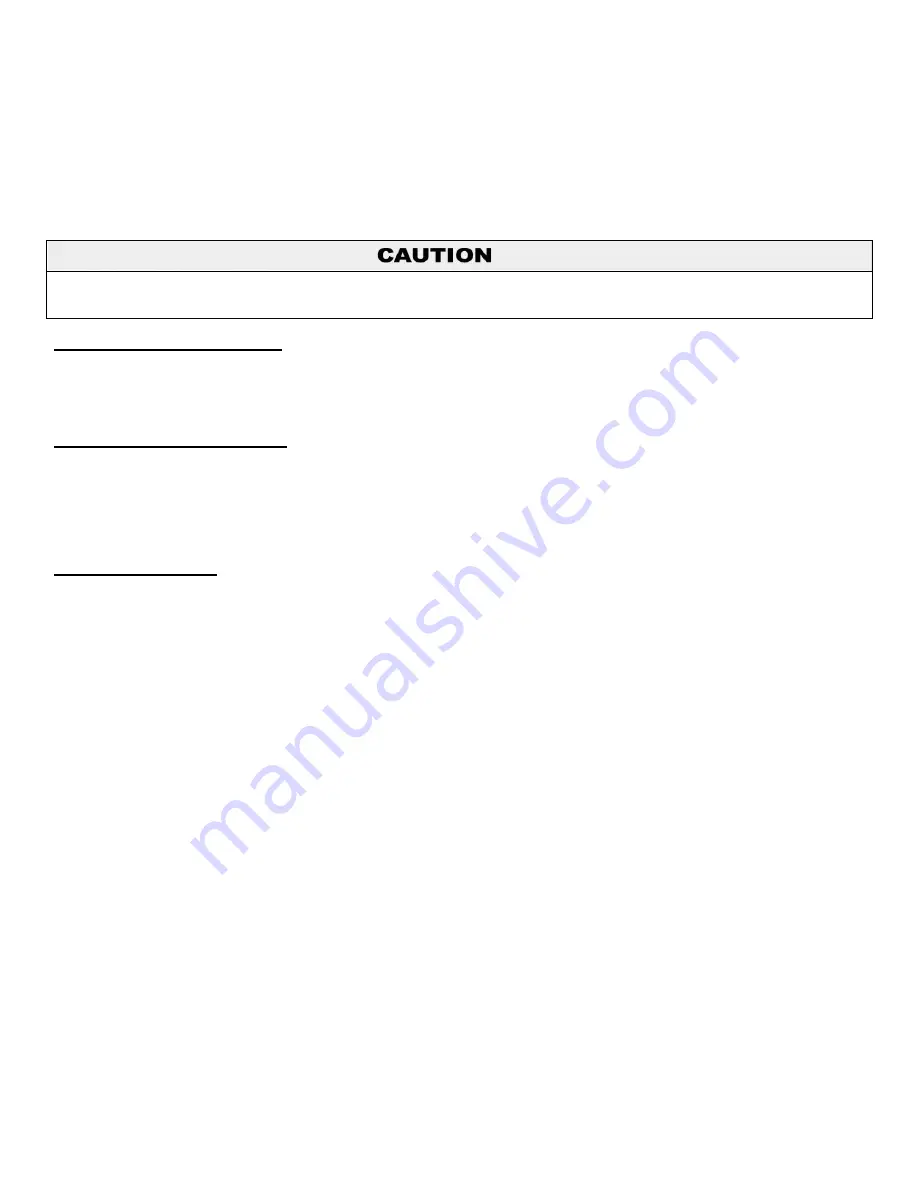
21
LP- 428 REV. 9.2.14
2. The glycol solution should be tested at least once a year and as recommended by the glycol manufacturer.
3. Anti-freeze solutions expand more than water. For example: A 50% by volume solution expands 4.8% in volume for a temperature
increase from 32
o
F to 180
o
F, while water increases 3% over the same temperature rise. Allowances must be made for this expansion in
the system design.
4. A 30% mixture of glycol will result in a BTU output loss of 15% with a 5% increase in head against the system circulator.
5. A 50% mixture of glycol will result in a BTU output loss of 30% with a 50% increase in head against the system circulator.
It is highly recommended that you carefully follow the glycol manufacturer’s recommended concentrations, expansion requirements,
and maintenance recommendations (pH additive breakdown, inhibitor reduction, etc.). Carefully figure the additional friction loss in the
system as well as the reduction in heat transfer coefficients.
J. ZONING WITH ZONE VALVES
1. Connect the boiler to the system as shown in Boiler Piping Details when zoning with zone valves. The primary/secondary piping
shown ensures the boiler loop will have sufficient flow. It also avoids applying the high head of the boiler circulator to the zone valves.
2. Connect DHW (domestic hot water) piping to indirect storage water heater.
K. ZONING WITH CIRCULATORS
1. Connect the boiler to the system when using circulator zoning as shown in Boiler Piping Details.
NOTE:
The boiler circulator cannot
be used for a zone. It must only supply the boiler loop.
2. Install a separate circulator for each zone.
3. Connect DHW (domestic hot water) piping to indirect storage water heater.
L. MULTIPLE BOILERS
1. Connect multiple boilers as shown in Boiler Piping Details.
2. All piping shown is reverse return to assure balanced flow throughout the connected boilers.
3. Each connected boiler must have its own circulator pump to assure adequate flow.
4. Connect DHW (domestic hot water) piping to indirect storage water heater.
5. The system flow (secondary loop) must be greater than the primary (boiler) loop flow.
Summary of Contents for MODCON1000
Page 40: ...40 LP 428 REV 9 2 14 E GAS VALVE Figure 22 Mod Con 1000 Gas Valve ...
Page 46: ...46 LP 428 REV 9 2 14 Figure 25 Figure 26 Cascade Resistor Plug Installation Detail ...
Page 47: ...47 LP 428 REV 9 2 14 Figure 27 Mod Con Cascade Master and Follower Wiring ...
Page 48: ...48 LP 428 REV 9 2 14 Figure 28 Mod Con Internal Connection Diagram LP 428 K ...
Page 70: ...70 LP 428 REV 9 2 14 Figure 31 MOD CON 1000 External Parts Blowout ...
Page 71: ...71 LP 428 REV 9 2 14 Figure 32 MOD CON 1700 External Parts Blowout ...
Page 72: ...72 LP 428 REV 9 2 14 Figure 33 ...
Page 73: ...73 LP 428 REV 9 2 14 Figure 34 LP 445 S ...
Page 74: ...74 LP 428 REV 9 2 14 Figure 35 LP 428 V ...
Page 75: ...75 LP 428 REV 9 2 14 Figure 36 ...
Page 78: ...78 LP 428 REV 9 2 14 ...
Page 79: ...79 LP 428 REV 9 2 14 ...