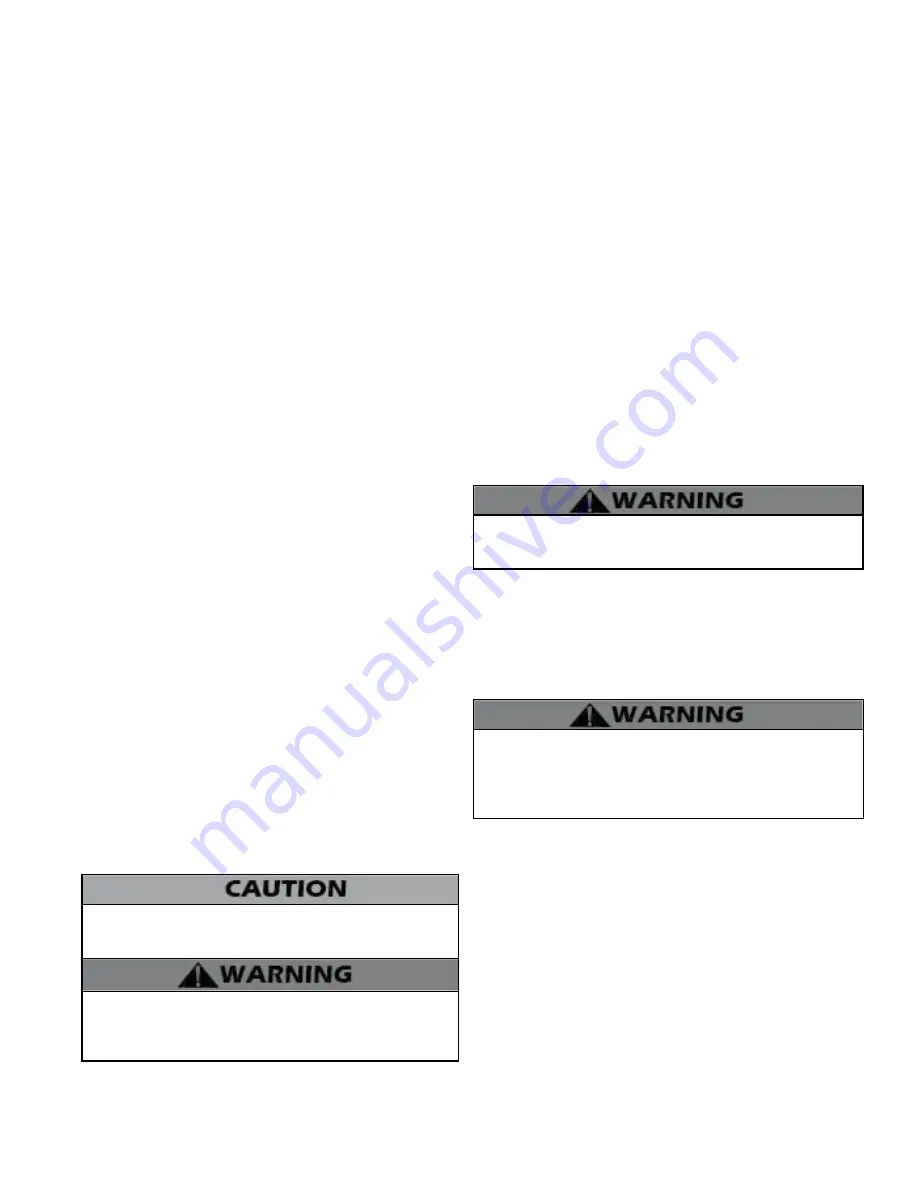
lp-505 Rev. 000 Rel. 015 Date 1.7.20
11
1. Direct Vent of Exhaust and Intake
If installing a direct vent option, combustion air must be drawn
from the outdoors directly into the water heater intake and exhaust
must terminate outdoors. There are three basic direct vent options
detailed in this manual: 1. Side Wall Venting, 2. Roof Venting, and 3.
Unbalanced Venting.
Be sure to locate the heater such that the exhaust vent and intake
piping can be routed through the building and properly terminated.
Different vent terminals can be used to simplify and eliminate
multiple penetrations in the building structure (see Optional
Equipment in Venting Section). The exhaust vent and intake piping
lengths, routing, and termination methods must all comply with the
methods and limits given in the Venting Section, this manual.
When installing a combustion air intake from outdoors, care must
be taken to utilize uncontaminated combustion air.
To prevent
combustion air contamination, see Table 7.
2. Power Venting, Indoor Combustion Air in Confined or
Unconfined Space
This heater requires fresh, uncontaminated air for safe operation
and must be installed in a mechanical room where there is adequate
combustion and ventilating air.
NOTE: To prevent combustion air
contamination, see Table 7.
Combustion air from the indoor space can be used if the space has
adequate area or when air is provided through a duct or louver
to supply sufficient combustion air based on the water heater
input. Never obstruct the supply of combustion air to the water
heater. If the water heater is installed in areas where indoor air is
contaminated (see Table 7) it is imperative that the water heater be
installed as direct vent so that all combustion air is taken directly
from the outdoors into the water heater intake connection.
Unconfined space
is space with volume greater than 50 cubic feet
per 1,000 BTU/hr (4.8 cubic meters per kW) of the total input rating of
all fuel-burning appliances installed in that space. Rooms connected
directly to this space through openings not furnished with doors are
considered part of the space. See Venting Section for details.
Confined space
is space with volume less than 50 cubic feet per
1,000 BTU/hr (4.8 cubic meters per kW) of the total input rating of all
fuel-burning appliances installed in that space. Rooms connected
directly to this space through openings not furnished with doors are
considered part of the space.
When drawing combustion air from inside a conventionally
constructed building to a confined space, such space should be
provided with two permanent openings: one located 6” (15cm)
below the space ceiling, the other 6” (15cm) above the space floor.
Each opening should have a free area of one square inch per 1,000
BTU/hr (22cm
2
/kW) of the total input of all appliances in the space,
but not less than 100 square inches (645cm
2
).
If the confined space is within a building of tight construction, air for
combustion must be obtained from the outdoors as outlined in the
Venting section of this manual.
When drawing combustion air from the outside into the
mechanical room, care must be taken to provide adequate freeze
protection.
Failure to provide an adequate supply of fresh combustion air can
cause poisonous flue gases to enter the living space, resulting
in severe personal injury or death. To prevent combustion air
contamination, see Table 7.
In the Commonwealth of Massachusetts and As Required by State
and Local Codes:
Installation of Carbon Monoxide Detectors: At the time of installation
or replacement of the vented gas fueled appliance, the installing
plumber or gas fitter shall observe that a hard wired carbon monoxide
detector with an alarm and battery back-up is installed on the floor
level where the gas appliance is installed, unless the appliance is
located in a detached, uninhabitable structure separate from the
dwelling, building, or structure used in whole or in part for residential
purposes.
In addition, the installing plumber or gas fitter shall observe that a hard
wired carbon monoxide detector with an alarm and battery back-up is
installed on each additional level of the dwelling, building, or structure
served by the vented gas appliance. It shall be the responsibility of the
property owner to secure the service of qualified licensed professionals
for the installation of hard wired carbon monoxide detectors.
a. In the event that the vented gas fueled appliance is installed in a
crawl space or attic, the hard wired carbon monoxide detector with
alarm and battery back-up shall be installed on the next adjacent
floor level.
b. In the event that these requirements cannot be met at the time
of completion of installation, the owner shall have a period of thirty
(30) days to comply with the above requirements; provided, however,
that during said thirty (30) day period, a battery operated carbon
monoxide detector with an alarm shall be installed.
F. Carbon Monoxide Detectors
Do not attempt to vent this water heater by any means other than
those described in this manual. Doing so will void the warranty and
may result in severe personal injury or death.
Approved Carbon Monoxide Detectors: Each carbon monoxide
detector as required in accordance with the above provisions shall
comply with NFPA 70 and be ANSI/UL 2034 listed and IAS certified.
G. Prevent Combustion Air Contamination
Install intake air piping for the heater as described in the Venting
Section, this manual. Do not terminate exhaust in locations that can
allow contamination of intake air.
Ensure that the intake air will not contain any of the contaminants
in Table 7. Contaminated air will damage the heater, resulting in
possible substantial property damage, severe personal injury, or
death. For example, do not pipe intake air near a swimming pool or
laundry facilities. These areas always contain contaminants.
Summary of Contents for Hydra Smart RT-199
Page 40: ...lp 505 Rev 000 Rel 015 Date 1 7 20 40 Figure 38 150 Model Electrical Wiring Diagram ...
Page 41: ...lp 505 Rev 000 Rel 015 Date 1 7 20 41 Figure 39 150 Model Ladder Diagram ...
Page 42: ...lp 505 Rev 000 Rel 015 Date 1 7 20 42 Figure 40 199 Model Electrical Wiring Diagram ...
Page 43: ...lp 505 Rev 000 Rel 015 Date 1 7 20 43 Figure 41 199 Model Ladder Diagram ...