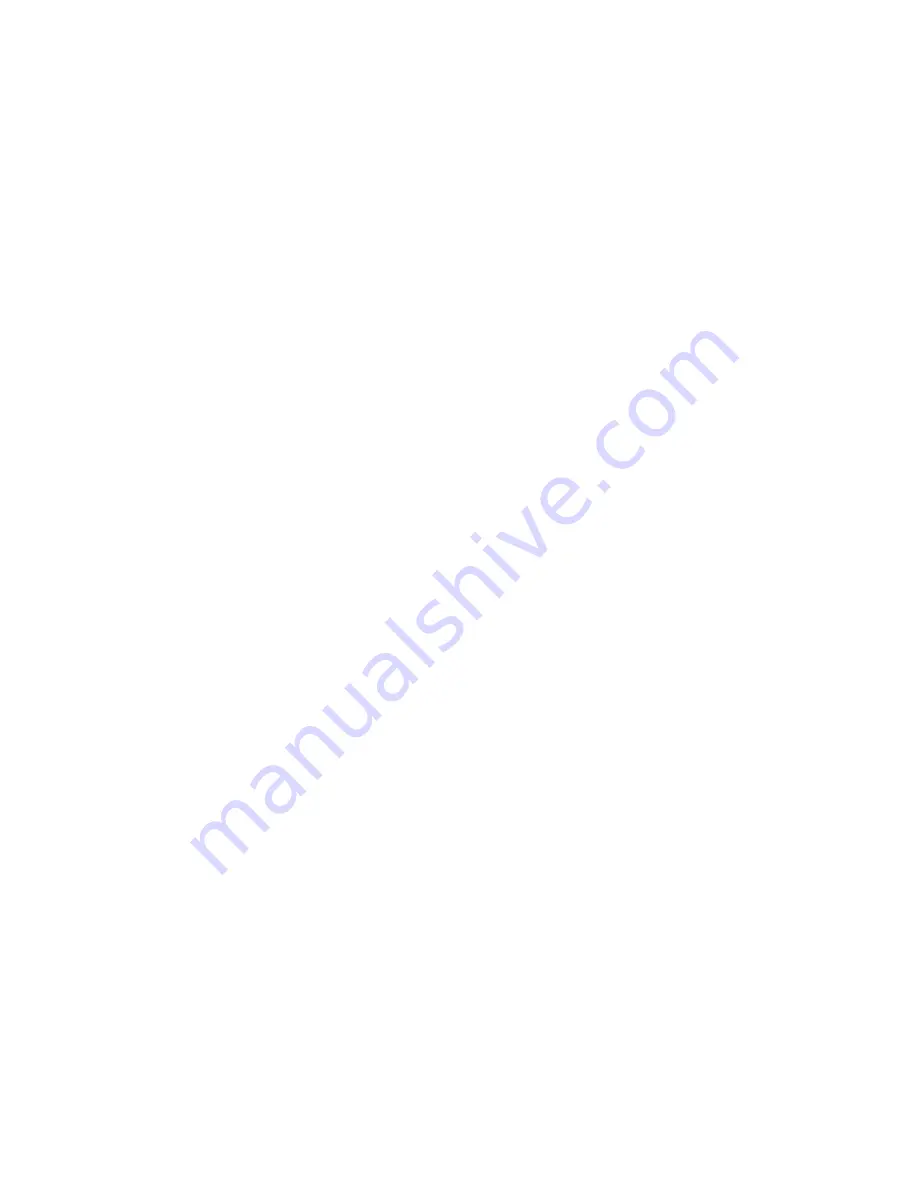
LP-517 Rev. 000 Rel. 019 Date 7.21.20
32
L. Optional Flow Switch
NOTE:
Follow the more detailed instructions included with the flow
switch kit for proper installation steps.
1. Attach the correct flow paddle to the flow switch.
2. Thread flow switch into the fitting provided on the manifold using
teflon thread tape.
Make certain the FLOW arrow points in the
correct direction.
3. Locate the two red wires at the boiler and connect them to the flow
switch as described in the flow switch instructions.
4. When installation is complete, power up the boiler and use the
control to access installer parameter #20 and change the default value
to FLOW SWITCH. When done, create a demand and observe boiler
function to verify the installation is working properly.
NOTE:
The flow switch requires a minimum flow rate of 21 GPM to
activate the boiler. The sensitivity of the flow switch can be adjusted.
See manufacturer’s instructions for details.
M. UL353 Internal Low Water Cut-Off (Factory Installed)
The supplied internal Low Water Cutoff (LWCO) meets UL 353
requirements to function as a safety, locking out the boiler when water
level is inadequate for safe operation.
To test, press the
RESET
and
v
buttons together for 3 - 5 seconds. The
LWCO will trip and indicate an F21 or F22 fault code on the display. To
clear the error, press
RESET
.
N. Optional High Limit Manual Reset
NOTE:
Follow the more detailed instructions included with the high
limit manual reset kit for proper installation steps.
1. Thread the control well into the fitting provided on the manifold
using teflon thread tape.
2. Insert the control probe into the control well.
3. Secure the high limit manual reset box to the control well.
4. Locate and disconnect the red high limit manual reset wires. Connect
the two red wires to the manual reset box.
5. When installation is complete, power up the boiler and test the
reset according to the provided instructions. If the reset operates
properly, set the high limit temperature as described in the provided
instructions. When done, create a demand and observe boiler function
to verify the installation is working properly.
P. Wiring of Cascade System Communication Bus
1. A Cascade Bus Termination Plug has been installed on the customer
connection board of this boiler. The purpose of this plug is to stabilize
communication between multiple boilers and reduce electrical “noise”.
See Figure 22 for Cascade Bus Termination Plug installation detail.
NOTE:
It is important that the termination plug in multiple boilers
(cascaded units) be installed as depicted in Figure 22. Leave the plug
installed in the J3 port on the Master boiler. Remove the plug on
intermediate Follower boilers. Move the plug to the J4 port on the final
Follower boiler.
2. Use standard CAT3 or CAT5 computer network patch cables to
connect the communication bus between each of the boilers. These
cables are readily available at any office supply, computer, electronic,
department or discount home supply store in varying lengths. If you
possess the skills you can also construct custom length cables.
3. It is recommended to use the shortest length cable that will
reach between the boilers and create a neat installation. Do not run
unprotected cables across the floor where they may become wet or
damaged. Avoid running communication cables parallel and close to
or against high voltage (120 volt or greater) wiring. HTP recommends
that the maximum length of communication bus cables not exceed
200 feet.
4. Route the communication cables through one of the knockouts in
the cabinet.
5. Connect the boilers in a daisy chain configuration as shown below. It
is best to wire the boilers using the shortest wire runs rather than trying
to wire them in the order that they are addressed. The communication
Q. Cascade Master Pump and Sensor Wiring
1. Connect the system pump hot wire to the terminal marked 7 (SYS
PUMP).
2. Connect the system pump neutral to the 8 (SYS NEUT) terminal
and the pump ground wire to the 9 (SYS GND) terminal.
3. Connect the boiler pump to the terminals marked 1 (BOILER HOT),
2 (BOILER NEUT), and 3 (BOILER GND).
4. Connect the system pipe sensor to the terminals marked 18 and
19 (SYS SENSOR).
5. Connect the outdoor sensor (if used) to the terminals marked 12
and 13 (OUTDOOR SEN).
6. Connect the signal to start the system to the terminals marked 14
and 15 (THERMOSTAT).
NOTE:
This signal can come from a room thermostat or a dry contact
closure. No power of any voltage should be fed into either of these
terminals.
R. Cascade Follower Pump and Sensor Wiring
1. If it is desired to have the boiler control the boiler pump, connect
the boiler pump to the 1 (BOILER HOT), 2 (BOILER NEUT), and 3
(BOILER GND) terminals.
2. If you are using an indirect fired water heater connected directly
to the follower boiler, connect the pump for it to the 4 (DHW HOT), 5
(DHW NEUT), and 6 (DHW GND) terminals.
If desired, an alarm bell or light can be connected to the alarm
contacts of the boiler. The normally closed alarm contact may be
used to turn a device off if the boiler goes into lockout mode. The
alarm contacts are rated 5 amps at 120 VAC.
To connect an alarm device, connect the power for the device to
the J10-2 (ALARM COM) terminal. Connect the alarm device hot wire
to the J10-1 (ALARM NO) terminal. Connect the neutral or return of
the alarm device to the neutral or return of the power for the alarm
device.
To connect a device that should be powered off during a boiler
lockout condition, follow the same instructions as above and use
the J10-3 (ALARM NC) terminal rather than the ALARM NO terminal.
NOTE:
In a cascade system, the alarm output of the boiler addressed
as #1 will also be active if the master boiler has a lockout condition.
The alarm output of boilers addressed #2-15 will only sound if a
lockout condition occurs on that specific boiler.
S. Variable Speed Pumping
Variable speed pump support is available on the primary loop of
all models manufactured after 11/15/2016. This feature controls
pump speed via an analog 0-10VDC signal supplied via the 0-10VA
connection on the Customer Connection Board.
When this feature is in use, an installer selected Delta T is maintained
with the Supply and Return sensors, increasing efficiency and
providing better system temperature control. When the difference
between the Supply and Return temperatures is greater than
the desired setting, the pump will increase speed and flow to
compensate. Conversely, if the Delta T is less than the desired
setting, the pump will decrease speed and flow to compensate.
NOTE:
This feature may be used in Primary / Secondary piping
arrangements ONLY!
Variable Speed Pumping Wiring:
1. Connect the boiler pump as shown in Figure 22 to the terminals
marked 1 – (HOT), 2 – (NEUT), and 3 – (GND). The connections shown
are suitable for a maximum continuous pump draw of 2 amps at 120
volts. If the pump requires more current or voltage than the 120 volts
supplied, an external motor starter or contactor will be required.
2. Connect the 0-10v input wires on the variable speed pump to the
bus jacks on the customer connection panel are interchangeable so
you can use either one or both in any order to connect the cable.
If you have connected the boilers to each other properly, there will
be no open communication connection ports.