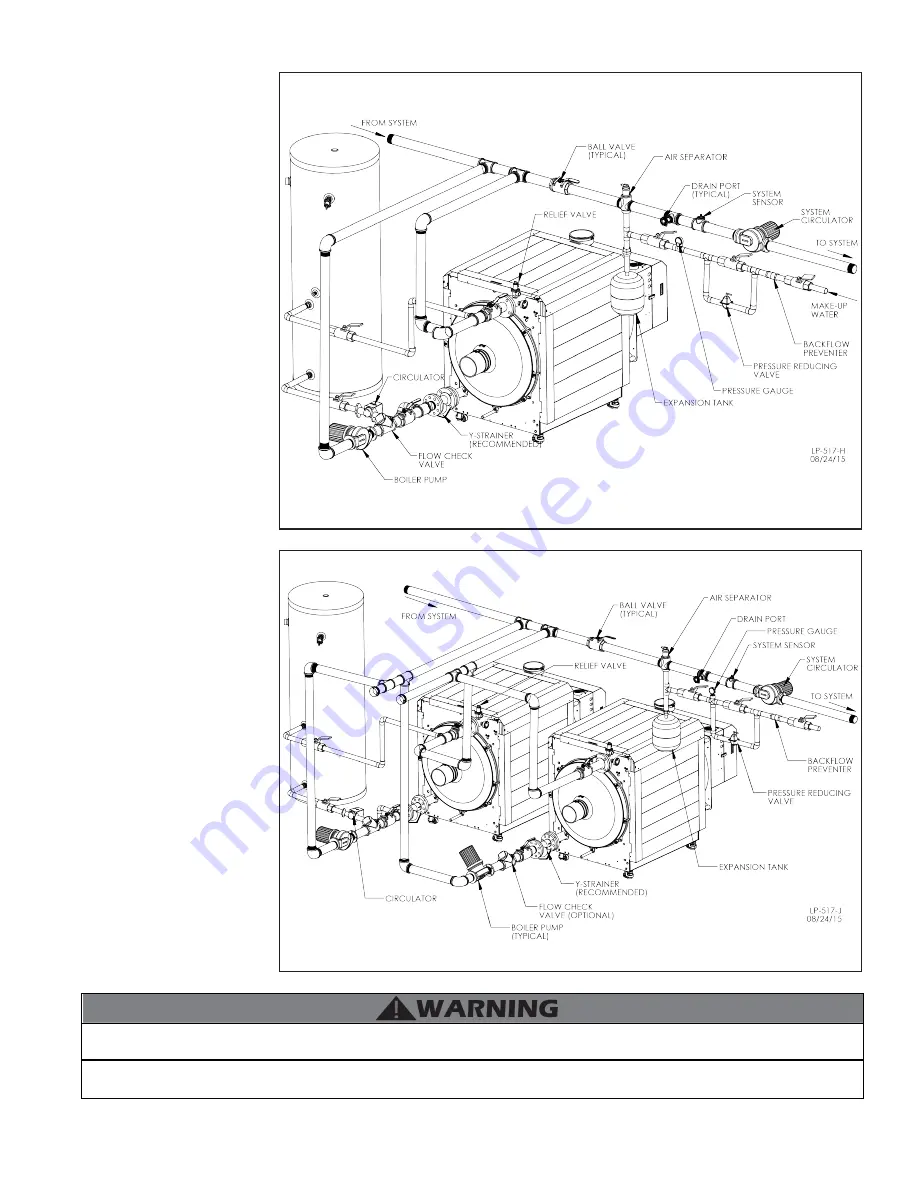
LP-517 Rev. 000 Rel. 019 Date 7.21.20
19
O. Applications*
*NOTE:
Systems shown are
primary/secondary piping
systems. These recommended
systems have a primary (boiler)
loop, and secondary circuits for
heating. The primary loop and
secondary circuits have separate
circulators. The use of other near
boiler piping configurations could
result in improper flow rates,
leading to inadvertent boiler high
limit shutdowns and poor system
performance.
NOTE:
In piping applications
utilizing a single zone, it is
recommended that the installer
use flow / check valves with
weighted seats at or near the
appliance to prevent gravity
circulation.
FIGURE NOTES:
1. This drawing is meant to
demonstrate system piping
concept only.
2. A mixing valve is recommended
if the DHW temperature is set
above the factory setting of 119
o
F.
3. Install a minimum of 12
diameters of straight pipe
upstream of all circulators.
4. Install a minimum of 6
diameters of straight pipe up and
downstream of all closely spaced
tees.
5. Piping shown is Primary/
Secondary.
6. The minimum pipe size for
connecting an HTP indirect fired
water heater is 1”.
7. The minimum pipe size for
connecting a 750 boiler is 2”. The
minimum pipe size for connecting
a 1000 boiler is 2 1/2”.
8. System flow (Secondary Loop)
must be greater than the boiler’s
Primary Loop flow.
9. Installations must comply with
all local codes.
10. In Massachusetts, a vacuum
relief valve must be installed on
the cold water line per 248 CMR.
11. See Multiple Boiler Manifold
Piping chart, this manual, when
sizing and installing a multiple
boiler system.
The piping will not support the weight of the circulators. Refer to the circulator manufacturer’s instructions to properly support the circulator.
Failure to comply with these instructions could result in property damage, severe personal injury, or death.
An ASSE 1017 thermostatic mixing valve is recommended on all indirect water heaters if the hot water temperature leaving the heater is
above 119
o
F. Failure to do so could result in substantial property damage, serious injury, or death.
Figure 7 - Single Boiler Space Heating with Indirect Priority
Figure 8 - Cascaded Boilers with Indirect Priority on One