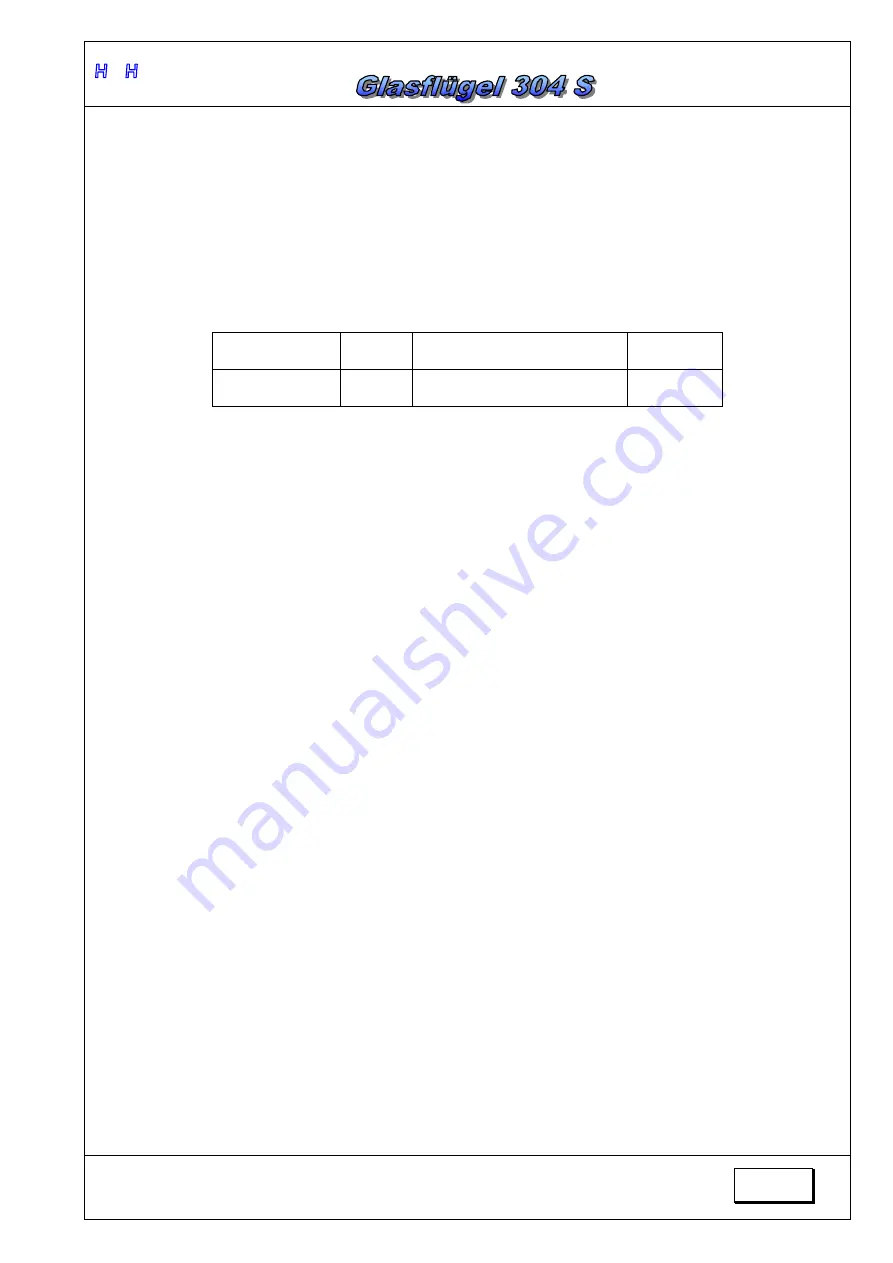
T
T
e
e
c
c
h
h
n
n
i
i
c
c
a
a
l
l
D
D
e
e
s
s
c
c
r
r
i
i
p
p
t
t
i
i
o
o
n
n
,
,
O
O
p
p
e
e
r
r
a
a
t
t
i
i
n
n
g
g
,
,
M
M
a
a
i
i
n
n
t
t
e
e
n
n
a
a
n
n
c
c
e
e
a
a
n
n
d
d
R
R
e
e
p
p
a
a
i
i
r
r
M
M
a
a
n
n
u
u
a
a
l
l
Document No.: 304S/MM
Date of Issue:
08/14
3-3
H
P
H
Ltd.
Landing Gear
Clean brake drum, check brake linings and if necessary renew. Check and
adjust bowden cable or brake lever, check side play of the wheel hub.
In addition, observe the instructions of TOST.
Ensure that the wheel axle and the two landing gear hinge-tubes are not bent,
and that the fiberglass bearings on the wheel box are not damaged.
Check pressure of main- and tail wheel.
Main wheel:
Takeoff
weight
[ lbs.]
837
992
1102
Tire size
[ kg ]
380
450
500
∆
p
[ bar ]
3.5
4.0
5.0
5.00-5
[ psi ]
51
58
72
Tail wheel:
∆
p = 2.5 bar, 36 p.s.i.
Check static and pitot inlets, lines, as well as line quick connectors for free flow
and leak.
Ensure there are no loose instrument face glasses.
On the rigged aircraft, check control deflections and function of the control
system and release mechanisms. A gap between the ailerons and flaps should
be 4.5 mm, at least
Check capacity as well as charging of the battery, inspect electric installation
and attachment of el. equipment.
Compensate the magnetic compass.