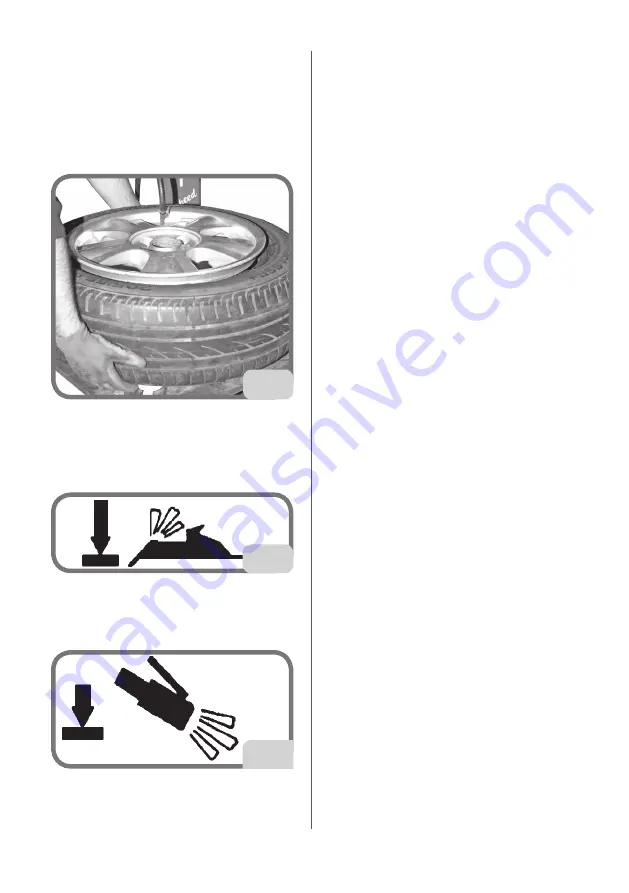
58
Operator's manual
M 824
- Connect the Doyfe inflator chuck on the air
hose to the valve stem (Fig. 28).
- Hold the tyre with your hands and lift it until
there is a slight gap between the lower bead
and bottom edge of the rim in order to close
the upper bead and the top of the rim (Fig.
28).
28
- Fully press the inflation pedal down for a
short period to the bead seating position (fig.
29a). The tyre will expand and the beads will
seat.
29a
- Continue to press the pedal in the inflation
position (fig. 29b) until the beads are com-
pletely inserted.
29b
Note
: to improve the operation of the tubeless
tyre inflation system the compressed air line
pressure must be between 8/10 bar.
TROUBLESHOOTING
Turntable does not turn
Power cord conductor shorting to
ground.
➥
Check the wiring.
Motor shorted.
➥
Replace the fuses
➥
Replace the motor.
Rotation control pedal fails to
return to the central position
Control spring broken.
➥
Replace the command spring.
Bead breaker pedal and table
top pedal do not return to home
position
Control spring broken.
➥
Replace the pedal return spring.
No oil in lubricator.
➥
Top up lubricator with SAE20 non-
detergent oil.
Air leak inside the machine
Air leak from bead breaker cock.
➥
Replace the cock.
➥
Replace the bead breaker cylinder.
Air leak from the table top cock.
➥
Replace the turntable cylinder.
➥
Replace the swivel connector.
Bead breaker cylinder lacks
force, fails to break beads and
leaks air
Silencer plugged.
➥
Replace the silencer.
Cylinder seals worn.
➥
Replace the gaskets.
➥
Replace the bead breaker cylinder.
Summary of Contents for M 824
Page 16: ...Operator s manual M 824 53 EN 10 20 13 23 14 24 min 17 14...
Page 28: ...Operator s manual M 824 65 EN 32...
Page 29: ...66 Operator s manual M 824 33...
Page 30: ...Operator s manual M 824 67 EN 34...
Page 31: ...68 Operator s manual M 824 35...
Page 32: ...Operator s manual M 824 69 EN STANDARD VERSION...
Page 33: ...70 Operator s manual M 824 FS VERSION...
Page 34: ...Operator s manual M 824 71 EN STANDARD VERSION AIR MOTOR...
Page 35: ...72 Operator s manual M 824 FS VERSION AIR MOTOR...