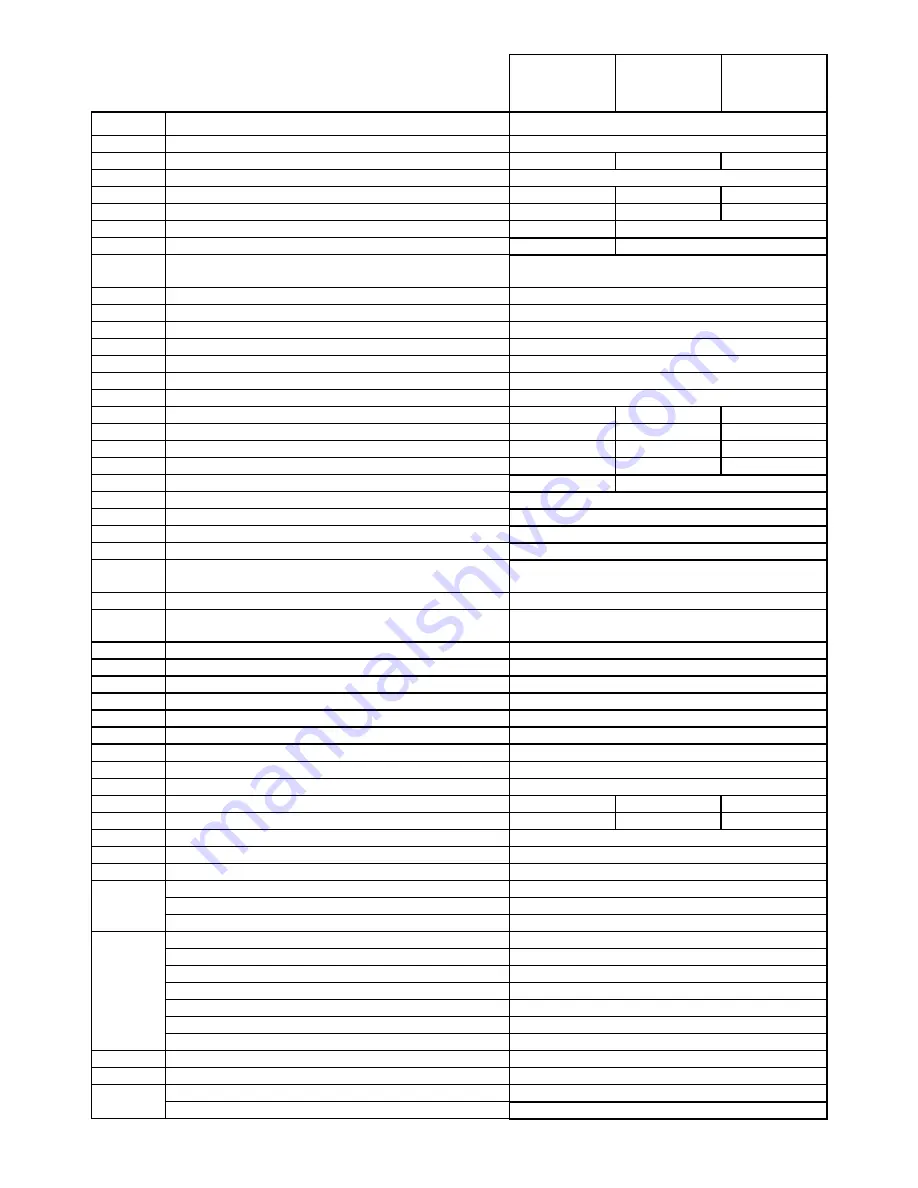
SELECTIVE PURPOSE Manual Page (70)
TABLE 4: Replacement Parts for Models Listed to Right
50E, 51E
50EA, 50EAR
75E, 76E
75EA, 75EAR
100E, 101E
100EA,
100EAR
Item No.
PART DESCRIPTION
PART NUMBER
3
Insulated lug spacers (8)
E50J2
7 Main
shaft
E50D1
E75D1
E100D1
8 Shaft
sleeve
E50D2
9
Top ice blade 20
2@
L, 12
2@
L, 20
2@
L
E30E3 E20E2 E30E3
9a
Nuts, Bolts & washers (top ice blade)
E30E5
E20E6
E30E5
10
Bottom ice blade
-
E30E3
10a
Nuts, Bolts & washers (bottom ice blade)
-
E30E5
Ice Blade Adjustment Gauge kit. Set of five feeler gauges for
ice blade adjustment.
E10T15
11
Ice deflector blade
E50G5
11a
Nuts, Bolts & washers (ice deflector)
E50G8
12 Insulating
ring
(2)
E50J1
12a
Insulating ring adhesive -
2
pint
7V033
13
Ice deflector bracket (2)
E50G9
14 or 15
Top & Bottom auxiliary ice scraper (2)
E20E4
15a
Nuts, Bolts & washers (aux. Ice scraper)
E20E7
16 Squeegee
E30F3
E75F3
E100F3
17 Squeegee
wrapper
E30F8
E75F4
E100F4
17a
Nuts, Bolts & washers (squeegee wrapper)
E30F22
E75F8
E100F8
18
Top squeegee bracket
E50F1
E75F1
E50F1
19
Bottom squeegee bracket
-
E50F1
20
Main shaft bearings (2)
E50K1
21
Bottom bearing thrust plate
E50K2
22 & 23
Main bearing grease seal (3)
E50K13
25
Top main bearing retainer
E50K3
25a
Top bearing replacement kit (includes bearing, 2-seals, shaft
sleeve.
E50K10
26
Bottom main bearing retainer
E50K4
26a
Bottom bearing replacement kit (includes bearing, 1-seal,
shaft sleeve.
E50K11
27 Bottom
bearing
cover
E50K5
28
Main bearing pull-out washer (2)
E50K6
35 & 36
Water distribution side spout & fitting (11)
E50H19
37 & 38
Water distribution bottom spout & fitting
E50H31
40
Water sump bolt down cover
E50H11
41
Water sump removable cover
E50H15
42
Water sump gasket
E50J3
43
Water float valve
E50H18
44
Water float valve fitting
CNBHF-SG-BR08/08
53
Water tube
E50H22
E75H4
E100H1
54 Water
tube
insulation
E50H32
E75H2
E100H2
55
Water tube valve brass nipple
NPBR-075/CL
56
Water tube fitting
CNM-SG-BR14/12
57
Water tube regulating valve
E50H24
Water pump 230-460/3/50-60
E50Q1
Water pump 220-230/1/50-60
E50Q2
62
Water pump 575/3/60
E50Q9
Drive motor 208-230-460/3/50-60 1 HP O.D.P.
E50M1
Drive motor 115-230/1/50-60
:
HP, 1 HP O.D.P.
E50M2
Drive motor 208-230-460/3/50-60 1 HP TEFC
E50M4
Drive motor 220/-380/3/50 TEFC
E50M5
Drive Motor 208-230/1/60 1 HP, TEFC
E50M6
Drive Motor 110/200-220/1/50 1 HP, TEFC
E50M7
63
Drive motor 220/-380/3/50 O.D.P.
E50M9
63A
Drive motor key
E50M8
65,66,67
Flexible coupling - complete
E50N1
Speed reducer 60 cycle
E50R1-935
68
Speed Reducer 50 Cycle
E50R2-935
Summary of Contents for Rapid Freeze
Page 6: ......
Page 16: ...6 SEAWATER MODEL INSTALLATION 10 ASSEMBLY DRAWING 11ESS 21ESS...
Page 17: ...6 SEAWATER MODEL INSTALLATION 11 ASSEMBLY DRAWING 31ES 31ESS...
Page 18: ...6 SEAWATER MODEL INSTALLATION 12 ASSEMBLY DRAWING 51ES 51ESS...
Page 19: ...6 SEAWATER MODEL INSTALLATION 13 ASSEMBLY DRAWING 11EFS 21EFS...
Page 20: ...6 SEAWATER MODEL INSTALLATION 14 ASSEMBLY DRAWING 51EFS...
Page 21: ...6 SEAWATER MODEL INSTALLATION 15 ASSEMBLY DRAWING 10ESS 20ESS...
Page 22: ...6 SEAWATER MODEL INSTALLATION 16 ASSEMBLY DRAWING 30ES 30ESS...
Page 23: ...6 SEAWATER MODEL INSTALLATION 17 ASSEMBLY DRAWING 50ES 50ESS...
Page 28: ...9 How The Rapid Freeze Flaker Operates 22 ICE FLAKER CUTAWAY DRAWING EXHIBIT 26...
Page 38: ...12 Control Panel Wiring Diagrams 32 Control Panel Schematic E20T40 RL...
Page 39: ...12 Control Panel Wiring Diagrams 33 460 3 60 WIRING E20T47...
Page 42: ...12 Control Panel Wiring Diagrams 36 220 1 50 Control Panel Schematic E20T40 RL 50...
Page 43: ...12 Control Panel Wiring Diagrams 37 380 3 50 Control Panel Schematic E20T60...
Page 64: ...15 Service Adjustment 58 EXHIBIT 40...