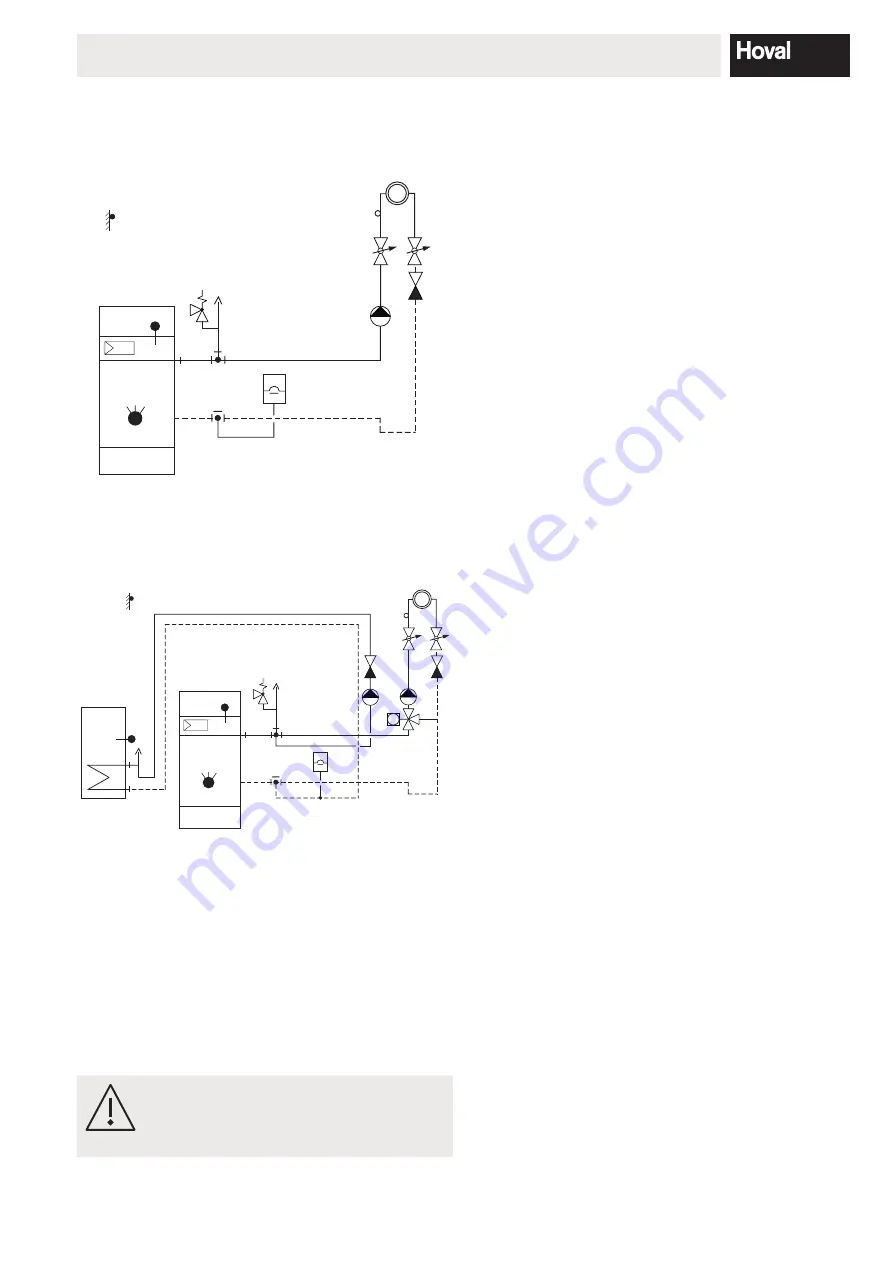
4.6
Hydraulic integration
Examples
Direct heating circuit
Fig. 40
Mixer circuit and water heater
M
Fig. 41
4.7
Condensate discharge
The boiler condensate drain must be made of corrosion-
resistant material.
The following materials are suitable for the condensate
drain:
- PVC
- PE
- PP
-
ABS
The minimum inner diameter of the con-
densate drain must be 15 mm. The con-
densate drain must be sufficiently in
-
clined
.
A:
A:
it is not necessary to neutralise condensate
from an oil-fired condensing unit of up to 120
kW drained together with domestic waste
water from a private household.
CH:
For the UltraOil
®
, the fuel used must be heat-
ing oil EL low-sulphur. As a rule, neutrali-
sation of the condensate is not necessary.
Local regulations pertaining to condensate
discharge must be observed.
D:
For the UltraOil
®
, the fuel used must be heat-
ing oil EL low-sulphur. Neutralisation is there-
fore unnecessary. Regarding the discharge
of condensate, the local regulations and the
ATV (Sewage Engineering Association) data-
sheet must be observed.
4.8
Setting the temperature regulators
Basic setting of the controller is carried out by the heating
contractor. Selection and setting of the various heating
programmes in accordance with the operating manual.
4.9
Safety valves
The heating system and hot water system must each be
protected with one safety valve against unauthorised high
pressures. The discharge capactiy of the valves must cor-
respond with the boiler’s maximum nominal heat output.
The valve must be installed in the flow line in the immedi
-
ate vicinity of the boiler.
4.10 Charging pump (boiler with water heater)
Speed of rotation and output must correspond to the re-
quirements of the water heater. Setting carried out by the
heating installation engineer.
4.11 Heating pump
Speed of rotation and output must correspond to the re-
quirements of the system. They are to be set by the heat-
ing installation engineer.
25
4 210 255 / 02
INSTALLATION
Summary of Contents for UltraOil 16
Page 49: ...49 4 210 255 02...