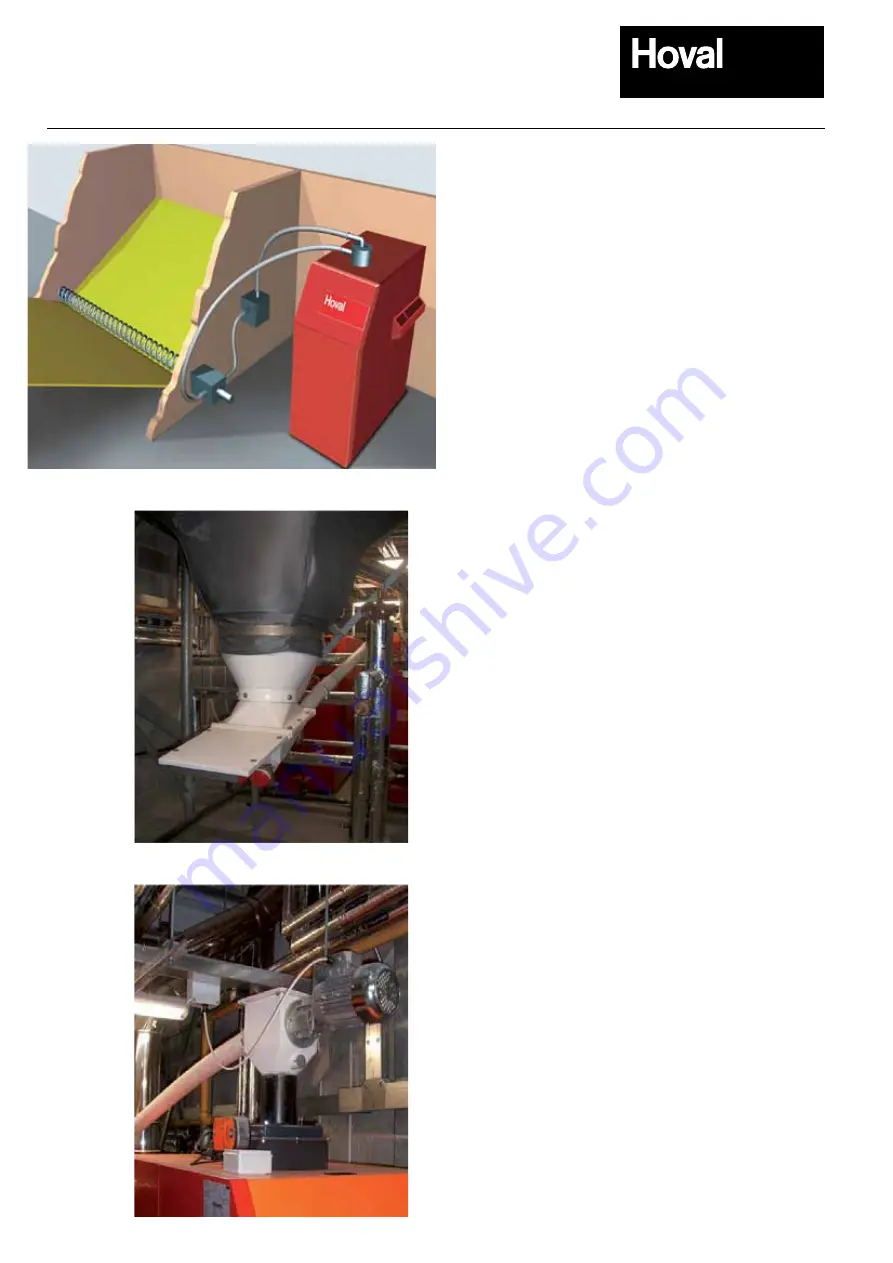
The successful and effective biomass installation is dependant on a
well planned and installed pellet feeding system to ensure delivery of
pellets to the point of combustion in the correct volume, quantity and
quality.
With regard to the bulk storage or wood pellet fuel store the following
simple guidelines offer advice to assist in the design and sizing for a
successful installation.
A bulk wood pellet fuel store should be located as close as possible
to the biomass boiler. The design of the fuel store and the recovery
of the pellets from the store and the subsequent transfer of the fuel
to the boiler should be kept as simple as possible. Tall thin storage,
such as purpose designed silos, often represent the most effective
way of storing wood pellet fuel and can lead to the best use of a given
storage volume. The angle of the discharge cone from such a silo
would typically be 60º to ensure complete mass flow from the store. A
possible alternative to a storage silo would be a bespoke build bunker
store. These typically require a larger floor area and are less effective
in terms of the available recoverable volume of fuel. Some profiling
of the bunker base should be considered – minimum angles of 45º
should be adopted if profiling bunker – which will significantly reduce
the volume available for the storage of pellet fuel. The natural angle of
repose of the fuel will vary depending on the quality of the wood pellet
but will typically be greater than 45º. Again this can significantly reduce
the recoverable volume available in the pellet store. Whichever fuel
store design is adopted it must be such that it:
• Keeps the fuel dry as water ingress will cause the pellets to fall apart
and block handling equipment.
• Is located as close as possible to the boiler.
• Has adequate vehicle access to allow easy bulk delivery.
• Is fitted with appropriately sized delivery pipe work.
• Bulk fuel deliveries would normally blow fuel into store via a delivery
pipe.
• Delivery pipe work/bunker design should not cause undue fuel
breakage during delivery.
• Is sealed to prevent possible dust nuisance.
• Conveying air used for fuel delivery needs to be filtered prior to
discharge.
• Is sized to suit boiler load and likely bulk delivery payload.
• May need to be behind a fire rated wall if inside the plant room
(check with Building Control).
Pellet recovery from the fuel store would typically either be via Pick-up
auger(s) angled into the bunker or directly from the outlet of a coned
purpose built store or silo. From the bunker or silo the wood pellet fuel
is delivered to the transfer box of the stoker.
There are three key factors that influence the size of the pellet store.
1. Available Space - usually adjacent to or close to boilers - taking
account of best use of that space.
2. Estimated Fuel consumption.
3. The required frequency of delivery - or the size of delivery
anticipated.
Hoval can offer a number of silo based fuel store options or advise on
most appropriate use of available space for a bespoke build fuel
store.
Pellets feeding
into the BioLyt
boiler from the
flexible auger into
the boiler storage
container.
Fabric bag silo
gravity feeding
pellet into BioLyt
boilers through a
centreless flexible
auger.
RAS 41 pellet transportation system (only suitable for BioLyt 50 & 70)
Wood pellet store design and feeding system guidelines
8
Hoval BioLyt (50-160)