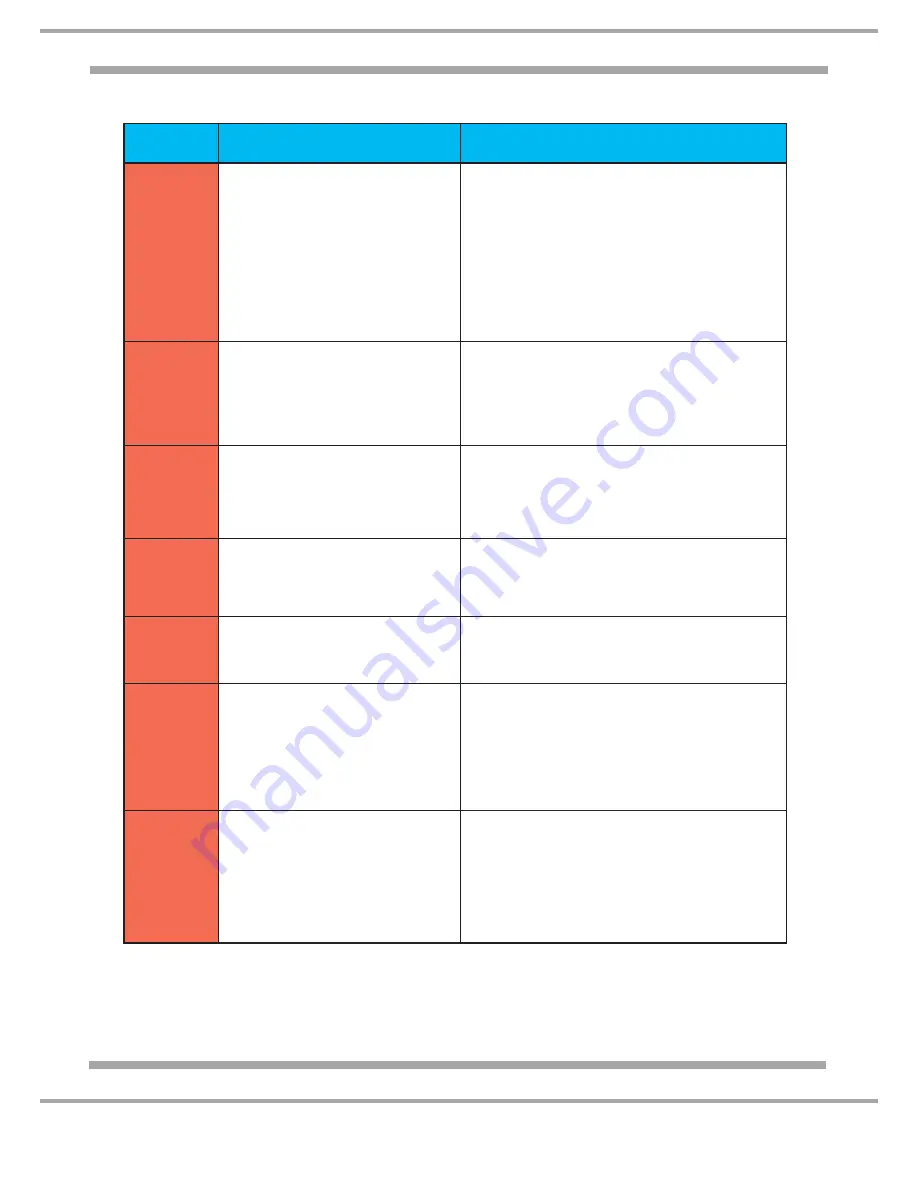
23 of 27
Whirlpool UK Appliances Ltd
Service Manual UK
English
- If status type pressure switch, check component directly;
- Check effi ciency of connector contacts on PCB;
- Check pressure switch wiring;
- Check continuity of pump on connector pins
4
and
5
(in case
of classic door lock), ensuring that impedance value is 170
1
+/- 10%;
- Check the wiring of pins
4
and
5
(/pump;
- Check pump fi lter, drain hose and wall drain outlet;
Reset the appliance with the OFF button, also after Fault resetting
with plug. Check the appliance pressure switches reaches full
without Faults at the next cycle;
- Replace the drain pump;
- Replace the linear pressure switch;
- Replace the main PCB.
- Check for water leaks that may affect connectors J
004
(collector)
or
J11
(three-phase) causing the relative contacts to short;
- Check the door lock terminal board (possible problems due to
aggression caused by manufacturing chemical residues that
may cause short circuits);
- Check
J004
/door lock wiring;
- Replace door lock;
- Replace PCB.
- Check effi ciency of contacts on connector
J001
(commutator) or
J10
(three-phase) on PCB;
- Check continuity of wash heating element on connectors
J001
(Commutator) or
J10
(Three-phase), pins
3
and
4
. The
1700W 230V heating element impedance value is 30 Ohm
+/- 10%. If value is different renew wash heating element;
- Renew
PCB.
- Check effi ciency of contacts on connector
J001
(commutator) or
J10
(three-phase) on PCB;
- Check leakage between the two ends and ground, impedance
should be at least 2 MOhm;
- Renew heating element;
- Renew
PCB.
- Disconnect appliance for 2 minutes. Check that correct operation
has been restored by starting the Autotest routine;
- Reprogram Main PCB;
- Renew main PCB;
- Renew display PCB.
- Check effi ciency of contacts on connector
J004
(commutator)
or
J11
(three-phase) on PCB;
- Check continuity on connector
J004
(commutator) or
J11
(three-
phase), pins
4
and
5
(in the case of classic door lock);
- Check continuity of pump, ensuring that impedance value is 170
Ohm +/- 10%;
- Check wiring of connector
J004
(commutator) or
J11
(three-
phase)/pump;
- Renew
pump;
- Renew
PCB.
- Check effi ciency of contacts on connector
J010
(Commutator)
or
J16
(Three-phase) on main PCB;
- Check effi ciency of contacts on Display PCB;
- Check continuity of
J010
(Commutator) or
J16
(Three-phase)/
Display PCB wiring;
- Disconnect appliance, wait for 2 minutes and reconnect to power
supply, then start autotest routine;
If problem persists proceed as follows:
- Renew main PCB;
- Renew display PCB.
Setting File error detected by Main PCB
or Display PCB
F09
Communication error between Main PCB
and Display PCB
F12
F08
Door lock fails to close/open, door lock
PTC triac open/closed, mains frequency
signal fault, mains power signal fault
Wash heating element relay open/diverter
relay sticking on drain pump side
Wash heating element relay earth leak-
age/wash heating element relay contacts
sticking
F07
F06
Pressure switch empty condition not
reached (valid for linear and status pres-
sure switch) or drain pump jammed (valid
for linear and status pressure switch)
F05
F11
Pump not wired or pump driving triac
short circuit
FAULT
SERVICE ACTIONS
CAUSE