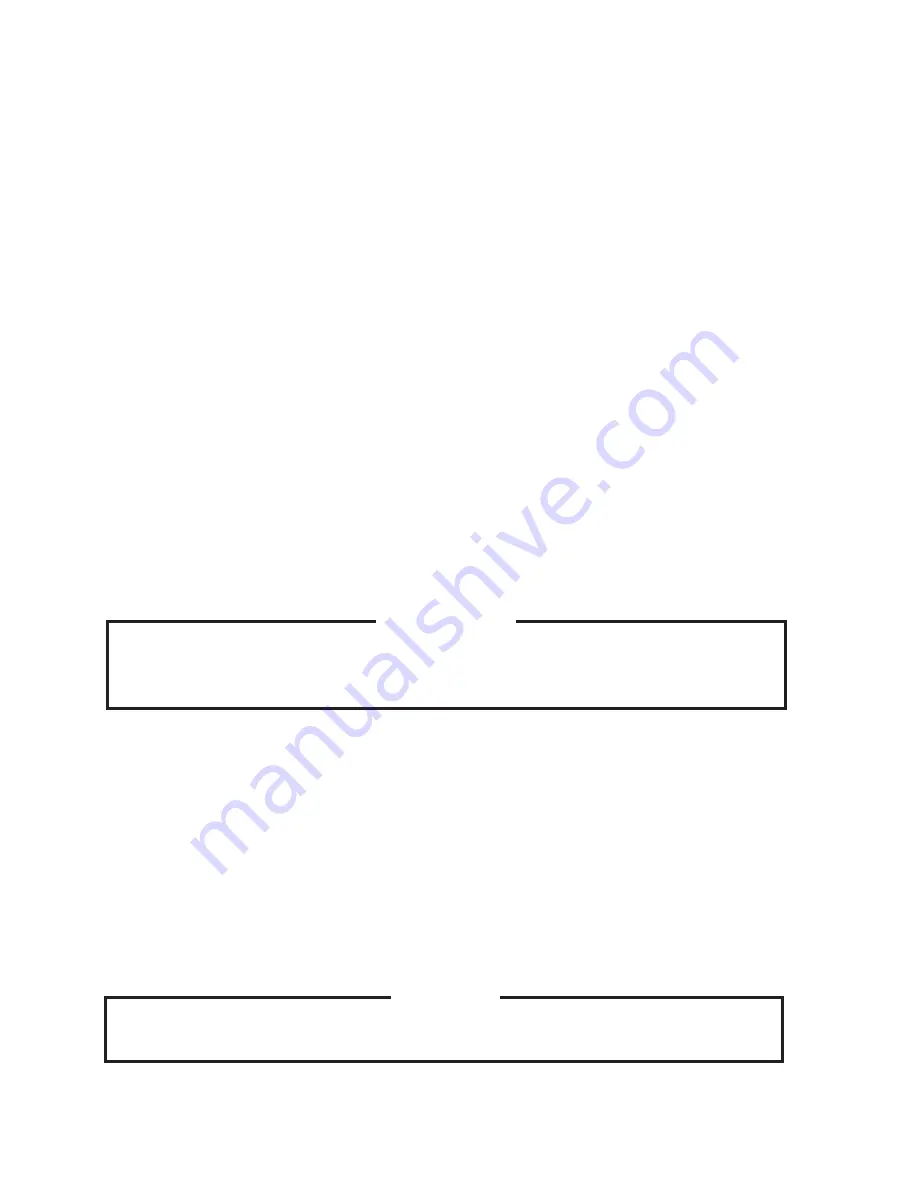
45
J. Adjustment of Water Regulating Valve - Water-Cooled Models
The water regulating valve (also called "water regulator") is factory-adjusted. No adjustment
is required under normal use. Adjust the water regulator, if necessary, using the following
procedures.
1) Prepare a thermometer to check the condenser drain temperature. Attach a pressure
gauge to the high-side line of the system.
) Five minutes after a freeze cycle starts,
confirm that the thermometer reads 104°F
to 115°F (40°C to 46°C). If it does not,
rotate the adjustment screw by using a flat
blade screwdriver until the temperature
is in the proper range. See Fig. 1. Next,
check that the reference pressure is in the
range indicated in the Head Pressure table
in the Performance Data section. If it is not
in the proper range, verify the refrigerant
charge.
3) Check that the condenser drain temperature is stable.
K. Removal and Replacement of Headmaster (Condensing Pressure
Regulator - C.P.R.) - Remote Air-Cooled Models
IMPORTANT
Always install a new drier every time the sealed refrigeration system is opened.
Do not replace the drier until after all other repair or replacement has been
made.
1) Turn off the power supply.
) Remove the panels from the remote condenser unit.
3) Recover the refrigerant and store it in an approved container.
4) Before heating, break off the stub on the dome to release the dome charge.
5) Disconnect the headmaster.
6) Place the new headmaster in position.
7) Remove the drier, then place the new drier in position.
8) Braze all fittings with nitrogen gas flowing at a pressure of 3 to 4 PSIG.
CAUTION
Always protect the headmaster body by using a damp cloth to prevent it from
overheating. Do not braze with the headmaster body exceeding 50°F (11°C).
Fig. 1
Adjustment Screw
CW – Higher
CCW – Lower
Top View